Мы не опоздали и не отстали. Мы медленно спускаемся с холма, слегка поскальзываясь на мокрой траве, обходя крупные валуны и глинистые участки. Массовое промышленное производство по аддитивным технологиям с использованием металлических порошковых композиций в России будет. Уже есть. Еще не в том объеме, в каком хотелось бы, но и присущие нашей стране проблемы на пути внедрения нового способа производства никто не отменял.
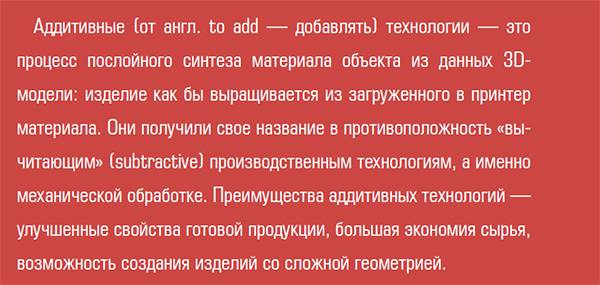
После введения санкций против России в 2014 году процесс распространения аддитивных технологий в реальном производстве затормозился. Это произошло из-за того, что стало сложнее покупать иностранные машины и связанные с ними продукты, те же порошки. Кроме того, возникло опасение, что даже проданный российскому предприятию промышленный 3D-принтер в какой-то момент может перестать работать или обслуживаться. Потому что его производитель так решил. Вернее, подчинился указанию своего правительства. Учитывая, что основные покупатели этих устройств — предприятия, связанные с обороной, такие опасения не напрасны. Но нет худа без добра: активизировался процесс разработки собственных аддитивных машин и всего с ними связанного. То самое импортозамещение. Причем на некоторых направлениях это даже не импортозамещение, а, как выразился вице-президент по техническому развитию Объединенной судостроительной корпорации Дмитрий Колодяжный, «импортоопережение».
Уже сегодня в России тысячами штук выпускаются бытовые 3D-принтеры, которые активно используются для прототипирования, например в учебных заведениях, с младых ногтей прививая будущим инженерам и конструкторам привычку применять эти технологии в своей работе. Нет особых проблем с выпуском и использованием в реальном производстве машин для изготовления пресс-форм и литейной оснастки.
Однако пока мы не можем похвастаться ни одной серьезной промышленной серийной аддитивной машиной, использующей в качестве материала для печати металлические порошковые композиции. А именно за такими машинами будущее аддитивного производства, поскольку на них можно массово выпускать конечные изделия с наибольшей добавленной стоимостью.
Впрочем, судя по всему, мы сможем сделать это в ближайшее время. И количество отечественных принтеров, которые рассчитывают продать их разработчики и производители, в несколько раз превышает число этих устройств, имеющихся в стране сегодня.
Боги машин
Мы делаем где-то 60 машин в год разных типов. Сейчас строится новый завод. Он позволит еще 40–50 машин делать. Так что наша мощность к следующему году будет около 100 машин в год. То есть мы можем без проблем делать 20–30 аддитивных машин в год.
Дмитрий Сапрыкин, группа компаний «Лазеры и аппаратура»
По данным Минпромторга, сегодня в России эксплуатируется порядка 600–650 промышленных 3D-принтеров. Из них лишь около 10% — это аддитивные машины, работающие с металлическими порошками.
В стране осуществляется несколько проектов создания отечественной аддитивной машины, использующей в качестве материала для выращивания изделий металлические порошки. Причем в рамках этих проектов происходит не столько заимствование и повторение уже существующих технологий, сколько создание своих собственных. «Эксперт» уже рассказывал об одной такой разработке в статье «Русский аддитивный прорыв» (см. № 12 за 2017 год).
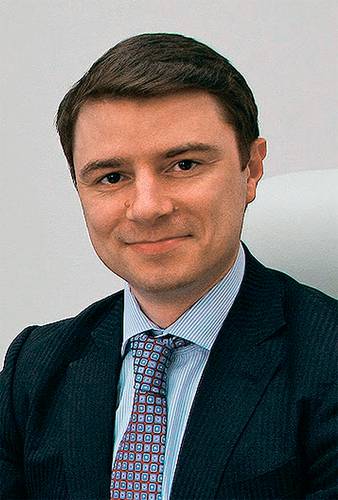
И это не единственная новация: «В России есть разработки, которые по постановке задачи уже сегодня опережают Запад на два-три года, — рассказывает директор департамента станкостроения и инвестиционного машиностроения Минпромторга Михаил Иванов. — К примеру, Научно-исследовательский физико-технический институт ННГУ имени Лобачевского совместно с ЗАО НИИ ЭСТО при поддержке Фонда перспективных исследований выполняет проект, цель которого —разработка технологии и соответствующего оборудования для производства многопорошковых металлических изделий сложной формы методом послойного лазерного сплавления (ПЛС). Использование многопорошковой ПЛС-системы открывает широкие перспективы для изготовления сложнопрофильных изделий, связанные с возможностью реализации новых “полиметаллических” конструкций, а также со снижением сроков и стоимости изготовления изделий. В настоящее время аналогов таких многопорошковых ПЛС-систем в мире не существует».
Научно-исследовательский институт электронного специального технологического оборудования (ЗАО НИИ ЭСТО) создан более десяти лет назад как исследовательский центр в группе компаний «Лазеры и аппаратура» (ЛиА). ЛиА в свою очередь занимается производством лазерного промышленного оборудования для обработки металлов. Она была образована в 1995 году в Зеленограде. Сегодня на этой площадке производится более 30 серийных моделей лазерного оборудования для всех основных технологий обработки металлов: микрообработки, маркировки, резки и раскроя, сварки. По ряду направлений ЛиА — единственный производитель в России.
Что касается машин для аддитивного производства, то здесь компания взялась за создание 3D-принтеров, работающих по двум технологиям: первая — наиболее распространенная технология послойного лазерного спекания, SLM, вторая — прямое лазерное осаждение, LMD, когда порошок в нужную точку подается из лазерной головки, что позволяет выращивать изделие в любую сторону, по пяти координатам. Поскольку до того, как заняться аддитивными технологиями, компания выпускала пять серий лазерных машин, а новые отличаются высокой степенью унификации с ними, то они, соответственно, стали машинами шестой и седьмой серий. В целом в аддитивные проекты было вложено порядка 200 млн рублей.

Первые экземпляры уже собраны и проходят испытания. Эти машины готовят к серийному выпуску. И продолжают разрабатывать технологию печати с использованием нескольких порошковых композиций одновременно: «На одной из конференций выступали представители немецкой компании SLM Solutions, — рассказывает генеральный директор НИИ ЭСТО Дмитрий Сапрыкин. — И вот они говорят, что на них работает пятьдесят ученых, десять университетов. И это действительно так. Фронт работ здесь колоссальный. Это сравнимо с тем, как создавалась традиционная металлургия, когда ученые всего мира с середины девятнадцатого века изучали, как ведут себя металлы, каковы их свойства, какие нужно применять процессы обработки, чтобы добиться нужных результатов. И только где-то к середине прошлого века этот объем знаний в целом был накоплен. Надеюсь, здесь сто лет все-таки не понадобится. Но куда бы ты ни пришел — в Европе, в Азии сидят профессора со студентами и постоянно ведут эксперименты по аддитивным технологиям. На самом деле они, как и мы сейчас, находятся в первой фазе изучения. То есть пока мы не отстали. Нам надо создать свою машину, чтобы наша наука изучала все эти процессы на российском оборудовании. Потому что западные машины ориентированы на свое обслуживание, ПО и комплектующие».
С точки зрения взаимодействия с наукой в данном случае все хорошо: как уже было сказано, многопорошковая аддитивная машина создается в партнерстве с Нижегородским университетом.
В компании поставили себе задачу сделать свою аддитивную машину универсальной — она должна уметь работать с разными программными продуктами, как российскими, так и иностранными. Для этого создается специальная программа, способная сопрягать принтер и файлы, в которых содержится информация о предлагаемой к печати детали: «Мы надеемся здесь на широкую кооперацию, — говорит Дмитрий Сапрыкин. — Неправильно, когда кто-то держит все в одних руках. Вот у Siemens, например, цепочка программных продуктов полного цикла, и он предлагает полностью переходить на его продукцию. Решение хорошее, но дорогое, и потребитель навсегда привязывается к этому производителю. У нас же концепция — максимальная открытость».
Максимальная открытость и — обязательно — кооперация с другими участниками рынка, обмен информацией. Именно за счет этого, по мнению Дмитрия Сапрыкина, российским производителям аддитивной техники можно будет успешно конкурировать с западными:
«Российская империя была одним из мировых лидеров по производству паровозов. За счет чего? Оказывается, частные заводы были объединены в своего рода консорциум, который координировало Министерство путей сообщения. Они практиковали широкую унификацию своих изделий, из-за чего серийность русских локомотивов была одной из самых высоких в мире. Частные заводы тесно взаимодействовали с университетами и государственными научными лабораториями. Созданные при финансовом участии государства разработки очень быстро поступали в производство. Сейчас ситуация другая. Кооперация между предприятиями слабая, взаимодействие заводов с университетами в зачаточном состоянии, унификации нет вообще. Нам сейчас нужно думать о развитии кооперации между фирмами и о том, чтобы созданные в рамках государственно-частного партнерства результаты интеллектуальной деятельности без задержек шли в серийное производство на тех самых предприятиях, которые их создали. В части ПО это особенно актуально.
Иначе мы постоянно будем тормозить сами себя и не сможем конкурировать с гигантами типа General Electric или Siemens. Но и эта кооперация должна быть взаимовыгодной. Если у нас просто заберут наши разработки, скажут спасибо и передадут кому-то другому, нам это не понравится».
Что касается конкурентоспособности произведенных зеленоградской компанией аддитивных машин с точки зрения цены, то руководство уверяет, что они будет примерно на 40% дешевле импортных аналогов.
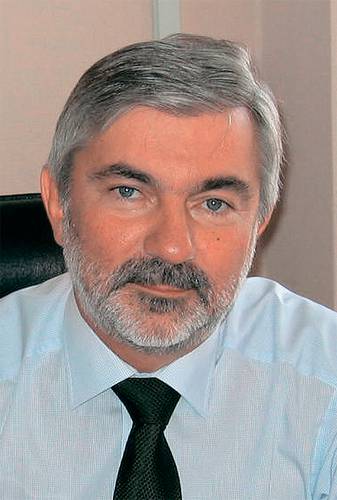
— Сколько человек работало надо созданием принтера?
— Не много.
— Не много — это десять, пятьдесят или сто?
Задумывается, подсчитывая про себя, и после паузы:
— Пятеро.
Из разговора с Владимиром Береговским (ЦНИИТМАШ)
В 2014 году Министерство образования объявило конкурс на разработку и изготовление аддитивной машины, работающей по технологии SLM (селективное лазерное плавление). По условиям конкурса также нужно было разработать и изготовить не только саму аддитивную машину, но и две технологии изготовления порошковых материалов: из нержавеющих сталей и из титановых сплавов.
В итоге разработкой аддитивной машины занялась команда во главе с Владимиром Береговским, заместителем генерального директора — директора Института технологии поверхности и наноматериалов АО «НПО “ЦНИИТмаш”», входящего в структуру госкорпорации «Росатом».
Объем финансирования составил 300 млн рублей на три года.
«Безусловно, разработка велась не на пустом месте, — рассказывает Владимир Береговский. — Мы давно занимаемся разработкой высокотехнологичного оборудования, в том числе в области вакуумных ионно-плазменных процессов. Поэтому мы это достаточно просто решили».
Собственно, аддитивная машина появилась уже в начале 2016 года: «Я хочу сказать, что машина — это просто железо, а вот мозг машины и система управления — это, конечно, сложно. Пакет программных продуктов, который мы тоже разработали, уникален. Наше программное обеспечение, обрабатывая трехмерную модель, само программирует машину для производства конкретного изделия. То есть не человек закладывает какие-то параметры работы машины, скажем, скорость перемещения луча, толщину слоя, температуру, а сама программа, поняв задачу и исходя из трехмерной модели детали и материалов, из которых она изготавливается, программирует машину на производство».
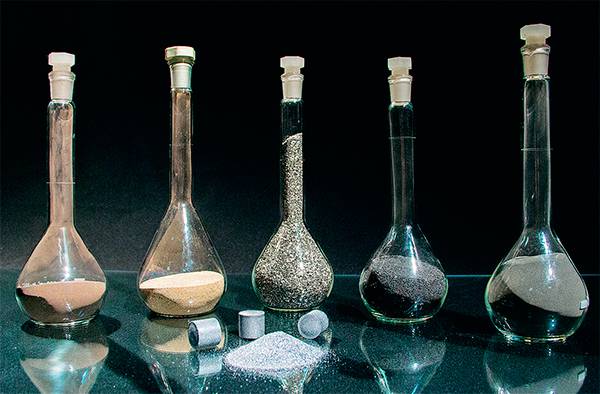
Сейчас — новый проект. Следующее поколение машины Береговский и компания разрабатывают в партнерстве с МИСиС и СПбПУ. В проекте участвуют АО «Наука и инновации» (координирует научную работу в госкорпорации «Росатом»), Уральский электрохимический комбинат. Индустриальным партнером выступает компания ТВЭЛ:
«Эта машина уникальная, таких машин еще нет на зарубежном рынке, — поясняет Владимир Береговский. — Помимо того что она будет работать с двумя лазерами (хотя это не новость, такие машины есть), она будет работать еще и с двумя материалами. То есть мы получим изделие, состоящее сразу из двух материалов. Что это значит? Очень наглядный пример — диск турбины авиационного двигателя. Он еще называется блиск турбины, это диск плюс лопатки. Сам диск состоит из одного никелевого жаропрочного сплава, а лопатки — это другой жаропрочный никелевый сплав, с повышенными свойствами по жаростойкости, по жаропрочности. Вот такое изделие можно сделать за один раз: сам диск будет состоять из одного материала, а лопатки — из другого».
По словам Владимира Береговского, прежде чем запустить созданные машины в серию, необходимо провести ряд испытаний, изучить свойства используемых материалов и изделий, получаемых по аддитивной технологии, добиться необходимых свойств и от материалов, и от изделий: «Мы недавно были на конференции, которую устраивала одна из ведущих фирм в этой области — бельгийская компания Materialise. И вот, побывав на этой конференции, говорить о том, что мы так уж отстаем, я бы не стал. Потому что у нас очень хорошая металловедческая наука, а все процессы, связанные с плавлением, — это металловедение чистой воды. У нас очень хорошие лазерщики, мы имеем возможность делать очень хорошие мехатронные узлы. Конечно, они на Западе уже много лет занимаются вопросами технологии. Это очень сложное и очень важное в этих процессах, но, в общем-то, мы все это тоже делаем».
Владимир Береговский оценивает в 70% локализацию созданных его командой машин. И этот процент будет расти: «В первой установке трехосевая сканирующая система — американская. В следующей — немецкая. Но дальше машины будут уже оборудованы отечественными сканирующими системами. У нас есть свой, российский производитель, который делает такие системы». Высокий уровень локализации позволит держать цены как минимум на 20% ниже, чем у иностранных аналогов, считает Владимир Береговский.
Сейчас на машинах установлены лазеры американской компании IPG, производственные мощности которой расположены в том числе в подмосковном Фрязино. Однако Владимир Береговский рассчитывает, что в будущем их заменят лазеры, сделанные одним из предприятий «Росатома»: «Нам было интересно использовать интеллект “Росатома”, который, по моим соображениям, соизмерим с интеллектуальным потенциалом какой-нибудь небольшой европейской страны».
Несмотря на то что серийного выпуска еще нет, спрос на машины уже есть: «Спрос достаточно большой, мы это ощущаем. И даже ощущаем, что вот-вот исчезнет некий психологический барьер, который сдерживает широкое внедрение, и посыплются заказы. Уже в этом году, по всей видимости, мы заключим от трех до пяти договоров на поставку этих машин».
Первые машины будут поставлены на предприятия самого «Росатома». В целом спрос со стороны структур госкорпорации Владимир Береговский оценивает примерно в 150 машин.
Пройти развилку
Наша основная задача — часть денег, которые уходят на Запад, оставить здесь, в России. Мы все время говорим государству: «Помогайте таким, как мы». При этом мы не просим у государства денег, а лишь хотим работать на нашем же рынке в условиях честной конкуренции.
Из разговора в компании «Топ-системы»
Отработка технологии. Теперь это главная задача для производителей аддитивных машин и их пользователей — промышленных предприятий. Хорошая западная машина может стоить миллион евро. А вот технология производства конечных деталей с определенными свойствами — в пять раз дороже. Мощность лазера, температура, среда, система охлаждения, состав и размер порошка — все имеет значение. Почему в России должно быть иначе?
Дело не в количестве произведенных 3D-принтеров, хотя и это важно. Дело в том, что они могут сделать. Получится ли с их помощью «вырастить» изделия, превосходящие по своим свойствам те, что сделаны по традиционным технологиям, да при этом еще быстрее и дешевле?
Без науки тут не обойтись.
«Я разговаривал с одним моим хорошим товарищем из университета, — рассказывает Дмитрий Сапрыкин. — Я говорю: “Давай сделаем что-то вместе, какой-нибудь проект для промышленного производства. Помоги нам с научной точки зрения”. А он отвечает: “Понимаешь, вот у меня есть рейтинг в Scopus и в Web of Science. За то, что я с тобой что-то сделаю, я получу один балл, а не сто, как за публикацию в американском журнале”. То есть научным работникам, которых оценивают по месту в этих рейтингах и по публикациям (KPI, модное слово), мы не нужны. Только в последние год-два ситуация начала сдвигаться и стало налаживаться взаимодействие университетов и заводов». Ключевые слова — «стало налаживаться взаимодействие». Хотя рейтинги по-прежнему в цене.
Отчасти ситуация изменилась и потому, что раньше у науки не было возможности отрабатывать технологии на отечественном оборудовании — все серьезные машины были импортными. А далеко не все они поставлялись с открытой программной платформой, позволяющей широко экспериментировать. Появление российских машин закрывает этот пробел.
Впрочем, не только машин. Параллельно с созданием реальной аддитивной машины в структурах «Росатома» создается так называемый виртуальный принтер: «С его помощью можно воспроизвести технологию изготовления изделия, созданного в конструкторской компьютерной программе. Виртуально произведя его. И тут же при помощи другой мощной компьютерной программы, “Логос” (аналог западной ANSYS), спрогнозировать, какие свойства будут у этого изделия. То есть вживую его печатать сразу не надо. Потом, конечно, нужно будет и напечатать, провести верификацию всей технологии. По мере накопления базы данных в конечном итоге мы можем для основной части продукции вообще отказаться каждый раз проверять свойства готового изделия», — прогнозирует Алексей Дуб, первый заместитель генерального директора АО «Наука и инновации» (входит в «Росатом»).
В пакете программ «виртуального принтера» будет и программа, позволяющая провести топологическую оптимизацию изделия. Владимир Береговский предполагает, что появление такого продукта будет способствовать более активному распространению аддитивного производства: «Когда у конструкторов появится такой инструмент, я думаю, что и дело с приобретением машин пойдет гораздо веселее, потому что они увидят, насколько можно сократить, во-первых, трудоемкость изготовления деталей, во-вторых — металлоемкость».
Как показывает практика, взявшись за разработку аддитивной машины, производитель пишет и программу, под которой работает сам принтер. Это вселяет надежду, что в итоге вся программная цепочка — от CAD-систем до программ топологического дизайна — может быть российского происхождения и мы избежим ситуации, которая сложилась сегодня с современными импортными станками.
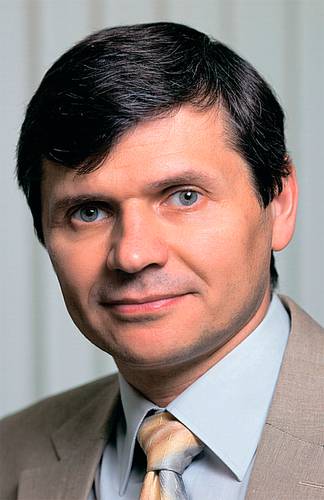
«Ситуация простая: сейчас все серьезные станки стоят на оборонных предприятиях, — сетует Сергей Козлов, директор по разработке ЗАО “Топ Системы”. — И проблема для нас состоит в том, что основную роль в той области, в которой мы работаем, — в конструкторских системах моделирования — играют крупные иностранные компании, Siemens, к примеру. И это лобби, которое сформировалось за последние годы, — серьезная проблема. Мы много говорим об импортозамещении в станках, а мы должны говорить об импортозамещении в IT, в процессе проектирования и подготовки производства в машиностроении. Мы зависим от софта глобальных иностранных компаний на ключевых производствах почти полностью, процентов на девяносто. У них фактически монополия. От конструкторских систем до программ управления станками. Фактически российские предприятия просто финансируют западных разработчиков высокотехнологичного ПО».
«Топ Системы» — один из ведущих российских разработчиков систем автоматизации проектирования, в их главном продукте T-FLEX CAD есть все необходимые средства проектирования и подготовки данных как для аддитивных технологий, так и для традиционных производственных процессов.
Здесь подчеркивают, что российские специалисты уже создают все необходимое программное обеспечение. Нужно лишь дать им возможность работать с российскими предприятиями, перестав опираться на иностранные решения: «У нас софт в десять раз дешевле: у них рабочее место миллион стоит, а у нас сто тысяч. А девяносто процентов задач мы решаем не хуже, а многие даже лучше. Мы за последний год в Германии продали нашу систему более чем на тысячу двести немецких предприятий».
В общем, посыл понятен: российскому «железу» — российский софт.
Не тяните лису за хвост
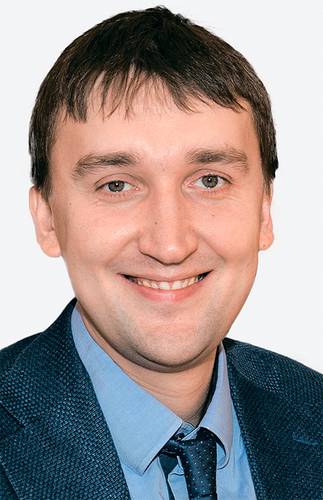
Когда мы два года назад начали этой тематикой заниматься активно, рынок фактически был мертвый. Просто мертвый.
Дмитрий Мартынов, управляющий директор АО «Полема»
И российский же порошок.
Важным условием для более широкого распространения аддитивного производства в России участники рынка и эксперты считают развитие собственного производства порошковых композиций. Отечественные порошки априори дешевле иностранных, а снижение цен на них делает аддитивные технологии более привлекательными для предприятий с точки зрения экономической эффективности.
Алексей Мазалов, управляющий директор АО «Центр аддитивных технологий» (Воронеж), отмечает снижение цен на порошки по мере появления на рынке новых производителей. Эта компания обладает крупнейшим в стране набором промышленного оборудования в области аддитивных технологий, в том числе работающего с металлическими порошками. Изначально приобретались импортные системы с открытой программной платформой, что позволило экспериментировать и постепенно переходить с использования поставляемых вместе с 3D-принтерами металлических импортных порошков на отечественные.
Один из партнеров Центра аддитивных технологий — Промышленный металлургический холдинг в лице тульского завода порошковой металлургии «Полема». История завода насчитывает более полувека, однако к выпуску порошков для использования в аддитивном производстве предприятие приступило не так давно: полтора года назад там разработали технологии получения металлических порошков. Этот проект получил финансирование от Фонда развития промышленности в виде займа в размере 270 млн рублей. Общая его стоимость — 449,8 млн рублей. Предполагается, что осенью новое производство уже будет запущено. Объем производства металлических порошков для аддитивных и MIM-технологий составит до 100 тонн в год.
«Это позволит нам перекрыть весь импорт по сплавам с железной, никелевой и кобальтовой основами», — утверждает управляющий директор АО «Полема» Дмитрий Мартынов. После запуска этого производства предприятие намерено начать процесс сертификации своих порошков у производителей аддитивных машин.
По словам Дмитрия Мартынова, у компании есть два потенциальных клиента, совокупная потребность которых в металлических порошках для аддитивного производства составляет 55 тонн в год. В связи с этим г-н Мартынов не исключает, что объемы запускаемого производства окажутся меньше потенциального спроса. Секрет успеха Дмитрий Мартынов видит в индивидуальном подходе: «Мы рассчитываем с каждым клиентом рентабельность перевода производства на аддитивные технологии. Обговариваем, какая химия, какие объемы ему нужны, какие дополнительные обработки он делает. Мы можем сделать, например, сложнолегированный какой-то сплав, который сразу даст нужные физические и механические свойства, но он будет дорогой. Мы можем сделать сплав проще и дешевле и порекомендовать клиенту, например, добавить в производственную цепочку термообработку напечатанного изделия. Тогда это будет для него дешевле, но это опять зависит от объема, сколько он хочет сделать. Я бы сказал, что сейчас рынок сдерживает то, что нет этого индивидуального подхода. Все пытаются работать по шаблону, а шаблона здесь нет. Рынок молодой, и нужно рассчитывать экономику под каждое изделие».
А поскольку рынок молодой, то у потенциальных потребителей существует определенная эйфория, вызванная недостатком информации о технологии: «Сейчас происходит осознание полной технологической цепочки. Я сравниваю аддитивные технологии с лисой. Производители порошков — хвост лисы. Конечная мехобработка — ее зубы. Все сейчас сосредоточились на заднице лисы: думают, как печатать. А на самом деле свойства изделия закладываются не на печати. Свойства закладываются в послепечатной доводке изделия: термообработка, гомогенизирующий отжиг, дополнительная интенсификация в горячем изостатическом прессе. Там получаются хорошие свойства. То есть помимо покупки принтера и порошка нужно еще покупать оборудование для термообработки напечатанного изделия».
Этим, кстати говоря, «Полема» тоже планирует заниматься — компания намерена создать собственный центр 3D-печати: «Клиенты покупают у нас порошок и начинают бегать по всей стране и искать, где его напечатать. Чтоб удовлетворить эту потребность, мы бы хотели этот сервис у себя сделать. Причем сделать уже полностью — с термообработкой и с нормальными технологическими режимами. Планируем для этого купить две машины лазерные и две — электронно-лучевые. Что касается того, импортные это будут машины или российские, то кто предложит наилучшие условия, в том числе с точки зрения технологии, у того и возьмем. Мы берем то оборудование, которое эффективно».
Не исключено, что это будет выигрышная стратегия. Сегодня мировое производство металлических порошков разных типов для аддитивного производства исчисляется сотнями тонн. В России — тоннами. И это при том, что, по словам директора по новым проектам ОК «Русал» Алексея Арнаутова, объем мировых мощностей по производству металлических порошков всех видов существенно превышает миллион тонн. Так что конкуренция ожидается не слабая. В «Русале», кстати, утверждают, что к этой конкуренции они готовы.
Ухаживать и поливать
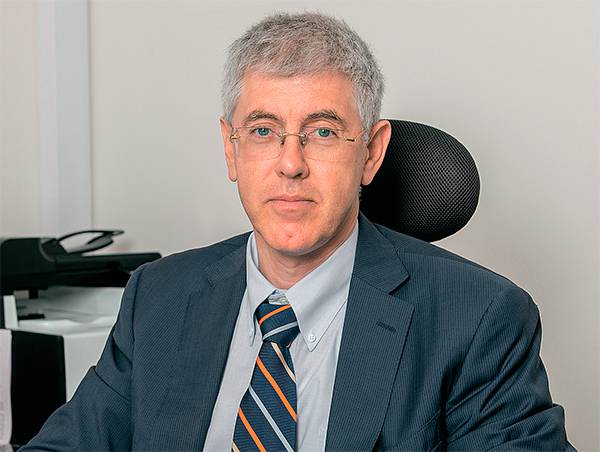
Мы не имеем самого главного — конструкторов, которые способны проектировать уже в новой реальности. Их нет потому, что не создана нормативная база, которая обеспечивает мостик от старой технологии к новой.
Алексей Дуб, первый заместитель генерального директора АО «Наука и инновации» («Росатом»)
Всё у нас есть. Что же тормозит внедрение аддитивных технологий в реальное производство? Бюрократия. Куда же без нее. Инерция мышления. Недостаток информации. Страх нового. Деньги. Ну и так далее. Впрочем, все это преодолимо.
Без бумажки и технология не технология: «Как это ни странно, современные технологии в мире преимущественно связаны с нормативными документами, которые эти технологии имплементируют в современную жизнь», — отмечает Алексей Дуб. Нет документа — значит, конструктор не может опираться на эту технологию в своей работе. А производство начинается с конструктора. Так что разработка нормативной базы — одна из важнейших задач. Технический комитет по стандартизации «Аддитивные технологии» создан в 2015 году на базе ВИАМа. АО «Наука и инновации» активно участвует в разработке стандартов. Пока их разработано только десять. На голом, как говорят, энтузиазме.
«Не скрою, что это требует средств. Вариантов два: либо государство должно выступить инвестором, который даст деньги на разработку этих стандартов, либо нужно ждать, что наши предприятия, поняв, что им необходимо ускоряться с точки зрения вывода на рынок новых продуктов, захотят профинансировать создание этих стандартов», — рассуждает Алексей Дуб. По его словам, в год надо разрабатывать по десять-пятнадцать стандартов.
Впрочем, как справедливо замечает Михаил Иванов, некоторые виды аддитивных технологий могут использоваться и без обязательной сертификации: «Сегодня уделяется большое внимание разработке отечественных принтеров для производства литейной оснастки. Это не требует дополнительной сертификации, так как технологический процесс и материалы отливок не меняются. При этом сокращается себестоимость всего технологического процесса. Германия использует около 3500 единиц принтеров для подобного вида литья, США — более 5000 единиц, в России в связи со слабой осведомленностью о современных технологиях используется всего 30 импортных установок для стереолитографии и 15 — для работы с песочными формами под “литье в землю”».
Действительно, пока в апробировании новой технологии наиболее активны предприятия из высокотехнологичных отраслей: ОПК, авиастроение, космос, двигателестроение, атомная энергетика. И, судя по всему, с них и начнется массовое внедрение этих технологий в реальное производство. Сейчас они нащупывают места приложения этих самых технологий, объединяют усилия по их продвижению, налаживают обмен информацией. При этом со стороны видится, что кооперация участников происходит без давления сверху, по горизонтали. И главное, все они заинтересованы не только во внедрении аддитивных технологий в свое производство, но и в том, чтобы это самое аддитивное производство базировалось на российских машинах и технологиях.
«Если вы используете чужое оборудование, чужие технологии, то вся информация о том, что вы делаете с их помощью, как вы делаете, какой результат получаете, отправляется в базу данных производителя оборудования и владельца технологии, — объясняет Алексей Дуб. — Так что, как только мы покупаем импортный принтер, импортные материалы и начинаем на нем что-то делать, мы тут же всю информацию о том, что мы делаем — не конкретно какое изделие, а какие у него свойства, например, — тут же передаем в их базу данных и в этом смысле их обогащаем. Поскольку эта информация — большая ценность для крупных компаний, так как на ее основе они и верифицируют свою продукцию».
Вряд ли производители подводных лодок и эсминцев, самолетов и вертолетов, атомных станций и авиационных двигателей захотят делиться информацией с конкурентами. И вряд ли они захотят отстать от конкурентов, отказавшись от внедрения аддитивных технологий.
А значит, выход только один — самим выращивать новое для российской экономики производство по аддитивным технологиям и все сопутствующие ему продукты и сервисы: машины, порошки, программное обеспечение, исследовательские лаборатории и далее по списку. Возможности для этого есть.