Мы сами это сделали. Своими собственными руками. И то, что мы сделали, это, наверное, самое плохое из того, что мы могли сделать для нашей промышленности. Мы уничтожили отечественное станкостроение. Практически полностью. Объемы производства металлообрабатывающих станков в 2010 году относительно 1990 года рухнули в двадцать пять раз, а доля российских производителей на внутреннем рынке опустилась ниже десяти процентов. Установка начала 1990-х «продадим нефть и купим то, что нам надо, на зарубежных рынках» лишила отрасль будущего.
Резкое снижение объемов производства в обрабатывающей промышленности свело до нуля потребность в покупке новых станков. И даже начавшийся в 2000-е экономический рост не сильно повлиял на спрос: расти от низкой базы можно было и на старом станочном парке. Если же возникала необходимость его обновить, предприятия предпочитали покупать иностранные станки.
Так что для производителей станков черная полоса оказалась значительно шире, чем для многих других отраслей. Одно время даже было впечатление, что они двигаются не поперек этой черной полосы в надежде когда-нибудь достичь белой, а вдоль — к полному разрушению отрасли и выходу России из клуба стран, имеющих собственную станкоинструментальную промышленность. Таких, кстати, в мире чуть больше трех десятков.
В общем, спроса не было, персонал разбегался, заводы останавливались. Пустые цеха переоборудовались под склады или торговые и офисные центры, если «повезло» с расположением, как, например, Липецкому станкостроительному, чей главный корпус теперь стал торгово-развлекательным центром «Европа». Или станкостроительному заводу имени Серго Орджоникидзе в Москве — одному из первых в СССР.
Не в своем отечестве
Тем, кто еще оставался на плаву, было выгоднее и проще работать с зарубежными потребителями. Доля экспорта у российских производителей стабильно высока, а по некоторым позициям даже превышает поставки на внутренний рынок. Виной тому высокая ставка кредита в России. Производство станка может занимать несколько месяцев. Российские покупатели не готовы работать по предоплате, а взятый станкостроителем по высокой ставке кредит съедает всю его маржу.
А иностранный производитель, взявший кредит в банке под полтора-два процента годовых, вполне может сделать станок и продать его российскому покупателю. Причем часто продать в рассрочку. Например, под пять процентов, что для российского рынка вполне приемлемо, и в результате не только «отбить» кредит, взятый на производство станка, но и немного заработать на разнице в стоимости денег.
В обратную сторону схема несколько иная: иностранный покупатель получает дешевый кредит в банке своей страны (а часто еще и субсидию по линии своего правительства) и делает предоплату российскому производителю, который, получив деньги, спокойно производит станок и передает его покупателю. Так что российский рынок довольно быстро заняли иностранные производители. Имея за плечами многолетний опыт работы в рыночных условиях, они на раз «сделали» своих российских конкурентов.
«Любой стратег понимает, что заходить в страну надо на минимуме делового цикла, когда все дешево. У нас иностранцы в кризис очень активизировались. Проводили семинары, тренинги, массово вывозили российских специалистов за границу, — говорит Сергей Недорослев, президент станкостроительной компании “Стан”, — Это называлось “съездить на завод, посмотреть, как они производят станки”. Что давало это “посмотреть”? С профессиональной точки зрения — ничего. Понятно, что производят они их хорошо. Главным здесь было завязывание личных отношений. Причем компании совершенно правильно действовали, они не договаривались, например, с главным технологом — он человек большой, по заводам не ездит. Они били на перспективных, молодых. Платили хорошие командировочные. Это что — коммерческий подкуп? Нет. Это правильный маркетинговый инструмент. Когда спад сменится подъемом, эти люди станут взрослыми, займут высокие должности, будут принимать решения. Так и случилось».
По мнению Сергея Недорослева, важное конкурентное преимущество иностранные производители станков получили и в процессе формирования в России рынка инжиниринговых услуг. Наиболее крупные компании в этой сфере имеют тесные связи с иностранными станкостроителями еще с начала 1990-х и своим клиентам предлагают именно оборудование своих иностранных партнеров, в том числе потому, что получают от них хорошие комиссионные.
«Мы пытались договориться, — делится Сергей Недорослев, — предложить комиссионные инжиниринговым компаниям. Говорим им: мы зарабатываем восемь процентов, готовы отдать половину — четыре процента. Нас даже не дослушали. Потому что, оказывается, они получают от иностранных производителей 15 процентов. А мы не можем 16 процентов банкирам отдавать и 15 — им. Мы тогда просто обанкротимся».
С Сергеем Недорослевым солидарен и генеральный директор ЗАО «Липецкое станкостроительное предприятие» Владимир Петров: «Современное производство — это не станок, а технология. У кого технология менее затратна либо позволяет выпускать более качественные товары, тот и выигрывает конкурентную борьбу. Поэтому на первый план выходят инжиниринговые компании. Безусловно, связь инжиниринговых компаний с иностранными производителями более плотная, чем с российскими. Во-первых, мы только начинаем смотреть в сторону инжиниринга, а зарубежные компании уже давно на этом выстроили свой бизнес. Во-вторых, система ценообразования иностранных компаний построена так, что в стандартную цену закладывается 25–40 процентов комиссионных, мы же формируем прайс-лист, основываясь на 20–25 процентах прибыли. При такой системе ценообразования, конечно же, нельзя давать скидку более 10–12 процентов, иначе это будет работа ради работы. Получается, что это проигрышная политика ценообразования и надо ее пересматривать, тогда инжиниринговые компании повернутся лицом к российским производителям».
Кстати говоря, российские власти озаботились развитием инжиниринговых услуг в стране не так давно: в 2014 году в рамках программы развития промышленности была принята подпрограмма об инжиниринговой деятельности и промышленном дизайне на срок до 2018 года. При этом финансирование из бюджета предполагалось только в течение первых трех лет в размере трех миллиардов рублей.
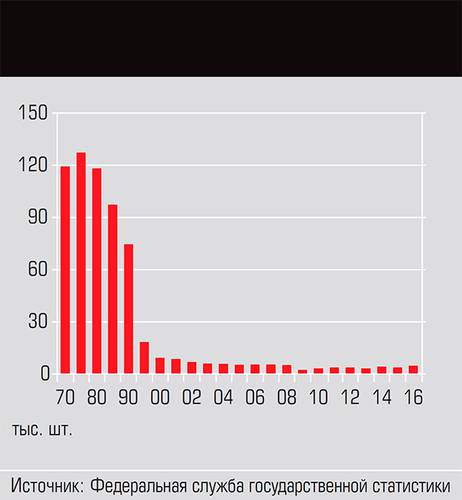
Перевооружение для вооружения
Шанс на возрождение станкоинструментальная промышленность получила после того, как в России началось перевооружение армии. Оно потребовало обновления станочного парка на оборонных заводах. К этому моменту основными игроками рынка металлообрабатывающего оборудования были отечественные станкопроизводители, прямые наследники еще советских заводов, и крупные дилеры, которые продавали на нашем рынке продукцию иностранных производителей. При этом, как уже было сказано, российские заводы проиграли маркетинговую битву, и потому сама по себе необходимость покупки новых металлообрабатывающих станков российской оборонкой не могла оказать практически никакого влияния на процесс восстановления отрасли. Предприятия могли спокойно — до санкций, введения которых в 2011 году никто и не предполагал, — закупать необходимое у иностранных компаний металлообрабатывающее оборудование, качество и производительность которого, надо признать, зачастую было значительно лучше предлагаемого оставшимися на плаву российскими заводами.
Так что следующим шагом стало введение протекционистских мер, призванных дать российским станкостроителям преимущество на собственном рынке.
Это был вполне логичный ход, считает Владимир Петров: «Меры поддержки есть во всех странах, которые занимают ведущие роли в машиностроении. При этом все эти страны состоят в ВТО. Поэтому все меры поддержки машиностроительной отрасли, которые есть в этих странах, скрыты и завуалированы. То есть машиностроение и тем более станкостроение в современном мире не может развиваться без поддержки государства».
Одной из таких мер поддержки стало принятое в феврале 2011 года постановление правительства РФ № 56, которое запрещало оборонным предприятиям закупать импортные станки в том случае, если их аналоги производятся в России (в дальнейшем это постановление с небольшими изменениями принималось каждый год под новыми номерами).
Одним из главных инициаторов и лоббистов появления этого документа была отраслевая ассоциация «Станкоинструмент». Ее президент Георгий Самодуров вошел в комиссию Минпромторга, которая определяет, производится ли то или иное оборудование на территории России, и фактически дает предприятию разрешение купить иностранный станок в случае отсутствия российского аналога. По его словам, если первое время только в семи-восьми случаях из ста комиссия выдавала заключение, что заявленное предприятиями оборонки к приобретению оборудование производится в России, то сейчас до 35% таких заявок закрывается российскими аналогами.
Однако дорога к этому результату была непростой. Предприятия ОПК продолжали покупать импортное оборудование, мотивируя это так: да, предприятие мы государственное, но покупаем-то на свои, заработанные, то есть не на бюджетные. Объяснение, почему это не так, со стороны власти последовало довольно быстро. Затем схема чуть усложнилась: иностранные станки ввозились в страну в разобранном виде, здесь комплектовались, на них крепился шильдик с надписью «Сделано в России» — и фактически иностранный станок под видом российского уходил на предприятие. Эту лазейку постепенно тоже прикрыли, определив уровень локализации, при котором станок может получить статус российского.
Сегодня комиссия ежемесячно рассматривает от 250 до 400 заявок на покупку станков от предприятий оборонно-промышленного комплекса. «Это колоссальный результат, — считает Георгий Самодуров. — И надо сказать, что в последние три-четыре года мы видим рост потребления станочного оборудования со стороны предприятий энергетического машиностроения, транспортного машиностроения, нефтедобывающего комплекса».
Произошли изменения и в структуре закупок оборудования предприятиями. «Если в начале, когда только вышло постановление, — подчеркивает Георгий Самодуров, — предприятия ОПК заказывали для технического перевооружения своих предприятий в 50–55 процентах случаев универсальное оборудование, а на оборудование с числовым программным управлением (ЧПУ) и обрабатывающие центры приходилось максимум 25 процентов заявок, то сейчас картина такая: 70–75 процентов заказов предприятий оборонки — оборудование с ЧПУ и обрабатывающие центры».
Но, наверное, самое главное, что произошло с российским станкостроением после 2011 года, это его структурное преобразование. Во-первых, борьба за заказ со стороны оборонки, обремененная условиями со стороны правительства, привела к тому, что иностранные производители начали строить на территории России станкостроительные заводы. Самый популярный пример здесь — завод DMG Mori, запущенный в Ульяновске в 2015 году. «Когда мы десять лет назад предлагали иностранным компаниям: приходите и стройте здесь заводы, — они смеялись и неофициально говорили: мол, зачем мы будем это делать, если рынок открыт, можно поставлять свое оборудование, загружать свои заводы, давать работу своим рабочим, — рассказывает Георгий Самодуров, — Постановление, выпущенное в 2011 году, заставило их изменить свою позицию».
Во-вторых, появились совместные предприятия российских станкостроителей с иностранными. Таких предприятий уже около десятка.
И наконец, возникли новые станкостроительные компании, созданные при участии частных инвесторов, собирающих в единый холдинг разрозненные активы, в том числе остатки предприятий, которые работали еще в СССР. К ним относится уже упомянутая компания «Стан».
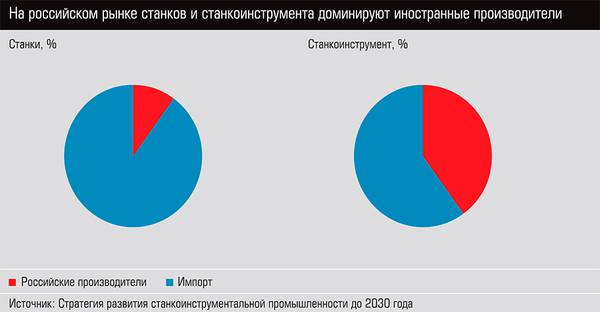
Конкуренция с подвохом
Несмотря на рост числа отечественных компаний, потребители по-прежнему предпочитают покупать зарубежную продукцию.
«Мы развили свои мощности по производству станков, вложили деньги в модернизацию. Мы конкурентоспособны. И не только “Стан”, многие заводы, — рассказывает Сергей Недорослев. — Но реализоваться эта мощность не может. Потому что на совещаниях на высоком уровне директора говорят, что будут в первую очередь рассматривать российские станки, а покупают в итоге иностранные».
По словам Недорослева, сегодня российские производители металлообрабатывающего оборудования могут «закрыть» своими поставками порядка 40% всех выставленных заявок на конкурсах по поставкам станков. Но в реальности поставляют только от пяти до семи процентов. Учитывая важность выполнения оборонного заказа, обосновать покупку конкретного иностранного оборудования не так уж и сложно: «Никто не оперирует тем, что “старый друг лучше новых двух” или что “от добра добра не ищут”, — делится с “Экспертом” своим видением ситуации Сергей Недорослев. — Генеральному директору, который в большинстве случаев не технарь, а управленец, и который опирается на мнение специалистов, просто говорят: “С этими станками мы изделие получим, а с этими — нет”. И все. Да, министр промышленности просил покупать отечественное, председатель правительства говорил про развитие станкостроения… Но за изделие директор отвечает перед президентом. Выбор предсказуем».
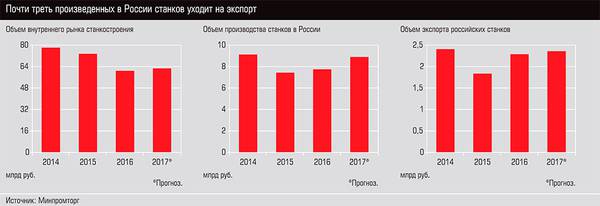
Так что способы обхода постановления правительства, запрещающего покупать иностранные станки при наличии российских аналогов хотя и усложняются, но продолжают применяться.
«Раньше предприятия обходили постановление “в лоб”, — продолжает Сергей Недорослев. — Это означает следующее: мы ничего не скрываем, наши каталоги открыты, они берут каталог, читают, видят, что у нас станок 12 тысяч оборотов выдает, и говорят своим партнерам: сделайте 16 тысяч. На самом деле для обработки стали не надо столько, и мы можем сделать такой станок. Но мы не делаем, потому что не знаем, что будет именно такой заказ. Объявляется тендер на поставку, и там условие: 16 тысяч оборотов. Выигрывает иностранная компания. Мы написали письмо в Министерство промышленности, пожаловались. Это попало к министру, я сам слышал, как на совещаниях Мантуров говорил: “Вы там прекратите!” Прекратили. Но теперь иначе обходят. Для чего нужен станок? Чтобы сделать определенную деталь. Заводу нужна деталь. Для ее производства может понадобиться несколько станков. Иностранный партнер предлагает группу станков для изготовления какой-то конкретной детали. Среди этих станков есть те, которые мы не делаем. И мы проигрываем. Но дело в том, что мы можем сделать эту же деталь на других станках, которые мы производим. Однако нам говорят: “В постановлении про деталь ничего не сказано, в постановлении сказано, что нельзя ввозить аналоги, у вас таких станков нет”. То есть теперь можно считать, что постановление больше не работает, потому что всегда можно найти станки, которые не являются аналогами, но могут выпускать эту деталь».
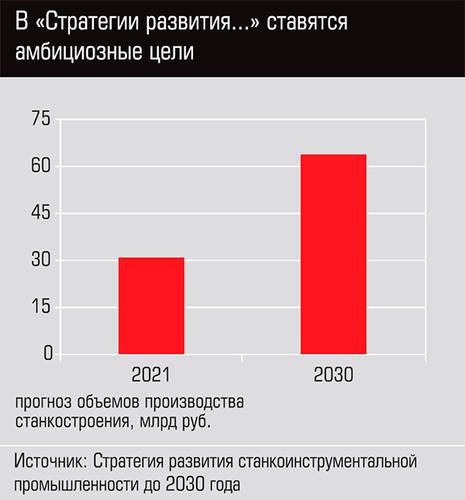
Специалисты Южного завода тяжелого станкостроения (создан на базе завода им. Г. М. Седина, Краснодар) также отмечают дискриминацию российских производителей: «Вся система государственных закупок заточена под импортный рынок. Технические задания делаются под их продукцию, выставляется короткий срок изготовления станков, а главное, первоначальные платежи со стороны предприятий с госучастием минимальны или полностью отсутствуют».
Приверженность иностранным станкам объясняется и тем, что еще живы воспоминания промышленников, как заказанные российским производителям станки или поставлялись с существенной задержкой, или не поставлялись вовсе.
«У нашей компании был опыт приобретения отечественных станков, — рассказал “Эксперту” Владимир Боглаев, генеральный директор ОАО “Череповецкий литейно-механический завод”. — Сотрудничали с производителем несколько лет. Качество продукции и цены нас устраивали, но поставки партнер всегда задерживал на большой срок, что очень влияло на финансовые показатели проекта. К тому же потом стоимость станков выросла, и они стали неконкурентоспособны по сравнению с предложением зарубежных компаний».
Маркетинговый провал российских станкостроителей тоже дает о себе знать: «На нашем производстве используются в основном японские станки Mazak, они обеспечивают высокое качество конечного изделия. К сожалению, у компании нет опыта эксплуатации современных отечественных станков, потому что очень мало информации по поводу их наличия на рынке, — отмечает Светлана Линник, директор компании “Пегас-Агро”. — Сегодня мы используем лишь небольшое количество токарных станков еще советского производства, которые были дополнительно оснащены импортным числовым программным управлением».
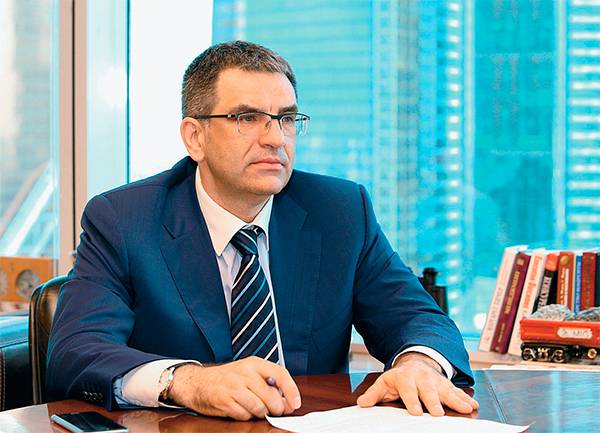
В то же время станкостроители в неформальных беседах отмечают еще одно, если так можно выразиться, конкурентное преимущество иностранного оборудования. Российский станок в процессе поставки проходит довольно короткую цепочку: производитель — инжиниринговая компания (если она участвует в сделке) — конечный потребитель. Если в ее начале станок стоит, условно, двадцать миллионов, а в конце — двадцать пять, то участвующая в сделке инжиниринговая компания покажет на эти пять миллионов свои услуги, заплатит налоги — и на этом все закончится. Если же она продаст тот же станок уже за 40 миллионов, то со стороны налоговой последуют вопрос: а нет ли здесь незаконного обогащения? В случае, если покупатель станка — оборонное предприятие или предприятие с госучастием, возникнет интерес к сделке у правоохранительных органов: а нет ли здесь хищения бюджетных средств? Поскольку информацию о всех сделках на территории России правоохранители могут довольно быстро получить, такого рода схемы вскрываются без особых усилий, и желающих их выстраивать становится все меньше.
Другое дело, когда станок поставляется из-за границы. Какой-то офшор может купить его у производителя за условный миллион долларов, а потом продать инжиниринговой компании за два миллиона. Она ввезет его в Россию, накинет свой небольшой, в разумных рамках, процент и передаст конечному покупателю. В этой ситуации сбор информации правоохранительными органами закончится на запросе в этот самый офшор, чей ответ на вопрос о цене станка будет предсказуем: коммерческая тайна.
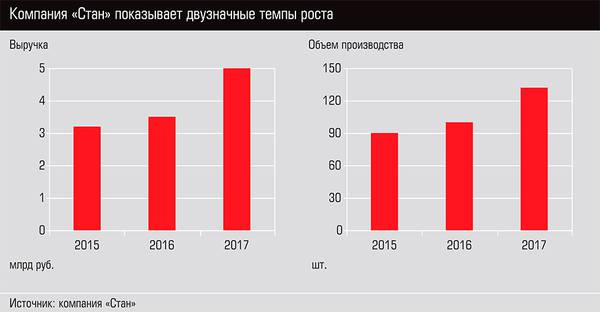
В бассейне должна быть вода
В мае 2016 года председатель правительства РФ Дмитрий Медведев поручил профильным министерствам разработать стратегию развития станкоинструментальной промышленности до 2030 года. Предполагалось, что документ будет утвержден до конца 2017-го. Однако теперь определен новый срок — первый квартал 2018 года. В отрасли считают, что документ крайне сырой, не учитывает реального положения дел в станкоинструментальной промышленности, предлагаемые меры поддержки порой сложны для применения на практике, а в том, что касается финансирования, недостаточны. Например, в самой стратегии сказано, что общее финансирование отрасли в России за 2014–2015 годы составило в среднем полтора миллиарда рублей в год. При этом в Китае только поддержка от введения льгот по НДС в 2015 году оценивается в 50 млрд рублей, а в Японии вклад государственных структур в НИОКР в станкостроении составляет от 25 млрд рублей ежегодно.
В дальнейшем финансирование российского станкостроения существенно не увеличится: стратегия предполагает, что «суммарный объем инвестиционных вложений на развитие НИОКР и наращивания производственных мощностей как за счет бюджетных, так и внебюджетных средств за 2017–2030 годы оценивается в 65,3 млрд рублей». Основным источником инвестиций должен стать Фонд развития промышленности, на его долю придется 48% общих вложений. Бюджетные субсидии составят 30%, собственные средства предприятий 12%, заемные — 10%.
При этом цели в стратегии поставлены весьма амбициозные — например, довести долю российских производителей на внутреннем рынке до 50%, обеспечить рост российского производства со средними темпами не менее 15% в год.
«Ранее, до прошлого года, работал ряд постановлений правительства, которые способствовали субсидированию процентных ставок по кредитам для предприятий, которые привлекали финансовые ресурсы как для пополнения своих оборотных средств, на выпуск продукции, так и на техническое перевооружение. Это был хороший механизм, который, к сожалению, сегодня практически не действует, — говорит Георгий Самодуров. — Поэтому мы выступаем за возвращение механизма субсидирования ставки. Еще один источник, который на протяжении четырех-пяти лет активно работал, а сейчас эти программы практически свернуты — это бюджетные субсидии на проведение НИОКР».
Как известно, правительство несколько лет поддерживает сельскохозяйственное машиностроение, выдавая аграриям субсидии на покупку отечественной техники. Эта мера позволила отрасли показывать двузначные темпы роста на протяжении нескольких лет. Недавно подобное решение было принято и в отношении производителей специальной техники. Для подъема станкостроения, считает Константин Бабкин, президент ассоциации «Росспецмаш», подобная мера тоже могла бы стать весьма эффективной. «Еще один вариант поддержки — возвращение инвестиционной льготы по налогу на прибыль для предприятий, которые проводят модернизацию, — продолжает Константин Бабкин. — Размеры льготы могли бы быть различными: для тех, кто закупает импортные станки и оборудование, ее можно было бы сделать меньше, а для тех, кто покупает отечественное, — больше».
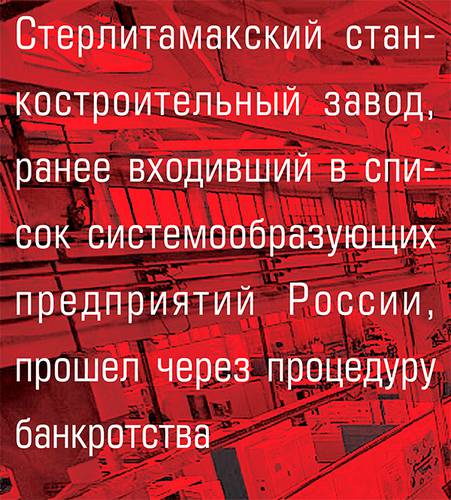
Учитывая современную политическую ситуацию и нарастающее санкционное давление, которое оказывается на Россию в экономической и научно-технологической сфере, промедление с принятием мер по стимулированию развития станкостроительной отрасли чревато серьезными последствиями.
Как рассказывают участники рынка, одному из крупных российских оборонных холдингов было отказано в поставке станков с предприятия, построенного на территории России иностранной компанией. Причина — прямой запрет правительства страны, откуда родом эта самая иностранная компания. Возмущенные оборонщики написали письмо в правительство, мол, как так: компания станки производит в России, на них выдан соответствующий сертификат, подтверждающий, что они российские, и мы — российская компания — не можем купить российский же станок!
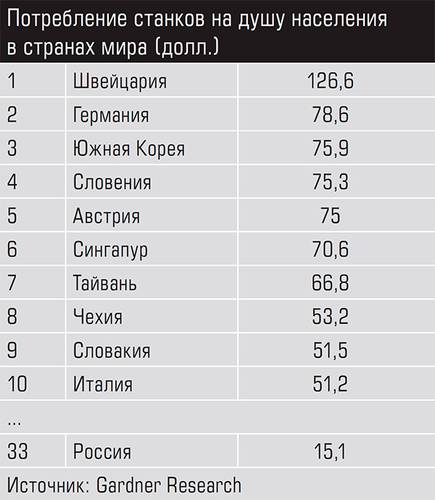
Избежать подобных ситуаций можно лишь развивая собственное станкостроение, чтобы иметь собственные компетенции на всех этапах производства станков. Начиная, конечно же, с конструирования. При этом, по мнению Георгия Самодурова, важно обеспечить трансфер технологий от уже работающих на территории страны иностранных станкостроительных компаний: «Я все время говорю собственникам DMG Mori, что мы поверим в серьезность ваших намерений после того, как увидим, что вы в России создаете мощнейшую проектную организацию, которая именно здесь будет разрабатывать самые современные станки».
«Перетаскиванием» современных технологий должны заниматься и российские компании, работающие в партнерстве с иностранными. «Мы убедили наших партнеров, что необходимо заниматься трансфером технологий, — рассказывает Дмитрий Каледин, директор по продажам ЗАО “Балтийская промышленная компания” (выпускает металлообрабатывающие станки под торговой маркой FORT). — У нас подписано соглашение с нашими партнерами из Тайваня, Южной Кореи, Австралии, по которому мы получаем эти технологии в виде конструкторской технологической документации, берем ее за основу, и на этой базе разрабатываем собственный модельный ряд станков».
В компании «Стан», по словам Сергея Недорослева, работает 450 конструкторов: «Станкостроители должны концентрироваться на разработке станков. Мы сейчас делаем центр компетенции, отдельно от конструкторского бюро. Там самые умные будут нарабатывать решения, которые КБ потом будет прорисовывать и внедрять».
Собственно, все российские станкостроители в унисон говорят о важности именно переноса в Россию или создания на ее территории конструкторских центров, что позволит развивать инженерный потенциал по проектированию. Квалификация конструктора и квалификация сборщика — это две не соприкасающиеся квалификации, подчеркивают они: «Когда нам говорят: вы, мол, потренируйтесь, пособирайте, а потом мы вам в бассейн воду нальем, — это ложь. Когда рынок насытится, спрос пойдет на убыль, никакого смысла создавать здесь конструкторские бюро не будет».
Пока же сборочные производства — безусловные победители в конкурентной борьбе.
«Если ситуация не изменится, нам придется подстроиться под условия рынка. Завтра возьмем даже не немецкие, а корейские чертежи, выгоним всех конструкторов, технологов и оставим 120 сборщиков. И зарабатывать будем не восемь процентов, а все сорок, — говорит Сергей Недорослев. — Но мы так не делаем. Этому тоже есть объяснение: в любой момент нам смогут отказать в чертежах, и мы останемся ни с чем — и без станков, и без компетенций. Если ты сам занимаешься проектированием, то ты надолго на этом рынке, ты видишь будущее. Наши конструкторы знают, что через пять лет будет станком. А те, кто собирает чужие станки, знают, что было станком пять лет назад».
Впрочем, даже сконструированный в России станок нужно еще и произвести. А в случае ужесточения санкций с этим могут возникнуть проблемы — не все компоненты производятся в России. Некоторые критически важные узлы и детали приходится покупать у признанных мировых лидеров — например, системы числового программного управления. Или шпиндели и прецизионные подшипники для них. Надо сказать, что по всем этим направлениям ведется работа, цель которой — импортозамещение критически важных позиций. Например, современную отечественную систему ЧПУ разрабатывает сразу несколько коллективов. И эти системы уже демонстрируются на выставках. Но мало разработать систему ЧПУ, ее еще нужно и произвести, причем серийно. Кто будет это делать, пока неизвестно. Есть мысль «назначить» производителем какой-то оборонный завод, имеющий свободные мощности и необходимые компетенции, но, чтобы эти системы были конкурентоспособными, их надо производить массово. Много систем ЧПУ — много станков. Но российских станков пока мало.
Балтийская промышленная компания и германская Hugo Reckerth GmbH создали совместное предприятие по производству шпинделей. «В мире станкостроения считается, что если ты делаешь станину, основу станка (а мы ее делаем) и шпиндель, сердце станка, то ты можешь считать себя настоящим станкостроителем», — утверждает Дмитрий Каледин. Производство шпинделей запускает и компания «Стан».
В свою очередь, выпуск импортозамещающих высокоточных и малошумных подшипников, которые используются в станкостроении, осенью прошлого года начался на Вологодском заводе специальных подшипников. Проект реализован при помощи Фонда развития промышленности, который выдал предприятию заем в размере 500 млн рублей. Еще 960 млн под поручительство Корпорации МСП предоставил банк ВТБ. Общая стоимость создания этого производства — 2,7 млрд рублей.
Пока это скорее единичные проекты. Станкостроение есть производство средств производства. Без него не будет промышленности. Но и без промышленности нет станкостроения — кто-то же должен выплавить металл для станины, сделать подшипник для шпинделя и процессор для системы ЧПУ. Встречное движение есть, но пока вклад станкостроения в ВВП страны составляет только 0,02%, что на порядок меньше, чем в КНР (0,2%) — Китай начал развивать свое станкостроение примерно в то же время, когда наше полетело в пропасть, из которой теперь пытается выбраться.