Производительность труда в России даже в самых успешных компаниях ниже, чем на Западе, а в среднем ниже в 10–15 раз. Зачастую проблему производительности пытаются решить за счет покупки нового оборудования. Однако опыт компаний, которые умеют наращивать производительность, показывает, что огромные залежи неэффективности находятся на стороне организационных процессов бизнеса. О подходах к увеличению производительности машиностроительных предприятий мы поговорили с генеральным конструктором инженерно-консалтинговой компании СОЛВЕР Радиславом Бирбраером.
— Мы недавно решили посмотреть разрыв в производительности труда между нашими госкомпаниями и зарубежными аналогами. Зарубежные аналоги, естественно, могут быть как государственные, так и негосударственные. Обнаружили, что разрыв составляет от десяти до двадцати раз. То есть он просто колоссальный. Очевидно, что есть три причины такого разрыва: технологический разрыв, то есть у нас плохие технологии, управленческий — плохо налажены бизнес-процессы и структурный — неэффективная структура выпуска, она могла такой сложиться и меняться слишком медленно. Это так?
— Я отчасти чувствую себя экспертом только в вопросах производительности в машиностроении. Об этом и буду говорить. В машиностроении основное — это технологии производства. Лидерство в технологии — это во многом лидерство экономик.
— В чем сегодня разрыв между нашими технологиями и западными?
— Разрыв — в возможности использования всего технического потенциала, который в принципе заложен в современном оборудовании. Мы говорим: «Нам нужна вот такая технология, она соответствует современному уровню». Что значит «соответствует современному уровню»? Это значит, что с использованием этой технологии мы получаем высокое качество, которое воспринимает рынок, сжатые сроки производства и конкурентную цену. Мы долгое время считали, что все двери в мире открыты, и не очень занимались промышленными технологиями. А теперь, когда мир изменился, введены различного рода санкции, мы понимаем, что нужно развивать собственные технологии, но догнать непросто, хотя последние несколько лет ускорение очень заметно.
Второе — это тема организации производства. У нас очень любят бережливое производство. Но что такое бережливое производство? Когда Toyota кратно повысила производительность труда везде, где смогла: выгребла издержки сначала «экскаватором», потом «лопатами» и стала бороться за единичные проценты производительности, — вот тогда они придумали бережливое производство. То есть это совочек, которым можно что-то подчистить. А нам в России показалось, что этим совочком мы можем сделать работу «экскаватора». В наших производствах залежи проблем, которые нужно пластами выковыривать и менять старые организационные принципы на новые.
— Я разговаривала с президентом «Технониколя» и спросила: «Что делать с самого начала, если вы хотите повысить производительность?» Он сказал, что надо для начала понять коэффициент загрузки оборудования (ОЕЕ). Как правило, он очень низок, а менеджмент этого не осознает. Насколько это важно?
— Это очень важно, потому что на большинстве предприятий, причем не только государственных, но и частных, нет реального понимания, почему оборудование, которое должно, как говорится, снимать стружку, находится в состоянии простоя. И конечно, сначала надо разобраться с коэффициентом загрузки.
Например, когда стоит задача роста выпуска количества продукции, то в первую очередь можно решить эту задачу существующими ресурсами, оборудованием и персоналом, и, нарастив выпуск продукции, получив дополнительные объемы продаж, получить реальный рост производительности труда. Но на практике у многих наших предприятий, как только есть перспектива роста спроса на продукцию, тут же рассматриваются проекты, связанные с приобретением нового оборудования. А это и рост численности, и инвестиции серьезные — а производительность фактически не увеличивается.
Повременная оплата против сдельной
— А какой аргумент в пользу новых инвестиций?
— У нас все загружено. Поэтому, конечно, нужно получить объективную информацию, как реально загружено работой существующее оборудование, а за последние пятнадцать лет предприятия приобрели достаточно много нового оборудования.
В чем причина недоиспользования ресурсов оборудования? Наиболее важная — устаревшая форма оплаты труда. Весь мир где-то в конце восьмидесятых годов перешел на повременную оплату труда, отказавшись от сдельной. Одной из последних, кстати, была компания IBM. А у нас до сих пор в основном используется именно сдельная оплата труда, которая была введена еще в советское время.
— Но она же справедлива?
— Кажется, да: что сам себе заработал, то и скушал, — но, не отказавшись от нее, нам очень трудно будет повысить производительность труда. Сдельная оплата удобна менеджменту. Для того чтобы сделать повременную оплату труда, нужно, например, правильно планировать, и за это должен отвечать менеджер, а не рабочий. А если я не умею правильно планировать производство, не умею вовремя выполнять заказ, то, чтобы скрыть это неумение, легче всего использовать сдельную оплату труда, делегируя ответственность вниз. И это делегирование сверху вниз упирается в рабочего. Вот ты, парень, бери и зарабатывай свою зарплату. Ты отвечаешь теперь и за себя, и за экономику нашего предприятия. Как он ее зарабатывает? Каждая деталь, которую он делает, оценивается нормо-часами. Сделал детали — заработал за месяц 180 нормо-часов. А нормо-час стоит, например, двести рублей. И ты можешь просто посчитать, сколько заработал конкретно — 36 тысяч рублей. Нормо-часы — это фактически часы, которые директивно разрешено затратить на выполнение операций по изготовлению деталей. Будет он заинтересован в том, чтобы уменьшить эти нормо-часы, выполняя определенную технологическую операцию? Нет. Наоборот, он сделает все для того, чтобы время, которое «привязано» к этой детали, было не меньше, а лучше, если будет больше.
— Проблема-то извне кажется небольшой. Есть повременная оплата, есть сдельная. Вы приходите к начальнику, говорите: «Повременная лучше. Переходи на повременную». Он вам верит и переходит.
— Никто добровольно не переходит. Когда производство не справляется со штуками, которые нужно выпустить, директору начинают рисовать эти нормо-часы. Ему говорят: «Мы не можем выполнить эти штуки за это время». — «Как не можем?» — Начинают нормо-часы соизмерять с ресурсом работы оборудования. И выясняется, что оборудования не хватает. «Что нужно?» — «Пять станков еще купить». — «Хорошо, купим пять станков, еще пять или десять рабочих наберем». Вот и потеряли производительность.
Переход на повременную оплату — это опора на достоверное планирование. Тогда менеджер должен четко сказать рабочему: за восемь часов ты должен сделать столько-то деталей. Но тогда и ответственность за то, что ему правильное количество штук предписали, лежит на менеджере. Начальник цеха, мастер в цехе должны проконтролировать выполнение этих штук. То есть тогда ответственность уже поднимается выше. Рабочий может восемь часов и простоять, правильно? Но его должны обеспечить работой. То есть такая смена системы оплаты труда вынужденно приведет к нужным переменам в управлении производством. Потребует внедрения современных систем управления экономикой предприятия.
Мы попытались на одном очень серьезном предприятии внедрить метод теории ограничений автора книги «Цель» Элиаху Голдратта. Это когда ты явно управляешь производственным потоками и весь поток ориентируется только на своевременное исполнение заказа. И когда на этом предприятии в течение двух месяцев так поработали, обнаружили, что есть продукция, которая делается, но привязана к заказам, которые вообще уже никому не нужны, идет на склад длительного хранения.
— Да ладно!
— Директор завода мне сказал: «Если вы внедрите систему, мы вам памятник поставим». Но мы не смогли. На самом деле это очень интересно, как работает логика в сдельной оплате. Есть рабочий, которому нужно заработать нормо-часы, и он их себе зарабатывает. Мастер тоже понимает, что если рабочий нормо-часы не выработает, то не получит зарплату. Мастер начинает придумывать работу, иногда загружает его работой, которая может быть совершенно не связана с оперативными заказами, — пусть поработает на склад. А что такое продукция, которая никому не нужна? Ее продать невозможно. Вот и потеря фактической производительности в этих непроданных запасах. А перейти на повременную оплату — значит действительно работать в каком-то понятном рыночном механизме. Есть подтвержденный заказ, нужно спланировать его исполнение, сделать его вовремя, для этого нужно ровно столько-то ресурсов, не больше и не меньше. И платить нужно за то, что будет продано на финише производственного потока.
— Но в чем проблема? Вы же сказали, что машиностроение в основном работает на государство. Более или менее понятен размер заказа, его план, ну и так далее. Это же не рынок хаотичный. Тогда в чем проблема, работая на госзаказ, перейти на повременную оплату труда?
— Как только мы перейдем на повременную оплату, выяснится, что деталь можно делать не десять часов, а три часа. Соответственно, их можно выпускать не ста рабочими, а тридцатью.
— Прекрасно.
— Но мы не можем допустить социального взрыва. И при сдельной оплате труда можно всегда обосновать, почему такие режимы обработки и нужно так много нормо-часов. А когда ты говоришь: «Это нормо-время не соответствует реальному времени», — тебе отвечают: «Ну ты же понимаешь, нам нужна обоснованная зарплата».
— Но мир же не зря сначала имел сдельную оплату труда, и только потом они догадались, что надо перейти на повременную. Это явно было связано с изменением в системе управления.
— Конечно. В первую очередь мы сейчас говорим о цифровизации, о цифровой экономике.
— Восьмидесятые годы?
— Да, как только появились вычислительные системы планирования и контроля за производством, пришли к выводу, что повременная оплата стала более эффективной. Уже тогда можно было рассчитать исполнение производственных заказов при минимальных затратах времени и ресурсов. Рассчитать — ключевое слово.
Я вернусь к истории с заводом. Когда выяснилось, что куча продукции делается на склад и не востребована, привлеченные консультанты от Голдратта сказали: «Мы выходим из проекта до тех пор, пока у вас мотивация не будет поддерживать современные методы управления». Запад перешел к повременной оплате тогда, когда они поняли, что можно рассчитать, предписать и проконтролировать производство, увязав с ним мотивацию труда. А сейчас колоссальной революции в управлении производством нет, просто вычислительные ресурсы стали более мощными, появились суперкомпьютеры в центрах обработки данных и мобильные устройства на рабочих местах.
— Как устроены информационные системы управления производством?
— Системы управления нашими предприятиями в большинстве своем затрагивают управление финансами и персоналом, а реализованных проектов по управлению производством не очень много. Сегодня активно развиваются отечественные, особенно на основе ERP «Галактика».
— Почему важно управление производством в системах управления предприятием?
— Потому что мы должны опуститься до уровня каждого рабочего места и достоверно спланировать работу там. Экономика растет именно оттуда.
Новые закупки нужны всегда
— Мы когда-нибудь изменим наше машиностроение?
— Изменим только тогда, когда ответственно скажем себе, что мы готовы поднять производительность, наступив на очень болезненную тему сокращения персонала. Что такое коэффициент загрузки для станка? Станок, который «включен в розетку» две смены, должен работать шестнадцать часов. А реально он работает на выпуск продукции, например, восемь часов. Будет работать шестнадцать часов и даст продукции в два раза больше при том же количестве персонала, но не стоящего возле станка, а работающего на нем.
— То есть пятьдесят процентов — это более или менее распространенная загрузка? Почему?
— Потому что большую часть станочного парка мы по технологии подтянули, и эти станки с ЧПУ обмануть достаточно трудно. То есть за время, за которое снимается стружка, теперь отвечает компьютер станка. Как можно растянуть время на изготовление детали? За счет того, что, когда машина остановилась, оператор должен что-то долго крутить, налаживать… Эти системы переналадки — такой черный ящик, который позволяет нормо-часы очень сильно увеличить.
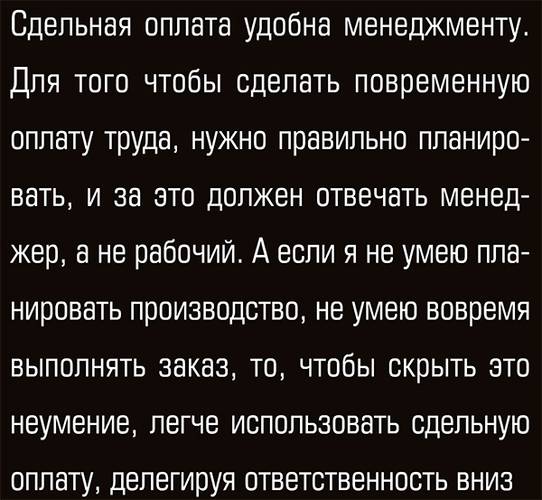
— Но это же абсурд.
— Опять могу случай из жизни рассказать. На одном серьезном предприятии проводили ревизию одного из проектов техперевооружения. Надо было понять, нужны большие средства на закупку нового оборудования или нет. Провели анализ и выяснили, что по подготовленному проекту текущая загрузка существующих станков — восемьдесят процентов, поэтому для роста программы производства обязательно нужны (как считали специалисты завода) значительные инвестиции в новое оборудование. Мы предложили: «Давайте попробуем на том, что есть сейчас, поднять пропускную способность». — «Да невозможно! Ну пробуйте…» Взяли участок из девяти станков. «Сколько вы деталей в месяц сейчас планируете на этот участок?» Получили план. Мы прикинули и говорим: «Этот участок будет делать в три раза больше». — «Да ладно!» — Выяснилось, что вместо того, чтобы заниматься переналадкой два часа, ею можно заниматься несколько десятков минут, изготовив специальные приспособления. Изготовили и предложили: «Давайте только договоримся так, что результатом нашей работы будет не абстрактная цифра роста производительности, а мы поставим наших специалистов к станкам и они сделают сменно-суточное задание с обещанным бо́льшим количеством деталей. И сделали. Начальник цеха нашим сказал: «Ребята, вы что? Сейчас бунт будет у рабочих. Они, — говорит, — сейчас ко мне прибегут и скажут, что они сделали деталей больше, дай мне зарплату больше».
— Ну и что? Они же и деталей сделали в два раза больше.
— Он должен поднять зарплату нескольким рабочим, а остальных тогда нужно уволить, так как в них больше нет необходимости при более интенсивной работе.
— Нет, подождите. Ведь руководитель спрашивал, надо инвестировать или не надо. Вы объяснили, что надо, но не в таком масштабе, как планировалось. Но тогда разницу можно заплатить рабочим.
— Насколько мне известно, какую-то часть предложенной нами технологии они применили. Хотя, конечно, если бы сократили часть рабочих, а оставшимся подняли бы зарплату хотя бы на двадцать процентов, уже был бы толк.
— Ваш диагноз: этого никогда не произойдет. Мы начали с того, что у нас есть разрыв в качестве технологий и нам надо догонять. Но если мы будем догонять с мыслью, что нам обязательно надо потратить, чтобы загрузить рабочих, или купить оборудование, или еще что-то, то ничего не произойдет. Мы оказываемся в некотором тупике.
— Надо двигаться вперед, конечно. «Цифра» позволяет контролировать работу не раз в квартал и на диспетчерских совещаниях разбираться: «Я взял отчет, оказывается, у меня там станок целый месяц простаивал». Теперь эту информацию можно снимать каждый день. Как только мы сможем реально использовать результат этого контроля для правильного планирования, правильной мотивации персонала и перехода на повременную оплату труда, у нас все получится.
— А что происходит в рыночном сегменте машиностроения? И с точки зрения наличия -отсутствия заказов на нашу продукцию? Или мы совсем вне рынка?
— Мы сейчас общаемся с Петербургским тракторным заводом. Выпускает знаменитые мощные энергонасыщенные трактора «Кировец». И, как выяснилось, они буквально за несколько лет подняли свою долю внутреннего рынка с четырнадцати до семидесяти процентов.
— Там все в порядке с эффективностью? Повременная оплата труда?
— Конечно, не только это, но и система мотивации там абсолютно рыночная.
— И сбыт есть, и все работает?
— Мы с директором говорили. Он мне рассказывал историю. Как он в начале своей работы на этом заводе собрал экономистов и задал вопрос: «Смотрите, ребята, такая деловая игра. К вам пришел заказчик и готов купить трактор за сто рублей. У вас реально девяносто рублей стоят материалы, десять рублей — это реальная зарплата. А себестоимость трактора по вашим «котловым» расчетам — сто двадцать рублей. Вы будете продавать трактор?» Они говорят: «Нет, конечно, у нас же себестоимость сто двадцать, а заказчик готов платить только сто». Он говорит: «Понял. То есть, если заказчик заплатит вам сто, вы на девяносто купите материалы, а десять рублей останется, чтобы вам платить зарплату, но вы отказались, десять рублей не заработали, да? И вы не продали, потому что у вас мысленно потери двадцать рублей. Тогда заказчик ушел, а вы реально зарплату десять рублей все равно платите, потому что людей вы не сократили. Только вы платите из собственного кармана, а не из его ста рублей».
— И что он сделал?
— Он разобрался с себестоимостью и системой продаж. Ввел правильную мотивацию на производстве.
— За сколько лет это произошло?
— За три года они это сделали.
— То есть рынок открыт фактически?
— Да. Для меня это один из ярких примеров, когда я увидел, как работает правильная экономика. Я не думаю, что везде, где хозяином является государство, невозможно это сделать. Возможно.
Управление простоями
— Сергей Колесников из «Технониколя» как раз и говорил, почему ОЕЕ первый. Потому что не надо начинать покупать оборудование, пока еще не знаешь, что у тебя творится.
— Казалось бы, когда вы это формулируете, выглядит банально. Упрощенно ОЕЕ — это и есть степень загрузки оборудования. Другой вопрос, что у тебя нет инструмента, с помощью которого ты можешь такую «температуру» измерить объективно. Сейчас инструменты такие появились. Цифра, онлайн. Сейчас мы можем замерить не только то, сколько станок работает, но и причины его остановок.
— Причины меряете тоже электронно?
— Мы создали специальную систему цифрового мониторинга НАВИМАН. Если станок остановился, это фиксируется. И оператор указывает в меню одну из причин остановки, которые мы предварительно адаптируем под конкретные условия производства («Нет инструмента», «Нет заготовки» и так далее). Потом эти причины анализируем и, например, делаем вывод: «У вас станок не обрабатывал деталь, потому что прогрев шпинделя происходит недопустимо долго. Вы купили современный станок, ему двадцати минут прогрева достаточно». Так устраняются организационные причины простоев. Заносятся в специальную матрицу потерь. Потом туда оцифрованные виды потерь вносятся, и вносятся мероприятия, которые нужны для того, чтобы эти потери снизить или убрать вовсе. Так уходят организационные потери. Дальше потери мигрируют в так называемую желтую зону: станок остановлен, потому что идет переналадка.
— И дальше что происходит?
— Мы придумали штуку, которую назвали навигацией. Выбираем эксперта-оператора, надеваем ему очки, в которые встроена камера. И всю работу, которую он делает, он снимает. После этого с помощью специального программного обеспечения этот видеоряд разбивается на отдельные шаги. Шаги загружаются в библиотеку системы. И когда в следующий раз рабочий делает то же самое, к нему инструкция приходит не в виде фильма, а в виде дискретных шагов с конкретным временем. И предписывается: как только ты этот шаг завершил, ты должен нажать кнопку «Выполнено». Во-первых, есть уверенность, что он выполнит все шаги. А во-вторых, по теории ограничений мы следим за так называемым буфером опозданий. На каждом шаге у него есть информация, насколько он опаздывает к точке финиша процесса обработки. Если статус красный, он значительно опаздывает, зеленый — все делает вовремя.
У нас такая история была. Смена кулачков по нормативам была двадцать пять минут. Кулачки — это приспособления, которые зажимают деталь. Нужно одни кулачки убрать, другие поставить. Надеваем очки — пять минут. Взял, поставил, все. И так по каждому шагу. Ясно, что часто переналадка вместо трех часов превращается в час или полчаса. В совокупности со снижением организационных потерь добиваемся роста загрузки оборудования на двадцать-тридцать процентов при той же численности персонала. Вот вам и рост производительности!
Есть еще один интересный момент в машиностроении. На госпредприятиях примерно пятьдесят процентов парка — это универсальное старое оборудование. Низкая производительность труда. Мы сделали такое предложение: «У вас есть современное оборудование. Мы можем поднять его загрузку на двадцать-тридцать процентов. И если нет роста объема заказа, то давайте уберем обработку с универсального оборудования и перенесем ее на обеспеченный дополнительный ресурс существующего высокопроизводительного оборудования. Уберем как класс старое, изношенное оборудование. Отправим на заслуженный отдых людей, которые рядом с ним стоят. Можно это сделать? Можно и нужно.
— По поводу роботизации что вы думаете? Насколько широко она востребована?
— Я, когда готовился к интервью, параллельно отвечал на запрос одной государственной структуры, которая занимается вопросами производительности. Я им написал: первое — это технологии, второе — организация, контроль, правильное планирование ресурсов, загрузки ресурсов. Третье — автоматизация, роботизация. Есть особенности производства, которые не всегда удобны для роботизации. Но это перспективное направление развития производства. Однако нужно понимать, что роботизация в большей степени возможна, когда это достаточно крупносерийное производство. Когда много переналадок, это проблематично.
— Но тотально невозможна роботизация? Есть опасения, что человек перестанет быть носителем знаний.
— Тотальная роботизация возможна тогда, когда есть удобные для нее производственные задачи. Я думаю, что они во многом пока носят ограниченный характер. Но как альтернатива, наблюдая за действиями человека, мы через цифровые инструкции можем «роботизировать» действия человека. Цифровизация позволяет нам управлять более жестко действиями человека. В то же время это в определенном смысле база знаний, которую можно накапливать и совершенствовать.