Станкостроение для Липецкой области не терра инкогнита. Липецкий станкостроительный завод с середины 1950-х выпускал плоскошлифовальные станки. Тогда старт этого производства позволил стране отказаться от импорта подобного оборудования. Более того, продукция из Липецка шла и на экспорт. Всего за время существования завода было выпущено около 56 тыс. станков.
Однако к середине 2000-х предприятие практически перестало работать, а его главный производственный корпус, расположенный в центре Липецка, и вовсе был перестроен в торгово-развлекательный центр «Европа».

Но свято место пусто не бывает, и на обломках завода возникли новые производства.
ЗАО «Липецкое станкостроительное предприятие» (ЛССП) — одно из них. Это семейное предприятие, учредители которого — Владимир Петров и два его сына, Владимир и Кирилл.
Петров-старший долгое время работал на Липецком станкостроительном на руководящих должностях. «Когда мы начинали свой бизнес, я сыновьям сказал: работаем не на карман, а на развитие. Согласились». Сейчас он, по собственному признанию, потихоньку отходит от дел: «Ребята сидят тут крепко. Захотят от бизнеса освободиться — не освободятся, потому что он непродаваемый. Это тяжелый, малодоходный бизнес. Окупается очень долго. Детям моим до тризны его тащить на себе, а дальше — их детям».
Владимир Петров-младший сейчас директор ЛССП. «Сколько себя помню, отец работал на станкозаводе. Я ходил в садик, подшефный заводу, в подшефную школу, по направлению от завода учился в институте, проходил практику на заводе».
Станочный семейный бизнес начался с ремонта старых станков, которые предприимчивые липчане сдавали в металлолом. Петровы выкупали станки по цене чуть выше лома, реанимировали и продавали. «Многие пальцем у виска крутили: целый завод не может справиться с реализацией, куда вы лезете? Но спрос был, ведь восстановленные станки были раз в десять дешевле новых», — вспоминает генеральный директор ЛССП.
Постепенно перетянули на себя часть незавершенных заказов «старого» завода и уже в 2006-м начали производить собственные новые станки, организовали свой конструкторско-технологический отдел.
«Наша преимущество в том, что у нас очень мощная собственная электрическая часть, силовая монтажная схема и программное обеспечение. Можно вручную станком управлять — за веревки дергать или штурвалы крутить, а можно поставить электрику и только кнопки нажимать. В стране не хватает квалифицированных рабочих. В подготовке кадров — двадцатилетний пробел. Люди, которые работали раньше, чувствовали металл. Микроны на глаз ловили. Теперь так не умеют. И потому мы создали систему, когда станком управляет не станочник, а оператор. Один квалифицированный технолог пишет программу обработки детали, вносит ее в компьютер. Оператору нужно установить заготовку на станок, выбрать программу и запустить ее. Высокой квалификации не требуется. Да, мы тут не уникальны, но гордимся тем, что это наша собственная система», — рассказывает Владимир Петров.
Новый импульс развитию предприятия дал предыдущий кризис. С августа 2008 года по август 2009-го на расчетный счет завода не поступило ни копейки. Завод работал на склад. Часть рабочих ушла. После этого было принято решение расширить номенклатуру выпускаемых станков и усилить научную составляющую: «В СССР было разделение: Оршанский станкозавод делал маленькие шлифовальные станки, Липецкий — средние, Воронежский завод — крупные, тяжелые. Мы начинали со средних, а теперь делаем полный спектр плоско- и круглошлифовальных станков».
Еще одним следствием кризиса стало желание акционеров иметь такую подушку безопасности, чтобы завод в течение двух лет мог работать на склад, не продавая ни одного станка. И при этом покупать комплектующие и платить заработную плату работникам.
Сегодня на заводе внедрена Hubbard Management System. «Эта система управления используется многими мировыми компаниями, такими как Mercedes, Volkswagen, Audi, — говорит Владимир Петров. — У нас каждое подразделение и каждый сотрудник знают, какой ценный конечный продукт они производят. Внедрена система еженедельного планирования и еженедельного отчета, собирается еженедельная статистика по различным параметрам».
После кризиса ЛССП продолжило активно развиваться. Провал 2009 года был быстро ликвидирован — выручка предприятия ежегодно растет более чем на 30%.
«Любая компания всегда хочет потратить денег больше, чем у нее есть. У нас четкий контроль: мы никогда не тратим в неделю денег больше, чем за неделю же и заработали, — рассказывает Петров. — На текущую деятельность мы не берем кредиты очень давно — зачем нам кормить банковских работников, если мы можем поощрять своих? У нас зарплата привязана к доходу, есть стабильный оклад, а есть премия, размер которой зависит от того, сколько заработала компания. На ее развитие мы копим деньги. А также участвуем в различных федеральных и региональных программах. Получаем финансирование через них».
Даешь кластеризацию!
Во времена СССР в связке со станкозаводом в Липецке работало предприятие «Центролит». Оно поставляло ему отлитые из чугуна станины. Но к 2009 году «Центролит» закрылся. По словам Владимира Петрова, в России больше нет такого производства. Потому приходится покупать чугунное литье в Китае. Или — второй вариант — использовать станины, бывшие в употреблении: «Мы берем старый станок, выкидываем все, кроме чугуна. Его обрабатываем и на этом основании собираем новый станок».
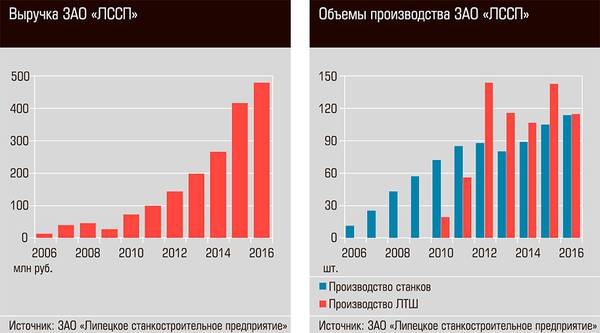
Впрочем, есть и третий вариант — возродить российское производство чугунного литья.
Несколько лет назад власти обратили внимание на плачевное состояние отечественного станкостроения. Сначала в рамках федеральной целевой программы «Национальная технологическая база» в 2011 году была принята подпрограмма «Развитие отечественного станкостроения и инструментальной промышленности на 2011–2016 годы». В 2013-м — постановление правительства РФ № 1224, которое, по сути, ограничивало присутствие на российском рынке иностранных компаний, доля которых, кстати говоря, к этому моменту составляла порядка 90%.
А в середине 2015 года было принято постановление № 719. В нем четко определены критерии отнесения произведенного на территории страны станка к отечественным, в том числе обозначены сроки перехода на использование при сборке станков определенной доли иностранных комплектующих. Так, с 1 января 2020 года станок будет признаваться российским, только если доля иностранных комплектующих в нем не будет превышать 30%.
Сегодня главный заказчик для станкостроителей — предприятия ОПК. У них есть и деньги, и потребность в новом оборудовании. И, что немаловажно, покупать в целях обеспечения государственной безопасности они должны в первую очередь станки российских производителей.
По признанию Владимира Петрова, сейчас завод практически ничего не отправляет на экспорт, так как растет спрос внутри страны. При этом генеральный директор ЛССП уверен, что российские универсальные станки не уступают по качеству зарубежным: «Мы проигрываем в маркетинге, но в целом наши станки на уровне. Даже немцы готовы их покупать, потому что они при сопоставимом качестве дешевле немецких. Так что мы будем и дальше развивать экспортное направление».
Отметим, что заметную роль в том, что государство протянуло руку помощи (в которой, кстати говоря, оно держит деньги) станкостроителям, сыграли и санкции.
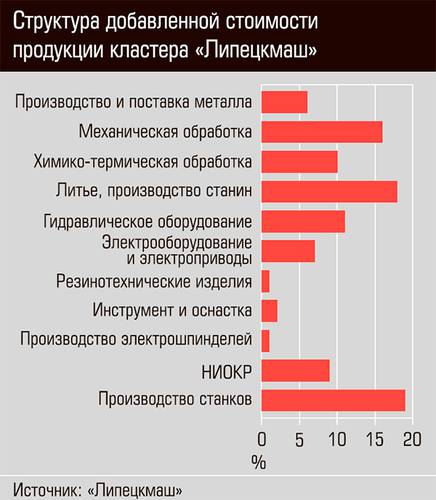
Летом 2015 года в Липецкой области был создан станкостроительный кластер «Липецкмаш», а затем и одноименная компания для координации деятельности участников кластера. Одним из 12 ее учредителей стало и Липецкое станкостроительное предприятие.
Сейчас, по словам генерального директора «Липецкмаша» Олеси Поповой, в кластере 42 участника. Помимо собственно промышленных предприятий это научные и образовательные учреждения, а также институты развития и инфраструктурные организации.
В рамках кластера участники отстраивают кооперационные связи, планируют организацию новых производств, продукция которых будет использоваться при сборке станков.

По словам Владимира Петрова, чем больше комплектующих станкостроительное предприятие покупает на стороне, тем выше у него рентабельность. Производить самостоятельно в малых количествах какие-то отдельные детали невыгодно. Впрочем, иногда приходится —ради обеспечения производственной безопасности. Например, у завода были сложности с покупкой резинотехнических комплектующих. Пришлось приобрести собственное оборудование для их изготовления, которое задействуется два раза в год. Потом полученная продукция пересыпается тальком и отправляется на склад. Остальное время этот пресс простаивает. Исполнять сторонние заказы невыгодно, так как нужна дорогостоящая оснастка, вложения, которые непонятно когда окупятся, поиск заказчиков и прочие расходы. Производитель комплектующих с широким кругом клиентов вполне мог бы зарабатывать.
Сегодня, по сути, любой предприниматель может прийти в кластер и спросить: «А что вам нужно? Я готов организовать производство». Участие в кластере позволяет получить поддержку как финансовую, так и организационную.
Ты мне — я тебе
Как рассказала «Эксперту» Олеся Попова, сейчас в высокой стадии готовности к реализации в кластере «Липецкмаш» находятся четыре проекта.
Проект «Станина» предполагает организацию производства станин и базовых станочных узлов из чугунного литья и композитных материалов. Проект будет реализован на базе компании «Свободный сокол». Она специализируется на изготовлении труб для питьевого водоснабжения и водоотведения. Это предприятие — единственный в России производитель труб из высокопрочного чугуна с шаровидным графитом. Его доля на российском рынке труб для инженерных коммуникаций в сфере ЖКХ составляет 25%. Общая стоимость проекта «Станина» — 1,97 млрд рублей. За счет собственных средств будет профинансировано 50% стоимости проекта, вторая половина — деньги из федерального бюджета. В качестве частных инвесторов в этом проекте задействованы сам завод «Свободный сокол» и ПАО «СТП — Липецкое станкостроительное предприятие», которое возглавляет Кирилл Петров.
Второй проект — «Флюидмаш». Он предполагает создание производства гидро- и пневмоаппаратуры для комплектации металлорежущих и металлообрабатывающих станков, а также другого гидрофицированного оборудования. Общая стоимость проекта — 1 млрд рублей. Как и в первом случае, финансирование проекта в равных долях — по 500 млн рублей — обеспечивают его частные инициаторы и государство. Здесь инвесторами выступают три предприятия — «Гидропривод», «Елецкгидроагрегат» и «Гидравлик». Наибольшую долю — 400 млн рублей из 500 млн — внесет «Гидропривод». На двух других участников придется по 50 млн рублей.
В третьем проекте — «Генборг» — предполагаемая доля финансирования из федерального бюджета менее 50% — 380,4 млн рублей из 1,356 млрд. Впрочем, 330 млн рублей АО «Генборг» получило из Фонда развития промышленности в виде займа под 5% годовых.
Проект предполагает организацию производства широкой гаммы низковольтных электродвигателей, которые соответствуют классу энергоэффективности IE3 (премиум). В дальнейшем «Генборг» планирует модернизировать двигатели до класса IE4 (суперпремиум). В России продукция такого класса почти не производится.
К 2019 году предприятие планирует занять от пяти до восьми процентов российского рынка. Основные конкуренты — компании ABB, Siemens и WEG. Одним лишь российским рынком «Генборг» ограничиваться не намерена: до 30% продукции компания планирует поставлять в страны СНГ, порядка 10% — в страны дальнего зарубежья.
Примечательно, что завод «Свободный сокол» в рамках проекта будет изготавливать для двигателей «Генборг» корпуса из высокопрочного чугуна, а также станины. «Свободный сокол» частично профинансирует проект, вложив в него 22 млн рублей.
В дальнейшем двигатели «Генборг» будут использоваться при реализации четвертого проекта кластера «Липецкмаш», который разрабатывается компанией «Интермаш». Он предполагает создание производства инновационных обрабатывающих фрезерных, токарных и шлифовальных центров с применением отечественной системы ЧПУ. Среди инициаторов проекта — ЛССП и «СТП — Липецкое станкостроительное предприятие». Согласно программе развития «Липецкмаша» стоимость проекта — 1,884 млрд рублей. Затраты частных инвесторов и государства поделены пополам. Основная часть выплат со стороны частного инвестора придется на компанию «Интермаш» — 565,2 млн рублей. Компании, которые возглавляют Владимир и Кирилл Петровы, выделят на проект по 188,4 млн рублей каждая.
Таким образом, по всем четырем проектам суммарные инвестиции из федерального бюджета составляют 2,807 млрд рублей, внебюджетные средства — 3,403 млрд.
В случае успешной реализации программы развития кластера «Липецкмаш» ожидается, что объемы произведенной здесь продукции вырастут в полтора раза — с 10 млрд рублей в 2016 году до 15 млрд рублей в 2020-м, доля инновационной продукции в этот же период увеличится более чем вдвое — с 44 до 91%, доля продаж продукции предприятий кластера на российском рынке вырастет в четыре раза — с 5 до 20%, а налоговые отчисления достигнут 7,7 млрд рублей в год. Судя по заявленным цифрам, федеральный бюджет внакладе не останется.