Мы привыкли думать о России как о сказочной кладовой, с лихвой обеспеченной всеми необходимыми богатствами недр. Подготовленный недавно Министерством природных ресурсов Государственный доклад о состоянии и использовании минерально-сырьевых ресурсов Российской Федерации показывает, что по целому ряду видов природных ресурсов наша страна критически зависит от импорта. Причем этот импорт осуществляется из небольшого числа стран, нередко — потенциально или уже явно недружественных России.
В мире нарастает противостояние великих держав, которое все чаще выплескивается в ограничительные меры экономического характера. Санкции, запретительные пошлины и прямые товарные эмбарго, которыми так полюбили разбрасываться в последнее время наши «уважаемые партнеры», — все говорит о том, что единый мировой рынок с его возможностями использования «преимуществ Рикардо» трещит по швам.
И даже если прогнозы о неизбежном распаде существующего миропорядка на отдельные военно-политические и торгово-экономические блоки, смотрящие друг на друга исключительно в прицел, окажутся чересчур скептическими, обеспечить суверенитет страны и ее экономики невозможно, если не найти возможностей снизить зависимость от импорта стратегического сырья в случае возникновения угрозы его поставок.
Сегодня можно выделить семь основных наиболее уязвимых позиций российского сырьевого импорта. Это уран, марганец, хром, олово, титан, алюминиевое сырье, редкоземельные металлы. Ниже мы разберем ситуацию по каждому из перечисленных ресурсов подробнее.

Исходные позиции: авангард
Все вышеназванные критические товарные позиции сырьевого импорта можно условно свести в три группы, в зависимости от влияния соответствующих отраслей России в мировом масштабе. Во-первых, это условная группа лидеров (уран, титан), то есть отраслей, где роль нашей страны чрезвычайно велика. Во-вторых, это «крепкие середняки» (хром, марганец, алюминиевое сырье). В-третьих, это отрасли, где в мировом масштабе Россия не заметна вовсе, но для нас самих существование этих отраслей критически важно (олово, редкоземельные металлы).
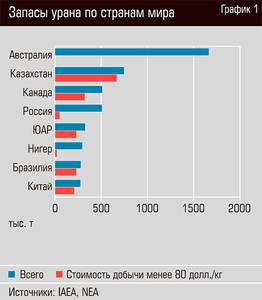
Уран используется как в военных целях, обеспечивая нам пресловутый ядерный щит, так и для решения задач вполне мирных, главная из которых — атомная энергетика.
Весь ядерный цикл в России контролируется государственной корпорацией «Росатом». Урановое сырье, добываемое или ввезенное в страну извне, поступает на переработку на предприятия Сибирского химического комбината (СХК), входящего в разделительно-сублиматный комплекс корпорации ТВЭЛ. На СХК сконцентрированы все конверсионные мощности корпорации, полностью обеспечивающие отраслевые потребности в гексафториде урана (UF6). Часть полученного сырьевого гексафторида урана реализуется на внутреннем рынке и поставляется на другие предприятия разделительно-сублиматного комплекса: Уральский электрохимический комбинат и ПО «Электрохимический завод» в Зеленогорске. Часть поступает на завод по разделению изотопов СХК, где получают обогащенный урановый продукт, реализуемый как внутри страны (поступает на Новосибирский завод химконцентратов и Машиностроительный завод в Электростали), так и на внешнем рынке. Ядерное топливо российского производства полностью обеспечило реакторные потребности Ирана, Чехии, Словакии, Венгрии, Болгарии и Армении. «Росатом» также частично обеспечил потребность в ядерном топливе Украины (85%), Финляндии (36%), Индии (31%) и Китая (3%). Доля корпорации в мировом производстве ядерного топлива составила 17%.
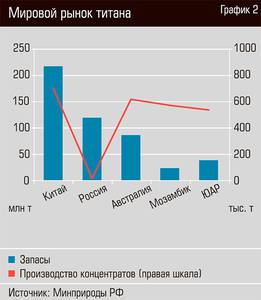
Таким образом, потребление урана в России, с учетом экспортных обязательств по ядерному топливу, достигает 8000–9000 тонн в год. «Росатом» имеет амбициозные планы зарубежной экспансии, а также расширения использования ядерных силовых установок малой мощности (см. «Атомный экспорт», «Эксперт» №39 за 2018 год). То есть потребность в урановом сырье только вырастет. Однако годовая добыча урана внутри страны составляет всего лишь порядка 3000 тонн в год.
Другая отрасль, демонстрирующая российские успехи в мировом масштабе, — производство титана. Так, на мировом авиакосмическом рынке российская титановая продукция занимает 30%.
Основные виды титановой продукции — губчатый титан, перерабатываемый в титановые слитки и продукцию из титановых сплавов; пигментный диоксид титана; покрытия сварочных электродов и сварочная проволока.
Губчатый титан в России производится главным образом на титано-магниевом комбинате корпорации «ВСМПО-Ависма» в Березниках Пермского края (95%), в меньшем количестве — на мощностях Соликамского магниевого завода.
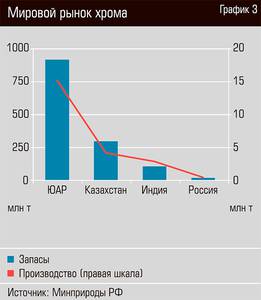
Титановые сплавы используется для изготовления корпусов самолетов и ракет, химического оборудования, медицинских инструментов и протезов. Россия занимает второе место в мире (после США) по выпуску титановых слитков и второе же (после Китая) — по выпуску титанового проката. Основной объем производства (98%) приходится на Верхнесалдинское металлургическое производственное объединение «ВСМПО-Ависма».
Пигментный диоксид титана находит применение в лакокрасочной, бумажной, пищевой промышленности. Основной производитель этого продукта в России — «Крымский титан».
В общем и целом существующие мощности титановой промышленности в России потребляют в год порядка 280 тыс. тонн титанового сырья (концентрата). При этом непосредственно внутри страны в 2017 году было добыто 369 тыс. тонн титановых руд, произведено 10 тыс. тонн титановых концентратов (полностью использованы Соликамским магниевым заводом). Наша титановая промышленность «сидит» на импортном сырье.
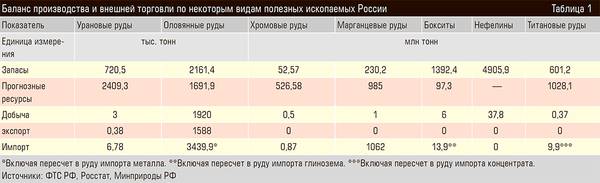
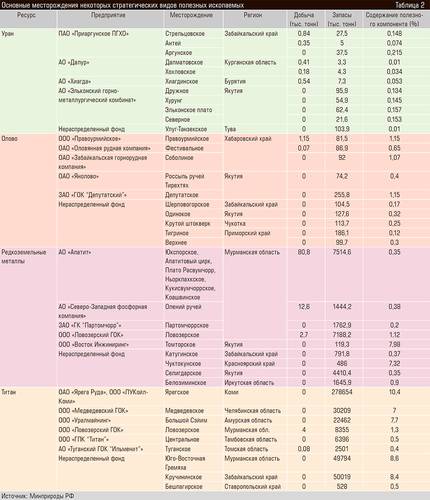
Исходные позиции: второй эшелон
Схожая ситуация с хромом. Хромовые руды и концентраты используются для выплавки феррохрома (Серовский завод ферросплавов, Челябинский электрометаллургический комбинат и другие), в меньшей степени — для производства металлического хрома и хромовых соединений (Новотроицкий завод хромовых соединений, Ключевский завод ферросплавов и другие).
Эта продукция имеет большую важность для нормального функционирования всей российской черной металлургии — а вместе с ней и машиностроения. Как известно, хром входит в состав легированных, нержавеющих, особо износостойких, бронированных, оружейных, огнеупорных сталей. Нержавеющая сталь должна содержать не менее 12% хрома. А сорта стали с содержанием хрома выше 30% используются для изготовления корпусов подводных лодок, сейфов, оружейных стволов пушек, металлорежущих инструментов, медицинского и химического оборудования, космических двигателей.
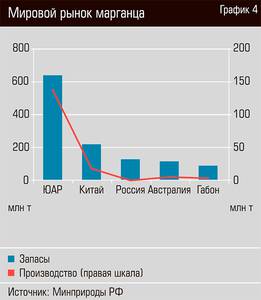
Потребность российских предприятий в хроме на сегодня может быть оценена в 1,4 млн тонн в год. Реальный объем добычи внутри России лишь немногим превышает 500 тыс. тонн. Разница покрывается за счет импорта, главным образом из Казахстана и ЮАР.
Помимо хрома для нормального функционирования черной металлургии нужен марганец. Свыше 90% всего производимого в мире марганца потребляется в виде ферромарганца — его добавляют в сталь, чтобы повысить ее ковкость, прочность, износоустойчивость. Увеличение содержания хрома до 11–14,5% используется в черной металлургии для изготовления «стали Гадфильда», особо высокопрочного сорта стали, используемого для производства элементов брони, траков гусениц танков и тракторов, стрелочных переводов, дробилок и тому подобных продуктов, рассчитанных на повышенные ударные нагрузки. В меньшей степени (в составе сплава с медью и никелем) марганец используется в электротехнике.
В России выпуск ферромарганца осуществляют четыре предприятия: Косогорский металлургический завод в Туле, Саткинский чугуноплавильный завод в Челябинской области, Челябинский электрометаллургический комбинат и Западно-Сибирский электрометаллургический завод в Новокузнецке. Потребность российской промышленности в марганцевом сырье может быть оценена в 1–1,1 млн тонн (не считая импорта марганца в виде готовых ферромарганцев и металлического марганца в размере 300 тыс. тонн в год). При этом собственная добыча в стране практически отсутствует, все потребности покрываются за счет импорта из ЮАР, Казахстана, Габона, Украины.
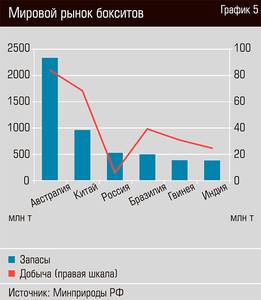
Россия имеет мощную черную металлургию (объем выплавки стали — 71 млн тонн, пятое место в мире), которая обеспечивает как внутренние потребности, так и поставки на экспорт (стальной прокат — 13,4 млн тонн, трубы — 2,1 млн тонн). Из этой стали производится техника и вооружения, одна из важнейших несырьевых статей российского экспорта. И все это имеет маленькое «кощеево яйцо» — импорт легирующих материалов.
В цветной металлургии дела не лучше. Россия играет довольно заметную роль на мировом рынке алюминия. Так, если все мировое производство алюминия в 2017 году оценивалось International Aluminium Institute на уровне 63,4 млн тонн, то в России производство только первичного алюминия составило 3,7 млн тонн (6% мирового рынка). Весь отечественный первичный алюминий произведен на девяти заводах Объединенной компании «Русал». Подавляющая часть производства сосредоточена в Сибири, где Красноярский, Братский, Саяногорский, Хакасский, Иркутский и вступивший в строй в 2016 году Богучанский алюминиевые заводы используют дешевую электроэнергию ГЭС Ангаро-Енисейского каскада.
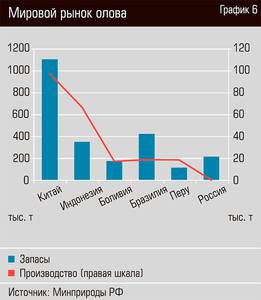
Алюминий производится из оксида алюминия Al2O3. В алюминиевой промышленности он является составной частью полуфабриката —
глинозема. В виде отдельного минерала оксид алюминия известен как корунд (с примесями — рубин, сапфир). Эти минералы используются в оптике и электронике, ювелирном деле, но общий объем этих рынков в натуральном выражении несопоставим с алюминиевым.
Производство глинозема в России также почти полностью сосредоточено на предприятиях «Русала» (Уральский и Богословский алюминиевые заводы, Ачинский глиноземный комбинат). В качестве сырья выступают бокситы или нефелины. Последние используются только в России и только на мощностях Ачинского комбината.
И здесь уже начинаются проблемы. Потребность алюминиевых заводов России в глиноземе (при имеющихся объемах производства) оценивается в 7,2 млн тонн в год. Фактически все предприятия страны в 2017 году произвели 2,8 млн тонн глинозема. Алюминиевая отрасль на две трети зависит от импорта полуфабриката. Основная его масса импортируется с Украины, из Австралии, Казахстана, Бразилии, Ямайки.
Исходные позиции: арьергард
Олово используется, как правило, в виде различных сплавов. Самый известный из них, пожалуй, хорошо всем известная бронза (сплав с медью). А кроме того, это специализированные материалы для изготовления подшипников, фольги для упаковки, белой пищевой жести, припоев, проводов, конденсаторов, для нанесения антикоррозионных покрытий на металлы и легирования конструкционных титановых сплавов.
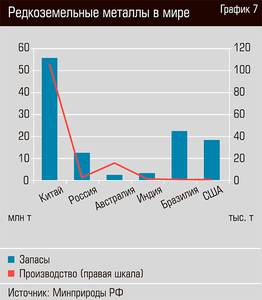
Производством металлического олова в России занимается одно-единственное предприятие — Новосибирский оловообрабатывающий завод. Российская оловянная промышленность в мировом масштабе — это доли процента. Этого слишком мало даже для существующего российского рынка, сильно подрастерявшего в ходе рыночных преобразований свои подшипниковые и электротехнические мощности. На протяжении всего последнего десятилетия объем импорта металлического олова в Россию стабильно превышал его внутреннее производство.
Разумеется, по мере восстановления этих мощностей и компетенций потребность России в олове будет возрастать. Что в существующих реалиях означает и увеличение зависимости от импортных поставок этого металла.
Потребление редкоземельных металлов в натуральном выражении тоже невелико: все мировое производство немногим превышает 63 тыс. тонн в год. К числу редкоземельных металлов относят группу из 17 химических элементов: скандий, иттрий, лантан и лантаноиды (церий, празеодим, неодим, прометий, самарий, европий, гадолиний, тербий, диспрозий, гольмий, эрбий, тулий, иттербий, лютеций). Безусловный мировой лидер в производстве редкоземельных металлов — Китай (83%). Формально вроде как наш если не союзник, то дружественная страна. Но страна, ревностно блюдущая свои интересы — или то, что она под ними понимает. И они далеко не всегда совпадают с российскими.
Так, начиная с 2009 года Китай неуклонно сокращал экспортную квоту на редкоземельные металлы. Сначала это было 50,2 тыс. тонн в год, но уже в 2010 году она снизилась до 30,2 тыс. тонн в год. Квоты были отменены в 2015-м, но ничто не мешает их вернуть.
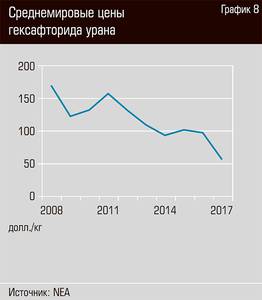
Потребление редкоземельных металлов в России сейчас составляет порядка 2000 тонн в год. Примерно 70% используется в электронике, несколько сотен тон в год также необходимо для выпуска катализаторов для нефтепереработки, меньшее количество применяется при производстве магнитов и в оптике. В целом лишь около четверти редкоземельных металлов в России используется для производства продукции гражданского назначения, остальное — для выпуска изделий военно-технического назначения.
Основные потребители редкоземельных металлов в России — предприятия, входящие в структуру «Ростеха»: «Росэлектроника», Объединенная двигателестроительная корпорация», холдинг «Швабе» и т. д. То есть совершенно очевидно, что это удобная мишень для потенциального давления на Россию.
Сейчас основным производителем редкоземельной продукции в России является Соликамский магниевый завод. Предприятие производит фактически полуфабрикаты — карбонаты и оксиды самария, европия, гадолиния, лантана, неодима, прометия, церия. Поставки готовой продукции на внутренний рынок не превышают 150 тонн, а основная масса карбонатов производства Соликамского магниевого завода, в силу отсутствия внутри России собственных крупных мощностей по разделению редкоземельных металлов, традиционно экспортировалась для дальнейшей переработки на предприятия компании AS Silmet в Эстонию.
Пространство для маневра
Таким образом, функционирование и дальнейшее развитие целого ряда важных отраслей промышленности, в том числе производства продукции военного назначения, оказывается в жесточайшей зависимости от импорта ключевых ресурсов из небольшого числа стран-поставщиков, часто недружественных.
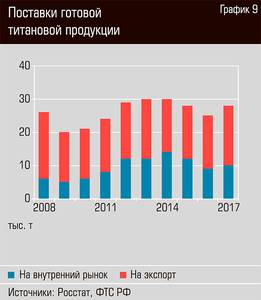
Можно ли считать это неизбежной данностью, которую никак нельзя преодолеть? На самом деле нет. Как следует из данных Минприроды, по всем вышеперечисленным видам ресурсов Россия формально обладает весьма неплохой ресурсной обеспеченностью.
Так, российская сырьевая база урана учитывается Государственным балансом запасов полезных ископаемых в размере 716,6 тыс. тонн категорий А+В+С1+С2. По данным МАГАТЭ, страна занимает четвертое место в мире после Австралии, Канады и Казахстана, располагая запасами урана в размере 507,8 тыс. тонн. В любом случае этого хватило бы с лихвой и надолго. Потенциал прироста запасов тоже велик — прогнозные ресурсы урана в стране могут быть оценены на уровне до 2409,3 тыс. тонн, что потенциально способно вывести Россию в лидеры по обеспеченности ураном.
То же и с запасами титана, которые превышают 600 млн тонн, правда, в разрабатываемых, осваиваемых и разведываемых месторождениях сосредоточено 117,5 млн тонн. Однако и этого с лихвой хватило бы на покрытие всех потребностей. По величине активной части запасов Россия занимает третье место в мире после Китая и Украины. Причем потенциал прироста запасов диоксида титана в стране велик, общий объем прогнозных ресурсов оценивается в 1028 млн тонн.
Сырьевая база хромовых руд России невелика в сравнении с основными мировыми производителями. Но и этого с лихвой хватило бы на десятилетия: Государственным балансом запасов полезных ископаемых учтено 52,1 млн тонн хромитов категорий А+В+С1+С2. А потенциал прироста запасов хромовых руд в стране весьма значителен: только наиболее достоверные прогнозные ресурсы категории Р1 более чем в два с половиной раза превышают запасы. Сейчас в разработку вовлечено 7,6 млн тонн, или менее 15% запасов хромовых руд страны.
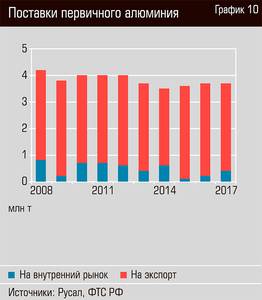
А вот сырьевая база марганцевых руд России довольно велика. В стране учтено 230,2 млн тонн запасов категорий А+В+С1+С2. Оценка прогнозируемых ресурсов еще выше — 985 млн тонн. Величина одних только условно активных запасов марганцевых руд России превышает промышленные запасы Австралии, занимающей третье место в мире по объемам выпуска товарно-сырьевой марганцевой продукции.
В теории неплохо обеспечена сырьевой базой и отечественная алюминиевая промышленность, точнее, производство глинозема. Запасы бокситов оцениваются в колоссальную величину — почти 1,4 млрд тонн. Только в разрабатываемых и осваиваемых месторождениях заключено 513,5 млн тонн запасов промышленных категорий. Столь же колоссальна сырьевая база нефелинов — учтено 4,9 млрд тонн запасов.
Учтенные в России запасы олова превышают 2,16 млн тонн, из которых свыше 75% подсчитаны по категориям А+В+С1. Только в разрабатываемых месторождениях заключено 209,6 тыс. тонн запасов этих же категорий, что обеспечивает стране пятое место в мире после Китая, Бразилии, Индонезии и Австралии. Перспективы прироста запасов олова в России также значительны: только прогнозные ресурсы наиболее достоверной категории Р1 превышают 611 тыс. тонн. Всего можно говорить о прогнозных ресурсах олова в 1,7 млн тонн.
Наконец, запасы редкоземельных металлов в России оцениваются в 26,9 млн тонн ΣTR2O3 (TR — условное обозначение для редкоземельных элементов). Это выводит нашу страну на второе место в мире, сразу после Китая (55 млн тонн). Даже с запасами только разрабатываемых и готовых к разработке месторождений (12,2 млн тонн) Россия выходит в число мировых лидеров.
Так что ресурсы у нас есть по всем критическим позициям.
Жемчуг мелок
Тем парадоксальнее, казалось бы, выглядит сложившаяся зависимость отечественной промышленности от импорта этих видов сырья.
На самом деле в большинстве случаев нужно говорить не только о количестве, но и о качестве ресурсов. Так, качество имеющихся в России урановых руд за редким исключением невысокое — среднее содержание урана составляет 0,1–0,2%. По данным Nuclear Energy Agency, при учете из доступных запасов урана только тех, разработка которых рентабельна при ценах менее 80 долларов за килограмм UF6, показатель России опускается более чем на порядок. При этом средние цены на UF6 в 2017 году опускались и до более низких отметок. Понятно, что при таких обстоятельствах и в условиях относительно свободного рынка «Росатому» выгоднее было ориентироваться на более качественные заграничные ресурсы.
Несколько смягчается это обстоятельство тем, что основной импорт урана в Россию приходится на поставки из Казахстана, с подконтрольных дочерним структурам «Росатома» предприятий, где себестоимость добычи, напротив, рекордно низкая — порядка 25–28 долларов за килограмм.
Значительная часть колоссальной сырьевой базы титана в России представлена труднообогатимыми рудами. Так, львиная доля разведанных запасов приходится на Ярегское месторождение в Республике Коми. Содержащиеся здесь нефтеносные лейкоксен-кварцевые песчаники отличаются довольно высоким содержанием полезного компонента (10,4% TiO2), но их обогащение затруднено (лейкоксен представляет собой тонкое срастание рутила, анатаза и кварца, переработка его требует сложной и дорогостоящей технологии). Для сравнения: китайские титановые руды, добываемые в провинции Сычуань, имеют содержание полезного компонента 6–13% при легкости в обогащении.
Российские хромовые руды обычно характеризуются повышенной железистостью и содержат не более 26% Cr2O3. А, например, для месторождений ЮАР этот показатель составляет 35–37%, в Индии — 42%, а в Казахстане и вовсе уникальные 52%.
Точно так же для сырьевой базы марганцевых руд в России, при том что она очень велика, характерно низкое качество руд. Среднее содержание марганца в отечественной руде находится в пределах 9–23%, в то время как у основных мировых игроков на этом рынке оно не опускается ниже 35%, а для высококачественных сортов превышает 40%.
Бокситы российских месторождений в основном низко- и среднесортные, трудновскрываемые, в отличие от легковскрываемых гиббситовых бокситов Австралии, Гвинеи и ряда других стран. Даже самые качественные российские бокситовые руды (месторождений Красная Шапочка, Кальинское, Ново-Кальинское, Черемуховское) залегают в карбонатных породах на глубинах до 1,2–1,3 км, что требует разработки шахтным способом, а удаленность основных районов размещения сырьевой базы — вложений в развитие инфраструктуры. В то время как большинство зарубежных игроков располагает месторождениями высококачественных бокситов неглубокого залегания, что позволяет использовать открытый способ добычи. Например, гвинейская руда при содержании полезного компонента до 65% подчас залегает на глубинах в районе одного метра от поверхности.
Обширная отечественная сырьевая база редкоземельных металлов привязана главным образом к апатит-нефелиновым месторождениям в Мурманской области. В месторождениях Хибинской группы учтено 40% всех российских запасов. Но содержание полезного компонента крайне мало (0,24–0,42% ΣTR2O3), и «Фосагро», разрабатывая эти руды на фосфор, извлечением редкоземельных металлов традиционно не занималась. Извлечение производилось только на Ловозерском месторождении, но и здесь содержание полезного компонента составляло в среднем 1,39% ΣTR2O3.
Для сравнения: австралийское месторождение Маунт-Уэлд выдает руды с содержанием полезного компонента до 23,6% ΣTR2O3, а уникальное по запасам китайское месторождение Байюнь-Обо может похвалиться показателем 5,7–6,7%.
Пожалуй, единственным исключением в этом списке выглядит российская сырьевая база олова. Она не только велика по объемам, но и может предложить месторождения с весьма достойными горно-геологическими условиями добычи и приличным содержанием полезного компонента (1–1,15%). Проблема в том, что эти месторождения далеко удалены от «цивилизации» (Яно-Индигирская оловоносная провинция на севере Якутии), поэтому их освоение сопряжено с большими транспортными издержками либо требует колоссальных инвестиций в развитие инфраструктуры. Более доступные в транспортном отношении альтернативы, как правило, имеют все тот же порок — низкое качество руды (в данном случае низкое содержание полезного компонента).
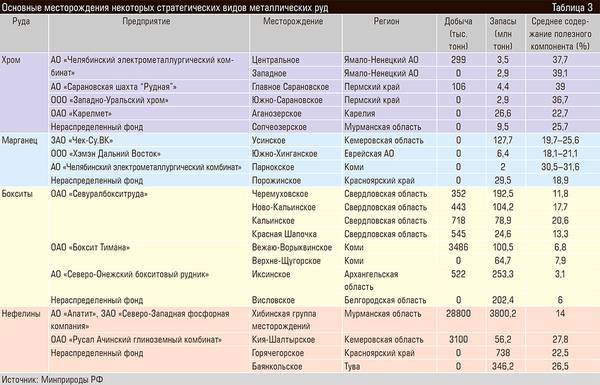
Дело техники
Таким образом, Россия теоретически имеет все возможности для импортозамещения по ключевым ресурсным позициям в случае долгосрочной военной угрозы. Но это потребует значительных затрат времени и потому не может быть срочным решением. А кроме того, потребуются финансовые затраты, которые частные инвесторы в мирное время нести не готовы — в силу значительно меньшей привлекательности этих проектов по сравнению с зарубежными альтернативами.
Страховкой на ближайшее будущее может быть только создание стратегического резерва соответствующих ресурсов в необходимых объемах на срок, необходимый для развертывания собственной добычи в критической ситуации.
Точно так же в обозримом будущем, несмотря на формально обширную сырьевую базу, Россия не станет нетто-экспортером соответствующих ресурсов.
Но отчаиваться не стоит. С одной стороны, многие отрасли, зависимые от импорта сырья, ориентированы на экспорт готовой продукции, свои собственные потребности Россия может удовлетворить и меньшим количеством ресурса. С другой стороны, в России уже предпринимаются попытки расширения добычи этих ресурсов.
Например, весной этого года началось строительство уранового рудника мощностью 1800 тонн в год (будет запущен в 2023 году) в Забайкалье. Проблемы зависимости от импортного уранового сырья этот рудник не снимет, но несколько снизит ее.
По хромовым рудам силами Всероссийского НИИ минерального сырья имени Н. М. Федоровского проводятся исследования по переработке высокожелезистых руд с целью повышения соотношения Cr2O3/FeO в концентратах для дальнейшего их использования при выплавке стандартного феррохрома. Уже разработана технология с применением восстановительного обжига с последующей магнитной сепарацией, позволившая получить концентраты с соотношением Cr2O3/FeO > 3. Отсутствие такой технологии было основной причиной невовлечения в освоение свыше 70% российских запасов хромовых руд.
Проводились работы по освоению крупнейшего в России Усинского марганцевого месторождения в Кемеровской области. Проект предусматривал возможность производства до 800 тыс. тонн марганцевых концентратов в год, что закрывало бы львиную долю российской потребности в марганце. Увы, реализация проекта была парализована экологической истерикой, охватившей жителей Красноярска в связи с планами строительства неподалеку от города ферросплавного завода (подробности см. «Порвем с индустриальным прошлым», «Эксперт» № 37 за 2012 год).
Нельзя не отметить и наметившиеся в последнее время позитивные сдвиги в ситуации с редкоземельными металлами. Производители минеральных удобрений, работающие с апатит-нефелиновые рудами, начали постепенно переходить к извлечению редкоземельных элементов. «Акрон» ввел в строй установку мощностью 200 тонн в год по выделению коллективного концентрата, содержащего оксиды церия, лантана и неодима. Группа «Фосагро» совместно с бельгийской Prayon запустила установку по извлечению РЗМ из фосфогипса — в будущем мощность предприятий группы по производству редкоземельных оксидов может составить 7000 тонн в год. «Воскресенские минеральные удобрения» также разрабатывают технологию доизвлечения полезных элементов из фосфогипса. Мощность установки составит 1700 тонн в год, но, к сожалению, сроки ее запуска сдвигаются из-за проблем с инвестициями.
Технологии не стоят на месте, и неудобные сегодня месторождения могут стать вполне привлекательными на новом технологическом уровне.