В декабре 2017 года Выксунский металлургический завод (ВМЗ), входящий в состав Объединенной металлургической компании (ОМК), по итогам аудита, проведенного японской компанией Toyota Engineering Corporation (ТЕС; входит в группу Toyota), получила серебряную медаль ТЕС за успехи в развитии производственной системы.
«По нашей оценке, уровень зрелости производственной системы Выксунского металлургического завода превышает аналогичный показатель не только японских металлургических предприятий, но и всей мировой металлургической отрасли. Это первое предприятие в металлургии, которое достигло таких впечатляющих результатов», — заявил президент ТЕС Тосихиро Ямада.
Ранее, в 2016 году, ВМЗ стал первым в мире металлургическим предприятием, удостоенным бронзовой медали ТЕС. На тот момент это было лучшим в мире показателем для металлургии и в принципе доказало возможность тиражирования производственной системы Toyota за пределы машиностроительной отрасли, в частности на предприятия металлургического сектора.
А в январе 2018-го другое предприятие группы ОМК — Альметьевский трубный завод — по итогам аудита ТЕС получил оценку уровня зрелости производственной системы, соответствующую бронзовой медали. И стал, таким образом, вторым в мире металлургическим предприятием, удостоенным этой награды.
ОМК — один из крупнейших производителей металлических труб в России и мире (см. график 1).
За что же японцы награждали металлургов?
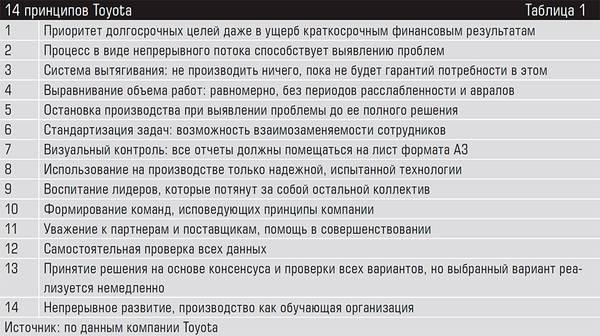
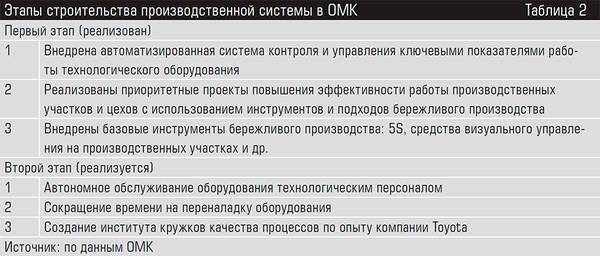
Всеобщая производственная система
Речь идет о внедрении всеобщей производственной системы Toyota —Total Toyota Production System (T-TPS).
Производственная система разрабатывалась японской машиностроительной компанией Toyota с конца 1940-х годов, когда после тяжелого поражения во Второй мировой войне Япония лежала в руинах, испытывая жесточайший дефицит решительно во всем — от финансовых средств до сырья и технологий.
С 1948 года основатель и глава Toyota Киитиро Тоёда начал внедрять на производстве принцип «точно в срок». Это наиболее известный принцип, который сейчас чаще всего и ассоциируется с Toyota, — в противовес ранее господствовавшему принципу фордизма, предполагавшему, напротив, максимальную опору на собственные силы. Одновременно компания постоянно работала над повышением качества, осваивала быструю переналадку оборудования (Single-Minute Exchange of Dies; SMED).
В результате уже в 1949 году Toyota отказалась от промежуточных складов, а в 1958-м — от изоляторов брака. В чем суть этих нововведений? Раньше любую ошибку можно было прикрыть за счет складских запасов, хотя это и означало перерасход материалов и человеко-часов. Теперь скрыть ошибки становилось невозможно. В результате снижались потери и росло качество продукции.
С 1980-х производственная система Toyota преобразуется во всеобщую производственную систему T-TPS. Важным нововведением в ней стал принцип активизации персонала и производственных участков через стимулирование инициативы снизу.
«Производственная система Toyota в своей основе — это организация оптимального потока материалов и информации, — говорит старший консультант Toyota Engineering Corporation Тацуми Кимура. — В идеале это поток единичных изделий, который нигде не останавливается. Но потом мы понимаем, что за этим стоят еще другие факторы — “М”. Это материалы (materials), обслуживание оборудования (machines), активизация и вовлечение персонала (men), совершенствование способов выполнения этой работы (methods). Есть прежняя модель TPS — производственная система Toyota. Сейчас мы называем нашу модель T-TPS — всеобщая производственная система Toyota, которая делает акцент на всех четырех “М”. Организационная структура компании — рабочий, линейный руководитель, менеджеры среднего уровня и, соответственно, руководство, топ-менеджмент компании. Если руководство сильное, это может дать определенный результат. Но пока вы не создадите для линейного персонала, для линейных руководителей возможности для движения снизу вверх — возможности подавать свои предложения, инициативы по улучшениям, — устойчивого развития компании не будет. Вот это движение снизу вверх очень важно».
Мировую известность производственная система Toyota получила благодаря американскому исследователю Джеффри Лайкеру, посвятившему японскому гиганту ряд книг, из которых самая известная, пожалуй, «Дао Toyota: 14 принципов менеджмента ведущей компании мира» (2003), где изложены основные особенности, легшие в основу управления производственной системой Toyota (см. таблицу 1).
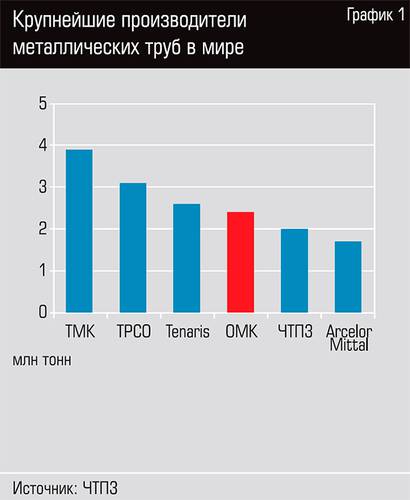
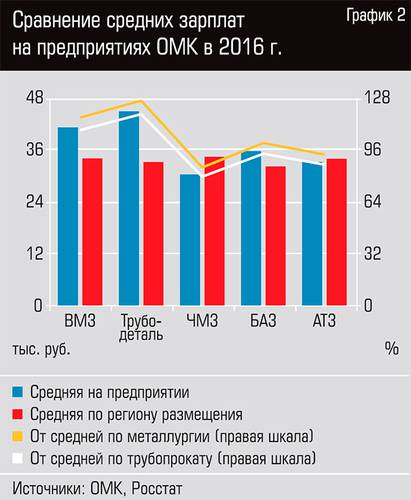
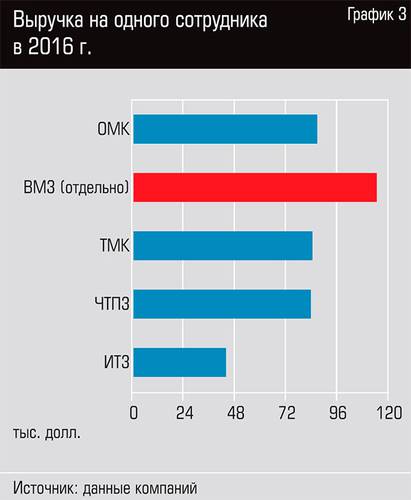
От машин к металлургии
ОМК начала выстраивать свою производственную систему с 2011 года. Пилотным объектом стала главная производственная площадка компании — ВМЗ. Были поставлены четкие цели: активизация темпов роста и снижение потерь. До этого у завода уже был опыт внедрения передовых управленческих технологий. В 2002–2003 годах была реализована программа оптимизации производства, в 2010-м — программа повышения культуры безопасности труда. А в 2011 году с помощью сторонних консультантов в ОМК разработали концепцию развития производственной системы.
Начальник управления по развитию производственной системы ОМК Владимир Смирнов рассказывает: «В 2011 году ОМК было принято решение о старте производственной системы на Выксунском металлургическом заводе. На первом этапе был проведен отбор сотрудников, которые должны были начать преобразование изнутри. Из нескольких тысяч работников отобрали десять наиболее компетентных “навигаторов” изменений. Было проведено необходимое обучение, определены базовые инструменты бережливого производства для внедрения, начались преобразования. В этой работе помогли консультанты.
На следующем этапе, в 2012 году, началось внедрение производственной системы на челябинском заводе “Трубодеталь”. Одного года хватило, чтобы собрать там команду “навигаторов” и получить первые положительные результаты. Параллельно началось развитие Чусовского металлургического завода и Альметьевского трубного завода. После вхождения в состав ОМК Благовещенского арматурного завода также начались работы по развитию производственной системы».
Японские аудиторы впервые появились на заводах ОМК в 2015 году. Как утверждают в компании, сделано это было с целью проверить, насколько проделанная своими силами работа соответствует «иконе стиля». Считалось, что лучшей в построении производственной системы и основоположником собственно производственных систем, инструментов бережливого производства является именно Toyota.
По итогам аудита в ОМК приняли решение доработать свою производственную систему. Были определены основные направления развития: ежедневное управление и контроль, визуализация процессов, 5S-производство и 5S-офис (это назвали единым инструментом), культура производства, следование корпоративному курсу, который включает в себя цели, задачи, видение бизнеса, стратегию бизнеса; это также стандарты рабочих мест, технологические стандарты, стандарты безопасности производства, стандарты качества.
Если рассмотреть некоторые из этих аспектов детальнее, то 5S — это стандартная японская система организации и рационализации рабочего места, один из инструментов бережливого производства. Система включает в себя такие понятия, как сортировка (разделение вещей на нужные и ненужные), соблюдение порядка (организация хранения необходимых вещей, которая позволяет быстро и просто их находить и использовать), содержание рабочего места в чистоте, стандартизация, совершенствование (воспитание привычки точного выполнения установленных правил, процедур и технологических операций). В некотором смысле эта система перекликается с идеями советского теоретика научной организации труда Алексея Гастева.
В ОМК признают, что полностью применить наработки Toyota для металлургии не представляется возможным.
«У нас есть еще такой фактор, как партийность, — рассказывают в компании. — Предприятие металлургического комплекса, которое производит для нас металл, может изготовить определенную минимальную партию. И даже если нам нужна лишь половина этой партии, мы будем вынуждены купить всё, потому что они по-другому не работают. И мы планируем свое производство с учетом двух факторов: возможностей поставщика и потребностей потребителя. Поэтому “точно в срок” не получается, небольшой запас все равно у нас будет храниться».
С другой стороны, Тацуми Кимура не считает, что внедрение всеобщей производственной системы Toyota в металлургии потребовало какой-то ее адаптации: «Не имеет значения, какая отрасль. Во всеобщей производственной системе Toyota главное — создание производства людей, которые могут самостоятельно заниматься улучшением. Я был руководителем металлургического завода, который работает в группе компаний Toyota, он раньше назывался Toyota Steel. Это тоже металлургическая компания, и я понимаю, что это можно и нужно использовать в работе. У нас все началось с кружков качества — линейный персонал собирался, выбирал тему сам, находил проблему, искал первопричину, разрабатывал мероприятия, реализовывал их. Потом началось внедрение внутренней системы всеобщего управления качеством. Потом нас начали обучать производственной системе Toyota. Это, конечно, тяжело шло. Тем более что в металлургии многое нельзя подогнать под поток единичных изделий. И потом, всеобщая производственная система в основе имеет всемерное развитие персонала, линейных руководителей. Это все вполне реализуемо, я в своей компании этим занимался и видел успехи».
Итак, важнейшими факторами производственной системы на сегодняшнем уровне видятся вовлеченность всего персонала в развитие компании, личная заинтересованность и инициатива снизу.
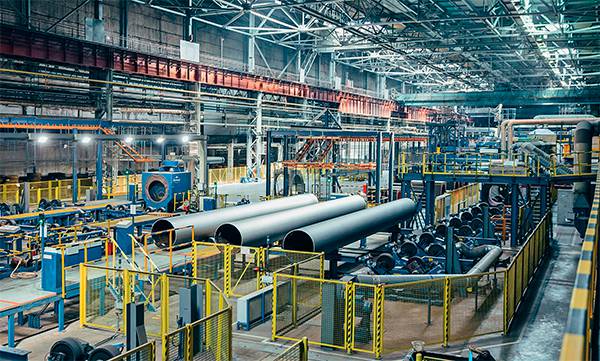
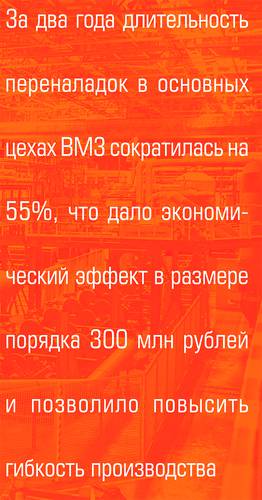
Научить инициативе
«Объединяющим фактором всей работы в рамках производственной системы является развитие и забота о людях компании, — говорит Владимир Смирнов. — Без сотрудников, которые работают на производстве и являются основной ценностью для ОМК, сделать ничего нельзя. Здесь одним из важных факторов было, есть и остается постоянное обучение. В компании существуют действующие программы обучения сотрудников, в том числе по развитию производственной системы. Мы обучаем людей как инструментам развития производственной системы, так и методам их применения с выходом на действующее производство. Для этого реализуются пилотные проекты, осуществляется мини-трансформация процессов. Новый человек в компании обязательно должен пройти вводный курс обучения. На предприятиях ОМК новые сотрудники проходят через учебный центр, где им рассказывают об инструментах производственной системы в Академии производственной системы. При обучении инструментам производственной системы работникам рассказывают обо всем, что требуется от человека с точки зрения применения инструментов бережливого производства на его рабочем месте. Далее новый сотрудник сдает тесты в автоматизированной системе обучения и получает отметку, сдал или не сдал, и только после успешного прохождения тестирования допускается к выполнению работы.
Еще один важный момент в поддержании и развитии инструментов производственной системы ОМК — принцип постоянного совершенствования. Для этого на всех предприятиях ОМК созданы и работают кружки качества процессов и ведется активная рационализаторская деятельность, которая поддерживается и поощряется руководством компании. Проводятся конкурсы на лучшее рабочее место, на лучшее рационализаторское предложение, на лучший кружок качества процессов. Победители и призеры получают ценные призы и признание от высшего руководства».
В ОМК есть нескольких инструментов развития рационализаторского движения.
Работник любого уровня имеет возможность подать рацпредложение, которое несет экономически обоснованный эффект, вносит какое-то изменение, какую-то новизну в работу.
Есть формат А3. Формат А3 направлен на улучшение того процесса, который уже существует. То есть человек, работая определенное время на каком-то станке, видит, что процесс несовершенен, но знает, как его изменить. В компании для этого есть специальный бланк. Работник его заполняет, обсуждает с мастером, с руководителем. Создается комиссия, и она передает это все дальше вверх.
И есть экспресс-улучшения. Под ними в ОМК понимают улучшения, которые не требуют сколько-нибудь существенных материальных затрат и могут реализоваться практически автоматически.
ОМК также развивает две формы самоорганизации сотрудников.
Во-первых, это так называемые малые инициативные группы. Они пришли из Японии и фактически являются аналогом японских «кружков качества». В рамках малой инициативной группы несколько рабочих под управлением мастера или бригадира собираются в определенное время и решают какие-то проблемы, связанные с технологией. Они вырабатывают решение. Есть специальные бланки, которые члены группы заполняют. И далее это решение поступает на рассмотрение к руководителю. После этого, если получено положительное заключение, оно направляется на исполнение. А потом люди получают вознаграждение, например, денежные выплаты.
К концу 2017 года на ВМЗ насчитывалось более 310 малых инициативных групп, в работе которых участвовало более 1900 сотрудников. Всего в малых инициативных группах реализовано около 900 проектов, свыше 300 находится в работе.
Во-вторых, можно отметить так называемые малые рабочие группы. Принцип в основу положен тот же самый, но здесь руководит уже начальник цеха либо сам директор предприятия. На этом уровне решаются проблемы более масштабные, связанные с реорганизацией производства, со значительным изменением технологии.
Инициатива снизу поощряется даже на уровне стандартов производства. Сначала разработкой стандартов занимались «навигаторы» — сотрудники отдела по развитию производственной системы. Затем, когда какой-либо процесс обкатывается, он регламентируется и передается в производство. Далее в производстве уже непосредственно рабочие, технологи и руководители рабочих, мастер или бригадир, самостоятельно создают стандарты, утверждают их с техническими службами и размещают в общекорпоративных информационных системах. В ОМК есть даже графики смены стандартов.
При этом развитие тех или иных инструментов производственной системы может приводить как к росту производительности работника, так и к ее снижению — но за счет роста качества.
Как же в таких условиях стимулировать работников к инициативе и собственному участию в производственной системе?
Директор по развитию производственной системы ОМК Александр Иванов рассказывает: «Если меня спросить, в чем секрет успеха при развитии бережливого производства, то мой ответ будет коротким: человек. Известный американский ученый Уильям Эдвардс Деминг сформулировал четырнадцать ключевых принципов менеджмента, большинство из которых направлено именно на человека — работника компании. Сейчас мне хотелось бы выделить четыре из них: учредите лидерство; изгоняйте страхи; устраните произвольные числовые нормы и задания; дайте работникам возможность гордиться своим трудом. В ОМК взята за основу философия Деминга — мы в компании развиваем институт лидерства, выстраиваем систему, позволяющую каждому работнику свободно выражать свое мнение и предлагать решения по совершенствованию его рабочего пространства и бизнес-процессов. Для всех сотрудников разработана и действует система целеполагания и оценки результативности, действуют обоснованные нормы и нормативы производительности агрегатов и производительности труда рабочих, система подачи предложений по улучшениям позволяет выявить лучших работников, поощрять их заслуги и давать возможности для дальнейшего развития. Специфика нашего производства на ВМЗ — технологические линии. От работника в первую очередь требуется строгое соблюдение технологических режимов работы оборудования и выполнение установленных норм и правил. Мы также поощряем предложения по улучшениям, совершенствованию процессов, за которые отвечает работник. Поэтому для нас наиболее предпочтительна повременно-премиальная система оплаты труда. Эта система позволяет установить уровень вознаграждения, адекватный вкладу каждого работника».
В целом можно заметить, что средние зарплаты на ВМЗ значительно превосходят средние зарплаты по региону (Нижегородская область), по трубной отрасли и по металлургии в целом. И это явно должно стимулировать людей закрепиться на этом предприятии, сделать там карьеру.
Другой вопрос, что не столь выигрышно смотрится ряд иных предприятий ОМК — компании еще много над чем предстоит работать (см. график 2).
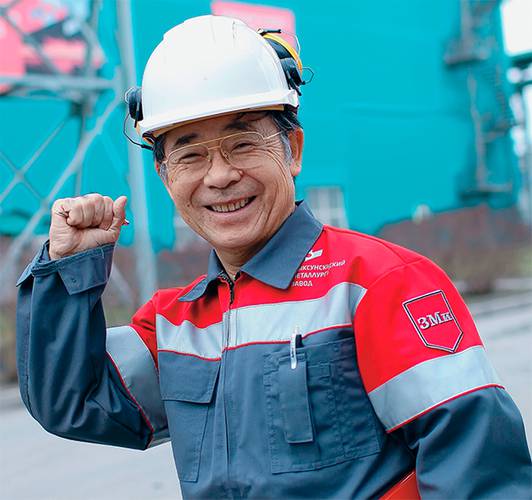
Развиваться всем и сейчас
Тацуми Кимура утверждает, что если сравнивать российский бизнес с японскими компаниями, то можно отметить одну особенность. В России довольно сильное руководство — во всяком случае, оно обладает необходимыми знаниями и компетенциями. Но в отличие от Японии никакого внимания не уделяется линейному персоналу.
«Есть системы производства, которые может создать менеджмент, линейный персонал в рамках этих систем будет выполнять какую-то стандартизированную работу, — объясняет Тацуми Кимура. — Да, это очень хорошо, и это нужно делать. Но это только 60 процентов успеха — все остальное рождается внизу. Те операторы, которые на местах, на линии выполняют стандарты, сами чувствуют проблемы, те точки улучшения, которые имеются. Если уделить внимание развитию линейных руководителей, линейного персонала, то это даст большую отдачу. Если взять в целом российские компании, то их отличает высокая компетенция топ-менеджмента и слабый линейный персонал, слабые линейные руководители. Это не относительно ОМК сказано, это об общей ситуации в российских производственных компаниях. Надо, чтобы персонал на всех уровнях был одинаково силен. Потому что это база, на этом все держится. Я бы даже сказал, что у нас в Японии более сильная вот эта базовая часть — линейный персонал компаний».
Актуален ли этот вопрос для российской экономики сейчас, когда на слуху разговоры о критическом отставании в производительности труда, а производственная система, мол, может служить лишь инструментом тонкой наладки хорошо отлаженного механизма?
В ОМК с этим категорически не согласны.
«Все еще моден штамп, что в России крайне низкая производительность труда, — говорит Александр Иванов. — Безусловно, у нас есть значительный потенциал повышения производительности труда. Но когда приводят сравнение с уровнем производительности труда в западных компаниях, то не учитывают различную организацию производственных и вспомогательных процессов в России и на Западе. Так, в Европе очень развит аутсорсинг различных функций, включая основные технологические. В России чаще встречается ситуация, когда предприятие является градообразующим, например в Сибири или на Урале, где крайне слабо развит аутсорсинг. Поэтому не удивительно огромное различие в производительности труда на российском заводе и на заводе в Европе. К бенчмаркингу в условиях различной структуры экономики нужно подходить очень аккуратно. В моей практике были случаи, когда разница в производительности между двумя рассматриваемыми предприятиями, на первый взгляд гигантская, после учета всех факторов становилась минимальной».
По мнению Александра Иванова, есть два фактора, которые обусловливают более низкую производительность труда на российских предприятиях — морально устаревшее оборудование и неэффективная организация трудовых и технологических процессов. В первом случае необходимо приобрести новое современное оборудование, во втором — применять инструменты бережливого производства.
«Инструменты бережливого производства на первом этапе позволяют получить самые большие эффекты, снять “низко висящие плоды”, а также привить коллективу определенную производственную культуру, нацеленную на непрерывное совершенствование», — говорит Александр Иванов.
В ОМК внедрение производственной системы происходило в два этапа (см. таблицу 2); несмотря на довольно короткий срок реализации, первые результаты уже видны.
Так, за два года длительность переналадок в основных цехах ВМЗ сократилась на 55%, что дало экономический эффект в размере порядка 300 млн рублей и позволило повысить гибкость производства. Кроме того, у предприятия появилась возможность браться за сравнительно небольшие заказы, число которых в последнее время увеличивается, в то время как новых крупных трубопроводных проектов в ближайшей перспективе не ожидается.
Среднюю продолжительность погрузки машины на ВМЗ удалось сократить с 17 часов до четырех, временны́е затраты на подготовку комплекта сопроводительной документации при отправке труб по железной дороге уменьшились с 20,5 часа до 3,8 часа. Сегодня сотрудники ВМЗ каждый месяц подают около двух тысяч предложений по улучшениям. За последние годы ВМЗ добился существенного повышения качества продукции, что помогло ОМК усилить позиции на российском и мировом рынке сварных труб, в частности в нефтегазовом сегменте.
Еще два года назад ОМК в целом по размеру выручки на одного занятого демонстрировала наилучшие показатели по сравнению с основными конкурентами. Отдельно взятый ВМЗ показал еще более высокие результаты (см. график 3).
«Развитие и применение инструментов бережливого производства вместе с модернизацией позволило нам последние два с половиной — три года непрерывно улучшать большинство технико-экономических показателей, каждый год мы получаем экономический эффект на миллиарды рублей», — резюмирует Александр Иванов.