«Вяземское кожевенное производство» (ВКП ЛТ), расположенное в Смоленской области, на прошлой неделе объявило об открытии цеха по выпуску натуральных мебельных и обувных кож. С запуском нового оборудования компания, которая и раньше производила эти виды кож, нарастила мощности и потенциально способна увеличить объемы производства на 50%. Кроме того, предприятие укрепит свои позиции на рынке, увеличив долю присутствия с 7 до 11%, и потеснит импорт, который сейчас занимает, по собственной оценке ВКП ЛТ, 22% рынка.
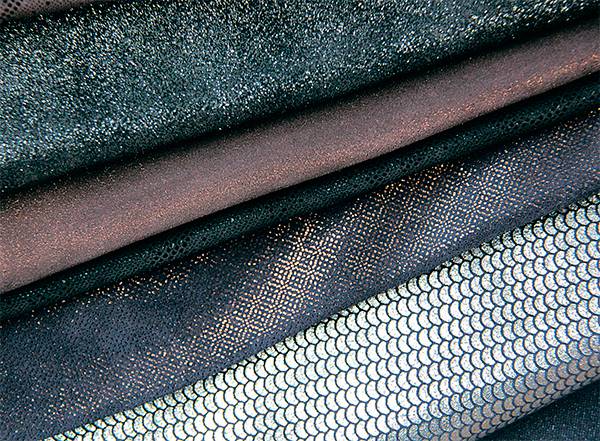
Расширение производства стало возможным благодаря займу, предоставленному Фондом развития промышленности (ФРП). Заявленная стоимость проекта составляет 386,6 млн рублей, из которых 271 млн ВКП ЛТ получило от ФРП в качестве займа на очень выгодных по нынешним меркам условиях: под 5% годовых на пять лет. Оставшаяся часть суммы, а это 115,6 млн рублей, — собственные средства кожевенного предприятия. «Для нас это очень ощутимая поддержка. Мы ежегодно выделяли 30–40 миллионов рублей собственных средств на текущий ремонт. Фактически за счет этого займа мы реализовали пятилетнюю программу модернизации», — говорит Анастасия Коброва, финансовый директор ВКП ЛТ. А поскольку спрос на продукцию ВКП ЛТ сейчас превышает предложение, компания рассчитывает, что с введением новых мощностей в несколько раз увеличится не только объем производства, но и выручка. Общие объемы производства завода сейчас составляют 109 тыс. кв. м кож, в планах — дойти до 150 тыс. кв. м, тогда как максимально возможные объемы — 180 тыс. кв. м. В этом случае проект может окупить себя за пять лет, а выручка завода к 2020 году достигнет 1,5 млрд рублей (за 2016-й она составила 822, 628 млн).

Бόльшая часть полученного займа — 187 млн рублей — была потрачена на закупку нового оборудования. Основное — красильно-шаровальные, разбивочные и дубильные барабаны, обессоливающий барабан, машина для шлифования кож, экспериментальный барабан и шкаф для разработки образцов. «Вся техника импортная, в России такую не производят», — рассказывает «Эксперту» Тимур Баркалая, генеральный директор ВКП ЛТ. Впрочем, за рубежом покупают не только технику, но и химические средства для обработки сырья, а они используются на всех этапах: кроме необходимых в технологии хрома и соли в России ничего не производят. В итоге импорт в себестоимости составляет 25%.
Оставшуюся часть средств направили на разработку артикулов кожи, покупку сырья и химии для создания опытных образцов.
Ставка на обувь
Поначалу завод производил полуфабрикат, который в основном шел на экспорт. В конце 1990-х предприятие запустило производство крастов (кожа без лицевой отделки) и мебельной кожи. Объемы выпуска на тот момент составляли порядка 50–60 тыс. кв. м в месяц. Основной объем производства приходился на кожу для мебели. Но в 2011 году существенно упал спрос на кожаную мебель, и компания стала терпеть убытки. В тот период пост генерального директора занял Тимур Баркалая. С его приходом завод переориентировался на производство новой линейки кож: для обуви, для рабочей одежды — и спилка (велюр или замша). «Для переориентации на новое производство в первую очередь нам были нужны рецепты производства кожи. Оборудование для производства полуфабриката у нас уже было, и его вполне можно было использовать для нового производства. Для изготовления спилка и обувной кожи завод купил новый пресс и барабаны», — говорит Анастасия Коброва.
Сейчас завод производит мебельную, галантерейную и обувную кожу, спилок велюр и кожу для рабочей одежды. Компания планирует начать производство нового вида кожи — лакированной. Бόльшая часть выпуска в настоящее время приходится на обувную кожу, меньшая — на мебельную. «Сейчас доля мебельной кожи в нашем производстве около 15–20 процентов, остальное — это обувная и галантерейная, но в основном обувная, ее доля составляет 64 процента. Кожа для обуви будет всегда пользоваться спросом, потому что альтернативы натуральной коже нет. А что касается мебельной, то для нее сейчас альтернатива есть — это прежде всего текстиль», — говорит Тимур Баркалая. Самые маленькие объемы в настоящий момент приходятся на кожу для рабочей одежды. «Кожа для рабочей одежды сейчас небольшой рынок. Здесь используют недорогую кожу (спилок). Раньше он либо уходил в отходы, либо его продавали как полуфабрикат, сейчас же отходов в производстве фактически нет», — рассказывает Анастасия Коброва.
Рост объемов производства обувной кожи связан с тем, что российская кожа с недавнего времени пользуется высоким спросом у отечественных обувных компаний. «Российские производители обуви покупают в основном отечественную кожу. Сейчас на рынке уже есть качественные производители кожи, да и отечественный продукт к тому же дешевле импортного, — рассказывает Тимур Баркалая. — Нашей кожей заинтересовалась обувная фабрика Ralf Ringer, до 20 процентов продаем им».
Впрочем, компания значительную часть продукции производит на экспорт: в 2016 году на него пришлось 30% объема производства. Три четверти идет в Италию, четверть — в Индию, Китай и другие страны.
Сырье подтягивается
Само «Вяземское кожевенное производство» работает исключительно с отечественным сырьем по той же причине, что и обувщики. Во-первых, это дешевле, во-вторых, в России сейчас можно найти качественные шкуры. «Качество сырья зависит больше не от продавца — бойня это или мясной комбинат, а от региона: хорошие среди них Центральный, Поволжье, Северо-Запад. Юг по качеству сырья хуже всего: в теплый период там много насекомых. Бόльшую часть продукции мы покупаем на бойнях в центральной части России», — говорит Анастасия Коброва. «Не очень хорошее сырье и на севере: там нет пастбищ и рацион животных ограничен, что в свою очередь отражается на качестве», — полагает Тимур Баркалая.
Введенный в 2014 году запрет на экспорт полуфабриката вет-блю стал для отечественных кожевенных заводов серьезным толчком в развитии, поскольку ранее значительная часть сырья (около 30%) вывозилась за границу, из-за чего на внутреннем рынке возникал дефицит. «Очень многие поставщики сырья осуществляли самую простую обработку и продавали товар за границу. В результате наши заводы оставались недозагруженными. Рынок шкур в России ограниченный, и, если бы не было запрета на вывоз полуфабриката, нам пришлось бы покупать шкуры дороже, началась бы ценовая конкуренция, и это отразилось бы на ценах конечной продукции для тех, кто производит обувь», — говорит Анастасия Коброва.
По качеству сырье можно разделить на три группы: лицевая кожа — сырье высокого качества, оно фактически не обрабатывается — лишь подвергается очень легкому окрашиванию. Второй тип кожи обрабатывает шлифовальная машина. Третий вид — плита — это самые низкие сорта кожи, их подвергают значительной обработке, в результате которой внешние дефекты сырья скрываются под рисунком, имитирующим естественный рисунок кожи — зерненый. Оборудование «Вяземского кожевенного производства» позволяет изготавливать все три типа кожи, но ориентировано оно на выпуск кожи самого высокого качества. «Дорогая лицевая кожа в России стоит 2500 рублей за квадратный метр, а самая дешевая — 500 рублей. Мы продаем дорогую, но есть и дешевая — такую кожу может дать производственный брак или очень низкие сорта сырья. Это пять-десять процентов от общего объема», — рассказывает Тимур Баркалая.
Поступающее на фабрику засоленное сырье проходит три основных этапа обработки: вет-блю, краст и финиш. Каждый из них одинаково важен — он влияет на качество конечного продукта. На первом этапе, вет-блю, шкуры запускают в барабан, где они обрабатываются хромом и дубятся, и в результате появляется хромированный полуфабрикат голубого оттенка. На втором этапе дубильную кожу двоят, строгают и запускают в разливочные барабаны, и в итоге получается краст. Затем осуществляют вторичную покраску в красильных барабанах — получается готовый продукт.
Работа на заказчика и большой ассортимент
Всего в России порядка 15 кожевенных заводов, некоторые из них находятся в предбанкротном состоянии, другие производят только полуфабрикат вет-блю, и лишь небольшая часть предприятий изготавливают качественную кожу. Маржа успешных компаний невысока: не более 15%. Отчасти это объясняется сложившейся организационной структурой производств.
«Объемы выпуска “Вяземского кожевенного производства” очень большие. В Италии в принципе нет вертикально интегрированных производств. Этот объем в Италии приходится на несколько заводов, у нас четкое разделение: одни делают только сырье, другие — только краст, третьи — только готовый продукт. Компаниями с полным производственным циклом трудно управлять — это колоссальная работа. Еще для этого нужен большой рынок сырья. Создавать вертикально интегрированные производства могут, например, Бразилия и Аргентина, где есть много сырья. Европейские производители не могут», — говорит Марко Калеаро, руководитель продаж и закупок итальянской обувной компании Thimeco.
Основные конкуренты вяземского кожевенного предприятия — АО «Русская кожа», расположенное в Рязанской области, и ЗАО «Хром» из Ярославской области. Это крупные заводы — они производят кожу для обуви и одежды, галантерею. «Если с “Хромом” у нас сопоставимые объемы выпуска, то “Русская кожа” производит в три-четыре раза больше продукции. Рязанский завод производит все, в том числе кожу для автомобилей. Ярославский специализируется на изготовлении кожи для обуви и для ремней», — говорит Анастасия Коброва.
Свои конкурентные преимущества «Вяземское кожевенное производство» видит в большом ассортименте артикулов и широкой цветовой палитре.
Кроме того, предприятие работает под заказ и фактически ничего не производит на склад, кроме разве что кожи черного и коричневого цвета, которая пользуется стабильным спросом. Работа под заказ позволяет избежать рисков и гибко реагировать на спрос. «У завода гигантский ассортимент — около 43 артикулов. Поскольку в России кожевенный рынок небольшой, то, чтобы выжить, нужно быть универсальным, при этом не теряя в качестве», — считает Тимур Баркалая.