Региональный инжиниринговый центр (РИЦ, учредители — УрФУ, правительство Свердловской области, ОКБ «Новатор» и Машзавод им. Калинина) совместно с Кыштымским ГОКом (Челябинская область) выступили с инициативой создать в Кыштыме завод по выпуску аддитивных машин, порошков и сопутствующего оборудования. Предложение прозвучало на совещании при губернаторе Борисе Дубровском. «По нашим расчетам, целесообразно создавать предприятие с годовой мощностью не менее 700 — 800 машин, — заявил руководитель отдела развития РИЦ Петр Москвин. — Рентабельность такого производства составит 25%».
ГОК — далеко не первый партнер, которому инжиниринговый центр предлагает организовать серийный выпуск промышленных 3D-принтеров. Причем аппетиты РИЦ постоянно растут: в 2015 — 2016 годах речь шла о 50 — 100 машинах.
Насколько нам известно, аналогичными поисками занимаются еще несколько российских исследовательских групп. Но пока ни одна из них, несмотря на чрезвычайно позитивные прогнозы развития рынка аддитивных технологий (АТ), успеха не достигла.
Смерть заводов
Если говорить просто, АТ используются для формирования изделия при помощи послойного наращивания материала (металла, полимера, керамики), а не удаления его из заготовки. Продукт создается в специальном принтере согласно загруженной в него 3D-модели.
Теоретические преимущества подобного способа производства очевидны. Он, во-первых, на порядок (и это не преувеличение) сокращает срок изготовления деталей, узлов и конечных продуктов. Во-вторых, способствует существенной экономии материала (при обычных способах изготовления потери сырья могут составлять до 85%). В-третьих, за счет АТ можно создавать изделия чрезвычайно сложной геометрии. В-четвертых, напечатанные детали из-за особой структуры могут быть на 40 — 50% легче традиционных аналогов при сохранении всех физических характеристик. В-пятых, создание деталей из так называемых градиентных материалов (соединяют сразу два сырьевых компонента, переходящих друг в друга) позволяет придать им уникальные свойства (например, исключительную жаропрочность).
Но, пожалуй, самое главное преимущество АТ — это изменение промышленной парадигмы. Возможность передавать 3D-модели в любую точку мира позволяет напечатать изделие на месте и заменить гигантские производства на локальные инжиниринговые центры с необходимым оборудованием. «Это коренным образом изменит производственные и логистические цепочки, — прогнозирует генеральный директор компании «ЛВМ АТ» Олег Лысак. — От дистрибуции продукции мы перейдем к дистрибуции производства».
В США в 2015-м была даже запущена специальная программа Quality MADE, одна из целей которой — создать на крупных кораблях (например, авианосцах) цеха по выпуску деталей. Это избавит их от необходимости возить запасные части с собой. В апреле 2016-го в СМИ появилась информация, что судно ВМС Великобритании, несущее службу у берегов Антарктиды, для определения маршрута использовало беспилотник, напечатанный на борту.
Ученые любят рассказывать, что АТ зародились еще в XIX веке, когда француз Франсуа Виллем сделал первую фотоскульптуру. Он оборудовал специальную круглую комнату, в которой был обозначен точный геометрический центр. В этот центр ставили человека, и его одновременно снимали 24 камеры, встроенные в стены на равной высоте и равном расстоянии друг от друга. Так скульптор получал исчерпывающую информацию о модели со всех сторон и мог воссоздать ее в материале.
В качестве второго праотца АТ называется Йозеф Блантер, который в 1890 году придумал послойный метод изготовления пресс-форм для печати карт, на которых видны холмы, горы и низменности в строгом соответствии с топографическими линиями.
Современная история АТ началась, пожалуй, в 1986 году, когда Чарльз Халл (основатель 3D Systems) запатентовал способ послойного синтеза посредством ультрафиолетового излучения, сфокусированного на тонкий слой фотополимерной смолы.
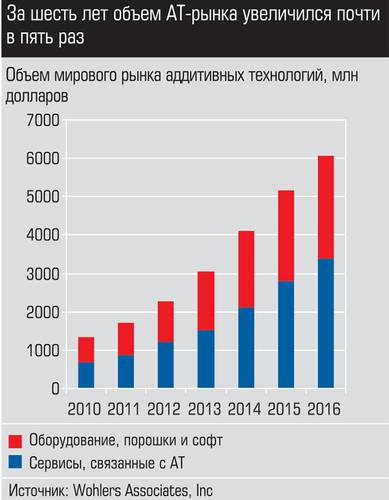
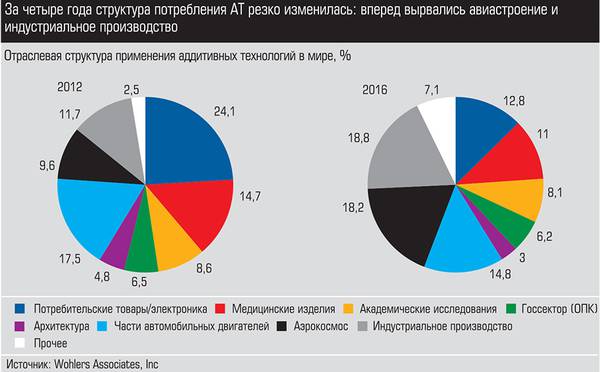
Бешеный принтер
С того времени мировой АТ-рынок начал расти лавинообразно, динамика радует до сих пор. По данным Wohlers Associates, в 2016 году его объем превысил 6 млрд долларов, что на 17,4% больше, чем в 2015-м. За последние десять лет рынок вырос в шесть раз. К слову, 6 миллиардов — это не так уж много. Для сравнения, продажи станков ЧПУ в мире в 2016-м достигли примерно 150 млрд долларов.
Всего в прошлом году было продано чуть больше 13 тыс. индустриальных аддитивных машин (аналитики Wohlers Associates относят к ним системы дороже 5 тыс. долларов), показатель 2015-го превышен на 4%. Подавляющее большинство реализованных принтеров работают с полимерами, на металлический сегмент пришлось всего 957 машин (808 в 2015-м). Главной страной-производителем аддитивного оборудования является Израиль (его доля превышает 35%). Здесь базируется крупнейшая в мире АТ-компания Stratasys.
С 2010 года средняя стоимость одного промышленного принтера постоянно растет (до этого она на протяжении десяти лет падала). Это, очевидно, связано со все более широким распространением машин, работающих с металлическими порошками. В 2016 году цена одной системы составила 104 тыс. долларов (показатель 2015-го — 97,4 тысячи, 2010-го — 62,6 тысячи).
В сегменте настольных 3D-принтеров — взрыв. Их продажи в 2016-м выросли почти на 50% к 2015-му и достигли 424 тысяч. Выручка от их реализации увеличилась на 42% до 464 млн долларов.
Продажи сырья для печати в 2016 году добрались до отметки 903 млн долларов. Это на 17,5% больше, чем в 2015-м. 39% этой суммы пришлось на фотополимеры. Доля металлических порошков пока не превышает 14% (но этот сегмент растет чрезвычайно активно и, судя по опросам производителей, в 2017-м должен увеличиться разом на 60%).
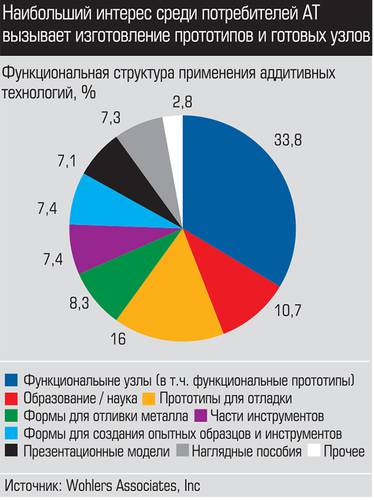
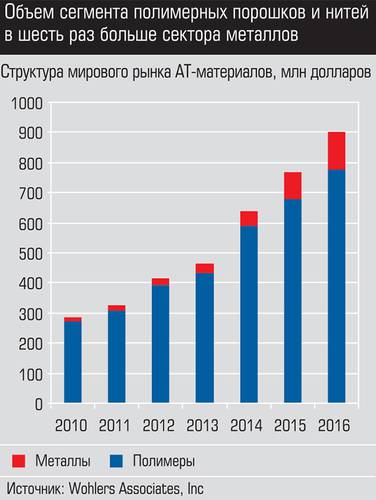
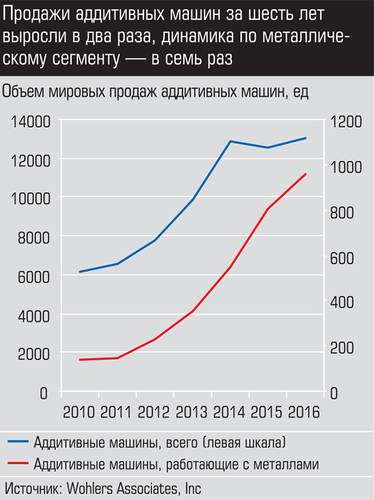
Самым активным потребителем 3D-машин в 2016 году была Северная Америка (понятно, что львиная доля пришлась на США): здесь установлено 38,7% всех систем, 29% — Азиатско-Тихоокеанский регион (в основном Япония и Китай), 28% — Европа.
По итогам последних 28 лет (Wohlers ведет исследования с 1988-го) впереди всех также США (36%). Второй эшелон — Китай, Германия и Япония (8,5 — 10%), третий — Великобритания, Франция, Италия и Южная Корея (3 — 4%).
Отраслевая структура применения АТ активно меняется. Еще в 2012-м ключевым потребителем этих технологий была сфера потребительских товаров и электроники. В 2016-м она уступила место сразу трем областям: автомобилестроению (в основном за счет повышенного интереса к 3D-печати со стороны японских и немецких производителей), авиастроению (здесь погоду делает одна компания — GE, которая запустила завод с 60 принтерами мощностью 90 тыс. лопаток турбин) и прочей промышленности.
Ключевой областью применения АТ по-прежнему остается прототипирование. Правда, по данным Wohlers Associates, на него в сумме приходится 30,5%. И это меньше, чем у функциональных узлов (34%). Некоторые эксперты радостно восклицают: наконец на принтерах начали печатать конечную продукцию! Однако мы полагаем, что в эти 34% «зашит» довольно большой кусок функциональных прототипов.
Прогнозы развития АТ-рынка исключительно позитивны. В Wohlers Associates уверены, что к 2021 году его объем превысит 26 млрд долларов. По оценкам аналитической компании Context, отрасль ежегодно будет прибавлять по 42% (в основном за счет настольных систем), к 2020-му доберется до планки 17,8 миллиарда. Аналитики Boston Consulting Group посчитали: если к 2035 году компаниям удастся внедрить 3D-печать хотя бы на 1,5% от общих производственных мощностей, то объем рынка превысит 350 млрд долларов.
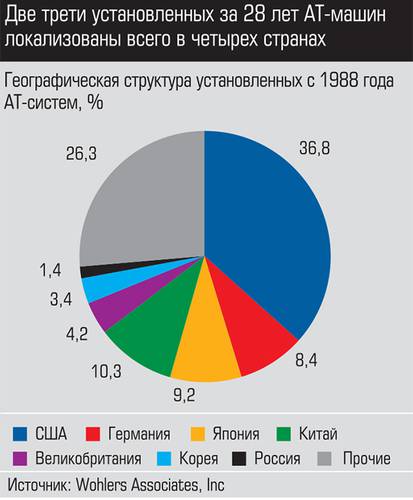
В следующей серии
Место России на этой картине завидным не назовешь. По данным Wohlers, с 1988 по 2016 год в нашей стране установлено 1,4% всех аддитивных машин. Минпромторг считает, что в РФ эксплуатируется около 600 — 650 промышленных 3D-принтеров, из них 10% работают с металлом.
По мнению экспертов Всероссийского НИИ авиационных материалов (ВИАМ), доля РФ на мировом АТ-рынке составляет примерно 1,5%. Олег Лысак в одном из своих выступлений приводил следующие данные: в России потребляется примерно 5 — 10 тонн металлических порошков (в мире — 800 — 900 тонн), при этом каждый год показатель увеличивается всего на 3 — 5%.
В РФ, тем не менее, есть достаточно много компаний, работающих в «низком» сегменте настольных машин — Picaso, 3DQuality, «Ирвин», EGL3D, Импринта, «Зенит» и т.д. (в сумме они выпускают тысячи принтеров в год). Одновременно мы располагаем внушительным количеством центров компетенций в области индустриальной печати. Это РИЦ УрФУ, структуры Росатома, МФТИ, МГТУ им. Баумана, питерский политех, Центр аддитивных технологий Воронежсельмаша, ОДК, наконец, ВИАМ. Почти у всех есть образцы принтеров, прошедшие ряд испытаний и в принципе готовые к запуску в производство.
На Урале в АТ заинтересованы, похоже, абсолютно все территории. В Свердловской области еще в 2015-м создан консорциум «Аддитивные технологии» (участие в нем принимает региональное правительство, «Ростех», АО «Наука и инновации», Машзавод им. Калинина, ВСМПО — «Ависма», ОКБ «Новатор», «Швабе», ТВЭЛ, УрФУ и УрО РАН). Цель амбициозная — формирование замкнутого цикла АТ-производства внутри региона. Идея явно нравится власти. «Сегодня существуют все предпосылки для того, чтобы аддитивное производство стало новой специализацией области», — недавно заявил министр промышленности и науки Свердловской области Сергей Пересторонин.
В Перми на базе «Пермских моторов» и «Авиадвигателя» (оба входят в ОДК) создается Центр аддитивных технологий. Ключевая задача — поставка деталей для двигателя ПД-14 (будет устанавливаться на МС-21). По инициативе краевого правительства создан Региональный центр инжиниринга, специализирующийся на АТ и являющийся одним из элементов инфраструктуры технополиса «Новый звездный», в пермском политехе создан соответствующий центр коллективного пользования.
В Челябинской области в 2014 году при участии инфрафонда РВК создан Региональный инжиниринговый центр аддитивных и лазерных технологий. В Башкирии на базе Уфимского государственного авиационного технического университета открыли центр прототипирования и лабораторию аддитивных технологий.
Список можно продолжать, но названиями структур и проектов главную проблему не зальешь — индустриальный сектор АТ (с печатью конечных изделий из металла, пластика или керамики) в нашей стране чертовски мал, а отечественных серийных машин вовсе нет.
Понять и захватить
Выделить какой-либо один ключевой барьер, препятствующий развитию индустриального АТ-сектора, вряд ли возможно. Скорее, это сочетание массы факторов.
— Отечественные промышленники не торопятся осваивать выпуск 3D-принтеров, поскольку в текущих условиях бизнесу нужна быстрая отдача, а налаживание серийного производства аддитивных машин требует непрерывного инвестирования в течение трех-четырех лет, — комментирует Петр Москвин. — Придется возвращать из небытия высокоточное станкостроение, отрабатывать логистику, закупать оборудование.
Спрос на аддитивные машины высоким пока назвать сложно. Поскольку, во-первых, слишком дороги материалы (металлические порошки в основном завозят из-за рубежа, Русал и Северсталь только выходят на этот рынок), а во-вторых, слишком консервативны конструкторы. «Люди говорят: мы всю жизнь лили и дальше лить будем, нам не важно, что там дешевле, экологичнее, быстрее, — констатирует Москвин. — Основные потребители аддитивных машин — предприятия, которые заглядывают за горизонт 2030 — 2035 годов. Но таких пока мало. Большинство же конструкторов остались в 60-х».
Инженеры, готовые сразу работать в АТ-парадигме, пока в дефиците. «Не так давно было совещание по поводу подготовки кадров для аддитивных технологий в политехе, и мы сразу поняли, что вопрос затрагивает три факультета и пять-шесть кафедр, — констатирует проректор по науке и инновациям ПНИПУ Владимир Коротаев. — Мы сможем насытить рынок примерно к середине 2020-х. Мы понимаем, что опоздали, не начав готовить соответствующие кадры пять-шесть лет назад».
Еще один барьер — стремление к монополизации. В США промышленный АТ-сектор развивается по пути кооперации. Там есть компании, специализирующиеся только на постобработке напечатанных изделий (получение точной геометрии, снятие напряжения, колеровка, шлифовка) или онлайн-мониторинге и аналитике процессов печати, или проектировании и моделировании под АТ, или топологической оптимизации, или стратегии печати.
— В России же есть ВИАМ и ОДК, которые занимаются всем — и оборудованием, и ПО, и технологиями печати, и порошками, — посетовал на одном из выступлений Олег Лысак. — И типичный российский стартап в аддитивном секторе звучит так: «Давайте сделаем принтер, который будет что-то печатать». Попытки «распаковать» этот рынок наталкиваются на серьезное сопротивление.
Желание заниматься всем и вся ожидаемо ведет к резкому увеличению сроков и стоимости R&D и одновременно к расфокусировке с потерей контроля над качеством всех процессов.
Еще один барьер — стандарты. Нормативная база в АТ-секторе до конца не сформирована. В мае у ученых и инженеров появились два утвержденных Росстандартом ориентира. Первый дает определение АТ и разъясняет основные термины, второй описывает методы контроля и испытаний порошкового сырья. Новые ГОСТы будут введены 1 декабря. В разработке комитета, собранного на базе ВИАМ, находится еще восемь стандартов. Они должны быть приняты до конца года.
И последнее — никто до сих пор доподлинно не знает, для создания каких изделий АТ-подход более эффективен (но уже ясно, что не для всех). На что аддитивные технологии способны, получится ли «вырастить» детали и узлы с поистине выдающимися свойствами, сколько это будет стоить, нужно ли ввязываться в войну в авиации, медицине или, может, переключиться на энергетику и конечные потребительские устройства? Как написал в Forbes замглавы Минпромторга Василий Осьмаков, «глобальная конкурентная борьба ведется не на “поляне” создания аддитивных машин, принтеров и порошков, конкуренция состоит в поиске рыночных ниш применения АТ, выиграет в ней не тот, кто нарастит производство установок или сырья, а тот, кто поймет, что именно нужно печатать, для чего и в каких областях это принесет максимальный экономический эффект».
Концерн Daimler в прошлом году заявил, что переходит на печать пластиковых деталей интерьера после того, как изготовил аддитивным способом 100 тыс. изделий. Впечатляющая проверка боем. Отечественные компании пока на такое не готовы. И здесь, как нам видится, в игру должны вступить госкорпорации с гигантскими бюджетами, способные профинансировать дорогостоящие пилотные проекты.
Западные и азиатские АТ-разработчики практически не имеют технологического преимущества над отечественными. Одновременно наши машины и порошки на 30 — 40% дешевле зарубежных аналогов. Это однозначно играет нам на руку. Но если мы быстро не найдем, куда себя применить, то все преимущества будут бесполезны.