Президент «Норникеля» Владимир Потанин рассчитывает, что через некоторое время продукция компании будет позиционироваться как «зеленая». Пять лет назад руководство «Норникеля» приняло долгосрочную производственную стратегию. Она предполагает радикальную перестройку всех технологических процессов, в том числе для повышения экологической безопасности производства.
При общей стоимости модернизации более 20 млрд долларов до 2023 года, около 5 млрд долларов выделены на экологические мероприятия. Текущая задача — добиться к 2023 году сокращения выбросов в атмосферу более чем на 75%, снизить сбросы загрязняющих веществ более чем на 80%.
Для этого из технологической цепочки «Норникеля» удаляются наиболее «вредоносные» переделы, внедряются новые, максимально щадящие для окружающей среды технологии. Реализуется программа развития минерально-сырьевого комплекса, модернизация обогатительных и металлургических производств позволяет извлекать больше металлов из руды при меньших затратах энергии с попутным сокращением выбросов диоксида серы и прочих производственных отходов.
Чтобы представить размах этой кампании, надо понимать, что «Норникель» — это десятки подразделений, ключевые из которых входят в Заполярный филиал с центром в Норильске и в Кольскую горно-металлургическую компанию в Мурманской области. При этом проводимая компанией масштабная модернизация — с «перетасовкой» производственных цепочек по всей группе, ликвидацией отдельных предприятий — осуществляется без снижения текущих объемов производства и, соответственно, с сохранением лидерских позиций компании на мировых рынках.
На пути к «зеленой» продукции
Борьба со снижением негативного воздействия на окружающую среду в «Норникеле» затрагивает все переделы — от обогащения руды до рафинирования никеля и меди.
«Норникелю» достались сульфидные руды, которые по химическому составу представляют собой соединения серы с тяжелыми металлами. В концентрате, который поступает на плавку после обогащения, серы еще много, в конечном же продукте ее быть не должно. Поэтому в процессе производства она может оседать в хвостах, сточных водах, попадать в атмосферу. Соответственно, бороться с серой «Норникелю» нужно по всей производственной цепочке — от производства концентрата до последнего передела.
Задача номер один — отправлять на плавку концентрат с максимально высоким содержанием металла. Более высокий процент металла в концентрате снижает объем плавки и, как следствие, дает меньше выбросов в атмосферу.
В прошлом году «Норникель» завершил модернизацию Талнахской обогатительной фабрики (ТОФ), которая обошлась компании в 32,7 млрд рублей. Производственные мощности фабрики были увеличены более чем на 35% — до 10,2 млн тонн руды в год. Модернизация позволила значительно повысить содержание металла в концентрате и увеличить количество серы в хвостах — отходах, которые остаются после обогащения.
Для хранения хвостов «Норникель» построил в Талнахском районе новое хвостохранилище проектным объемом 22,8 млн кубометров и стоимостью около 11,4 млрд рублей. Хвостохранилище построено с учетом всех экологических требований и обеспечивает максимально безопасное для окружающей среды хранение промышленных отходов.
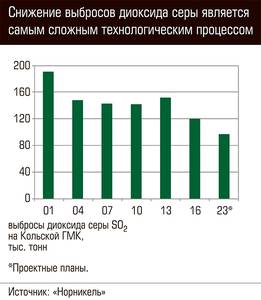
Концентрат «бедный» и «богатый»
На Кольской ГМК «Норникель» решил вопросы с концентратом более радикальным способом. В марте этого года на обогатительной фабрике в Заполярном началась реализация проекта по разделению концентрата на «бедный» и «богатый». «Богатый» — с более высоким содержанием металла — будет доставляться в поселок Никель для производства файнштейна и далее в Мончегорск для изготовления катодного никеля и другой товарной продукции. «Бедный» — с более низким содержанием металлов — будут продавать сторонним потребителям.
Проектная мощность линии по производству концентрата составит около 400 тыс. тонн. Оборудование поставит давний партнер «Норникеля» — финская компания Outotec. Стоимость всего проекта, который, как ожидается, будет завершен к концу 2019 года, составляет более 4 млрд рублей.
«Запуск разделения концентрата на Кольской ГМК позволит не только произвести диверсификацию товарной продукции в соответствии со стратегией развития “Норникеля”, но и решить важнейшую экологическую задачу — снизить выбросы диоксида серы, тем самым уменьшив негативное воздействие на природу», — пояснил «Эксперту» начальник управления научно-технического развития и экологической безопасности Кольской ГМК Александр Тюкин.
Использование в производственной цепочке «богатого» концентрата даст Кольской ГМК возможность вывести из эксплуатации одну рудно-термическую печь, что и обеспечит снижение технологических выбросов в атмосферу. В 2019 году снижение выбросов диоксида серы в поселке Никель (на границе с Норвегией) составит 50% по сравнению с уровнем 2015 года.
Ранее, в 2015 году, на Кольской ГМК отказались от обжига концентрата, что также привело к снижению выбросов диоксида серы в атмосферу. Теперь концентрат брикетируют и уже потом отправляют на плавку в рудно-термические печи. Общие затраты на реализацию этого проекта составили 2,8 млрд рублей.
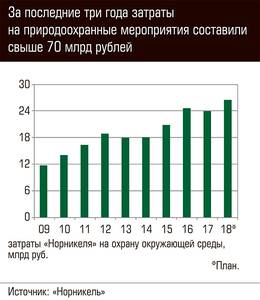
Металлургическая перетасовка
Поистине историческим событием для жителей Норильска — самого северного города в мире с населением свыше 170 тыс. человек — стало закрытие в 2016 году Никелевого завода. Он был построен еще в 1942 году для военных нужд. Очевидно, что тогда вопрос экологии в повестке дня не фигурировал.
Никелевый завод был одним из самых самым неэкологичных предприятий в России. Выбросы вредных веществ превышали 380 тыс. тонн в год. Это в два с половиной раза больше, чем все суммарные выбросы такого крупного промышленного города, как Красноярск.
Теперь их просто нет.
«Норникель» ликвидировал завод поэтапно, закрыв его при этом на два месяца раньше запланированного срока. Сотрудники были трудоустроены на других предприятиях группы. Часть (по их желанию) была переселена в другие регионы, жилье приобреталось за счет металлургической компании.
«По оценкам экспертов Общероссийской общественной организации “Зеленый патруль” после закрытия Никелевого завода на 30 процентов снизилось общее загрязнение жилой зоны Норильска», — говорит эксперт Центра общественного мониторинга ОНФ по проблемам экологии и защиты леса, председатель правления Общероссийской общественной организации «Зеленый патруль» Андрей Нагибин.
По словам эксперта, химический анализ снежного покрова, накопленного за зимний период в апреле 2017 года, показал, что содержание тяжелых металлов в пробах не превышает норм для рыбохозяйственных водоемов страны.
Закрытие Никелевого завода не привело к снижению производства — компания органично переформатировала производственные процессы. Плавка никелевого концентрата была перенесена на Надеждинский метзавод, производственные мощности которого были увеличены для этого на 26% — до 2,4 млн тонн.
Электроэкстракция делает мир чище
Снижать воздействие на окружающую среду на металлургической площадке Кольской ГМК в Мончегорске удастся за счет внедрения передовой технологии получения никеля путем электроэкстракции. Это способ электролитической очистки никеля, при которой в электролизные ванны металл загружается не в виде анодов, а сразу в виде раствора (электролита). В результате перехода на эту технологию исчезает необходимость в изготовлении анодов посредством плавки. Исключение из технологического процесса дуговой анодной электропечи существенно снижает выбросы загрязняющих веществ.
Первый пусковой комплекс — 42 современные электролизные ванны — был введен в эксплуатацию в конце прошлого года. В мае предприятие приступило к следующему этапу — установке 93 ванн.
В целом проект стоимостью более 24 млрд рублей предусматривает поэтапный перевод 476 электролизных ванн цеха электролиза никеля на технологию электроэкстракции.
Значительно повысить экологичность производства на Кольской ГМК удалось благодаря установке по утилизации солевого стока никелевого рафинирования стоимостью 1,7 млрд рублей. Она позволяет исключить сброс сточных вод в производственно-ливневую канализацию из цеха электролиза никеля. В основе этого нового технологического участка — установка швейцарской компании Evatherm AG для выпаривания солевого стока (раствора солей, образующегося в результате применения химикатов в производстве электролитного никеля) с последующей сушкой и упаковкой этих солей в товарном виде.
Эти соли, которые раньше просто сливали в технологический отстойник, теперь, после глубокой очистки, продают целлюлозно-бумажной и химический отраслям. Оставшаяся вода, содержащая ценные для технологии растворенные компоненты, не сливается в природный водоем, а возвращается в электролизное производство.
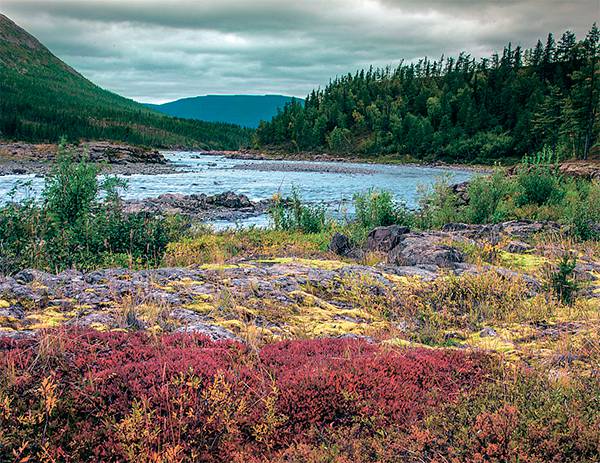
«Серный проект» переходит в активную фазу
В прошлом году компания определилась с конфигурацией «Серного проекта» на Надеждинском металлургическом заводе (НМЗ). «Норникель» рассматривал для НМЗ два варианта — производство элементарной серы и производство серной кислоты с последующей ее нейтрализацией. Выбор был сделан в пользу второго. Технология, которую разработала компания «Уралмеханобр», предполагает производство из серной кислоты безопасного гипса. Предусматривается возможность его долговременного хранения на специально оборудованном гипсохранилище в районе НМЗ. Параллельно проводятся исследования возможности переработки и использования гипса на территории Норильского промышленного района в качестве компонента для закладки горных выработок в рудниках Заполярного филиала.
Кроме того, как говорит руководитель проектного офиса «Серного проекта» Медного завода (МЗ) Андрей Северилов, важное преимущество этого проекта — возможность максимально использовать отечественное оборудование и материалы. «Это существенно снижает риски, связанные с применением дорогостоящей импортной техники и соответствующими лицензионными ограничениями», — подчеркивает он.
Финальным продуктом на МЗ (он также входит в периметр «Серного проекта») будет по-прежнему элементарная сера. Однако ее производство будет существенно расширено. Сейчас компания производит на Медном заводе до 80 тыс. тонн элементарной серы. В планах — увеличить производство до 280 тыс. тонн.
В прошлом году здесь же запустили установку по производству из диоксида серы сульфит-бисульфитного реагента. Помимо экологического эффекта компания получила и экономический «бонус» — с собственным реагентом, который используется в производстве, отпала необходимость закупать его на стороне.
По словам Андрея Северилова, для реконструкции производства элементарной серы на МЗ проведены необходимые испытания на действующей установке получения серы. Выполнены необходимые технико-экономические расчеты для выбора оптимальных вариантов утилизации диоксида серы. Кроме того, обследованы здания и сооружения, которые будут задействованы в проекте. Уже выполнена основная часть инженерных изысканий на площадке.
Идет разработка рабочей и конструкторской документации на оборудование. Параллельно «Норникель» проводит тендер на выбор генподрядчика.
Для проекта на НМЗ сейчас разрабатывается проектная документация, и, как ожидается, во втором полугодии 2018-го будет объявлен тендер на выбор генподрядчика для дальнейшей реализации проекта.
Комплексный «Серный проект» будет реализован к концу 2022 года. Он позволит улавливать до 560 тыс. тонн диоксида серы на Медном заводе и до 1,2 млн тонн диоксида серы на Надеждинском заводе. Это позволит снизить выбросы диоксида серы в Норильском промышленном районе на 75% по сравнению с 2015 годом до требуемого отечественным законодательством уровня. Стоимость комплекса мероприятий, направленных на снижение выбросов диоксида серы в Заполярном филиале компании, составляет около 2,5 млрд долларов.
Масштабные преобразования предполагают реконфигурацию металлургического производства на МЗ и НМЗ. «Норникелю» необходимо сконцентрировать на Надеждинском заводе переделы производства медно-никелевого штейна и черновой меди, которые генерируют богатые по содержанию диоксида серы отходящие газы. НМЗ уже является центром плавки никелевого штейна и файнштейна (после закрытия Никелевого завода). Сюда же переносится и передел конвертирования медного штейна (то есть производство черновой меди) с расположенного в черте Норильска МЗ. По сути, этот передел изымается из производственной цепочки Медного завода, а на Надеждинском строится комплекс непрерывного конвертирования. Эта технология предполагает безостановочную работу конвертера, что, в отличие от цикличного производства, не дает неорганизованных выбросов отходящих газов.
«Норникель» находится еще в середине своего пути к «зеленому» металлу. Однако экологи уже фиксируют положительные изменения. «Наиболее показательно состояние растительного покрова на границе санитарно-защитных зон предприятий “Норникеля”, — говорит Андрей Нагибин. — Повсеместное восстановление естественной тундровой растительности наглядно свидетельствует о значительном снижении загрязнения атмосферного воздуха в последние годы».