Жестокий кризис на рынке графитированных электродов поставил под угрозу развитие всего мирового металлургического комплекса. Во-первых, в этом году на ранее стабильном и даже депрессивном рынке наблюдалось настоящее ценовое ралли. За несколько месяцев цены на графитированные электроды взлетели почти в тысячу раз (см. график 1). Во-вторых, даже по новым, рекордно выросшим ценам металлургам не всегда удается договориться о поставках графитированных электродов в должном объеме и в требуемые сроки.
Напомним, что графитированные электроды применяются преимущественно в черной металлургии (85% мирового спроса), как правило для плавки в электродуговых печах. В меньшей степени они используются в цветной металлургии и литейном производстве. Причем вплоть до недавнего времени графитированные электроды считались совершенно «копеечным» расходным материалом — их доля в себестоимости стали составляла порядка 0,8%. А мощности на мировом рынке были настолько избыточными, что не металлурги искали себе поставщиков, а поставщики электродов дрались за контракты для металлургов. То есть кризис возник там, где не ждали. Тем не менее проблемы появились, и весьма серьезные.
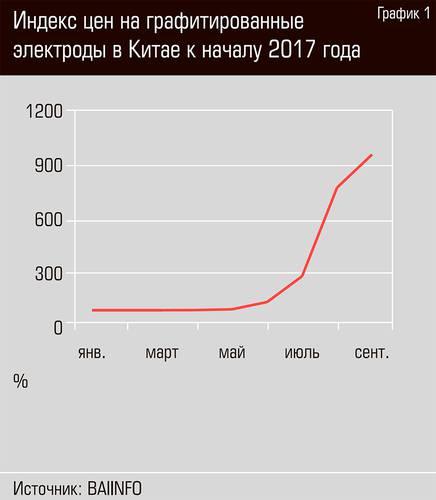
Исполнительный директор ассоциации «Русская сталь» Алексей Сентюрин отмечает, что это серьезный вызов для металлургической отрасли и беспрецедентная ситуация, которой не наблюдалось с 1990-х годов. Если положение не изменится, все это уже в ближайшее время грозит вынужденными остановками некоторых металлургических производств России, производящих сталь в электродуговых печах. «Сложившаяся ситуация для металлургов однозначно некомфортна, поскольку текущие ценовые уровни явно завышены и не были спрогнозированы ни поставщиками, ни потребителями и, соответственно, не заложены в бюджеты предприятий, — говорит Алексей Сентюрин. — С учетом действующих в России ввозных пошлин, антидемпинговой и регулярной, ценовая ситуация становится критической». Ассоциация предлагает отменить существующие пятипроцентные импортные пошлины на графитированные электроды, отказаться от антидемпинговых пошлин в 16–33%, действующих в отношении индийских поставщиков, а также настаивает на формировании под контролем ФАС политики сбыта и ценообразования для отечественных производителей графитированных электродов.
Дело уже находится на рассмотрении ФАС, а предложения по исправлению ситуации уже вызвали яростное сопротивление со стороны группы «Энергопром» (входит в «Ренову») — единственного российского производителя графитированных электродов.
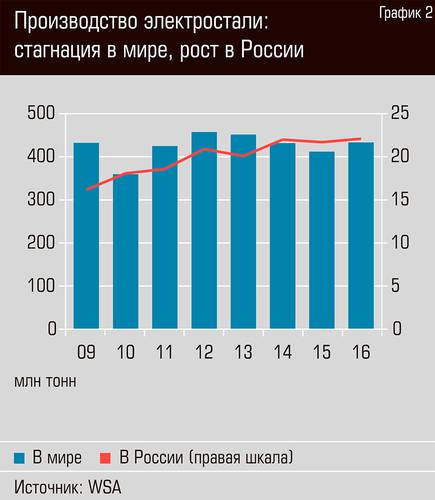
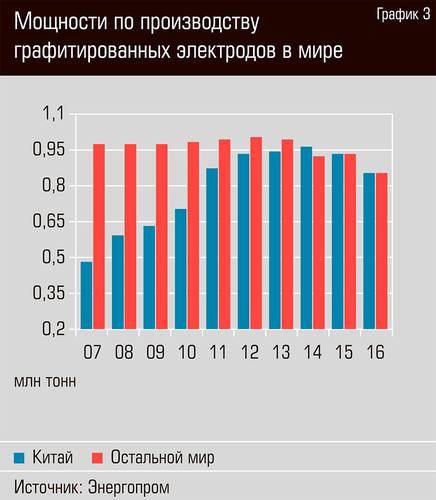
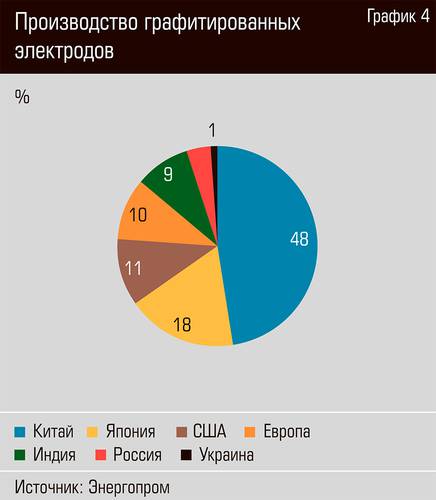
Сделать за полгода
Производственный цикл таких электродов, от сырья до готовой продукции, составляет от четырех до шести месяцев. Основное применение они находят в электродуговых печах переменного и постоянного тока различной мощности для производства электростали. Процесс этот происходит следующим образом: графитированные электроды навинчиваются друг на друга с помощью соединительного элемента, образуя свечу. Чаще всего на электродуговых печах стоят три электродные свечи по три электрода в каждой. Свеча погружается в печь, через нее пропускается ток, в результате чего между концом свечи и шихтой печи образуется дуга, расплавляющая шихту.
Существует единая международная классификация электродов по маркам в зависимости от мощности дуговых печей, для которых они предназначены. Наибольшее значение имеют электроды для сверхмощных печей (Ultra High Power, UHP). В электропечах в мире выплавляется в среднем 408–430 млн тонн стали в год. Это от 25 до 30% всего мирового производства. В России значение электростали примерно такое же: в год ее производится 22 млн тонн при общем объеме выплавки 70 млн тонн, то есть порядка 30%. Всего в мире ежегодно производится примерно 1,3 млн тонн графитированных электродов, ежегодная потребность России в них — 80–90 тыс. тонн. Стоит отметить, что роль электрометаллургии в России возрастает (см. график 2), в том числе за счет замещения устаревших мартеновских печей. Следовательно, будет расти и спрос на электроды. Так что вопрос обеспеченности металлургов этой продукцией для нашей страны совсем не праздный.
Китайцы подвели
Как же мы пришли к такому кризису? «В 2011–2014 годах, на фоне падения производства электростали в мире, в Китае наблюдался интенсивный рост мощностей по производству графитированных электродов, — рассказывает генеральный директор компании “Энергопром менеджмент” Виктор Нечуятов. — Высококачественные, но более дорогие европейские мощности закрывались, не выдерживая непрерывного и длительного ценового прессинга со стороны растущих китайских производителей. Избыток китайских мощностей провоцировал постоянное снижение цен на графитированные электроды. Снижалась и загрузка мощностей из-за падения производства электростали. Это привело отрасль графитированных электродов в депрессивное состояние. Их доля в себестоимости стального проката, производимого из электростали, например наиболее распространенной в России арматуры, к началу 2017 года упала менее чем до одного процента. В этих условиях потребители электродов привыкли в случае срочной необходимости покупать недостающие объемы на спотовом рынке и не держать у себя большие запасы. С учетом незначительного влияния на себестоимость металла мало кто считал графитированные электроды стратегически важным компонентом производственного процесса».
В самом деле, в 2007–2015 годах мировые мощности производства графитированных электродов увеличились на 28%, до 1,86 млн тонн в год. При этом китайские мощности за тот период выросли почти вдвое, с 479 тыс. до 930 тыс. тонн в год (см. график 3). На КНР к 2016 году стало приходиться немногим менее половины всего мирового производства графитированных электродов (см. график 4). Однако китайская электродная экспансия не подкреплялась ростом спроса со стороны металлургов. Десятилетие назад предсказывали, что к 2020 году мировой объем выплавки стали в электропечах превысит 900 млн тонн в год. Это более чем вдвое выше нынешних показателей (430 млн тонн в 2016 году), и теперь уже понятно, что прогнозный показатель в заявленный срок достигнут не будет.
Как результат, во всем мире наблюдалась неполная загрузка мощностей производства графитированных электродов. Если в 2007–2008 годах она превышала 90%, то к 2016-му опустилась до 70% в среднем в мире и до 60% в Китае (см. график 5). И это несмотря на масштабный вывод из эксплуатации мощностей в Европе и США, не выдерживавших конкуренции с китайцами. Только за 2013–2016 годы было закрыто электродных производств на 245 тыс. тонн в год. Затронуло это и Россию: в 2014 году прекратил работу старый Сычевский электродный завод в Смоленской области.
В целом в последние годы, по данным внешнеторговой статистики, Россия ежегодно импортировала 26–28 тыс. тонн графитированных электродов. Справедливости ради заметим, что еще 7–9 тыс. тонн продукции в год отправлялось на экспорт.
Избыток предложения сделал рынок графитированных электродов рынком покупателя и негативно влиял на цены: в 2016 году они были чуть ли не вдвое ниже, чем в 2007-м (см. график 6). А потом наступила расплата.
«Рост цен на электроды на спотовом рынке Китая начался в конце апреля 2017 года, — рассказывает Виктор Нечуятов. — К концу мая они выросли на 150 процентов, в сентябре отдельные спотовые поставки осуществлялись уже по ценам на тысячу процентов выше, чем в январе. Экологические инспекции в Китае стали останавливать “грязные” производства не только в углеграфитовой, но и во многих других отраслях: черной и цветной металлургии, производстве кремния, огнеупоров и так далее. В первом полугодии 2017 года были закрыто множество мелких заводов, производящих так называемую низкокачественную сталь на индукционных печах, которые не используют графитированные электроды. Выплавка стали в дуговых печах, напротив, пошла вверх, понадобилось больше электродов, а электродных мощностей в Китае закрыли, по нашей оценке, до 30 процентов. А это крупнейший производитель, 48 процентов от всего мира, потребитель и экспортер — 28 и 26 процентов соответственно. На этом фоне группа “Энергопром” занимает всего около четырех процентов мирового производства графитированных электродов».
То есть сначала дешевая и неэкологичная продукция выбила с рынка ряд американских и европейских производств, потом китайцы озаботились экологией — и на выходе возник рост спроса на электроды при одновременном сильном сжатии их предложения. Можно ли эту проблему решить?
«По нашим оценкам, в мире и сейчас есть существенные недозагруженные мощности по производству графитированных электродов, — говорит Виктор Нечуятов. — Но есть узкие места: это длина цикла производства графитированных электродов, достигающая шести месяцев, и дефицит сырья. Графитированные электроды для печей большой мощности марки UHP в России делают только из импортного сырья. В России это сырье не производит никто. Сырьем является так называемый игольчатый кокс, он импортируется из США, Японии и Великобритании».
Игольчатый кокс получают на установках замедленного коксования. Своим названием он обязан особенным вытянутым структурам, напоминающим толстые иглы или спекшиеся волокна. Исходным сырьем может служить как нефть (США, страны Европы), так и уголь (Япония, Китай). К слову, свою роль в кризисе сыграло и резкое удорожание угольного сырья за последний год из-за изменения трудового законодательства в Китае (см. график 7).
Освоение промышленного производства игольчатого кокса в Европе, США и Японии в конце 1960-х стало основой для настоящего прорыва в технологии производства графитированных электродов. В СССР первые лабораторные опыты по созданию технологии производства кокса игольчатой структуры были предприняты в Уфимском нефтяном институте еще в 1968 году. В 1969-м на базе малосернистой туркменской нефти получена первая опытная партия на Красноводском НПЗ.
Параллельно разрабатывались технологии получения игольчатого кокса из нефти с повышенным содержанием серы, но промышленного развития эти наработки не получали. Мировое производство игольчатого кокса сейчас составляет порядка одного миллиона тонн в год. Ежегодная потребность России при существующих мощностях по производству графитированного электрода составляет 28 тыс. тонн игольчатого кокса в год. Однако существующие мощности способны удовлетворить лишь около половины всех потребностей российской металлургии в графитированных электродах.
«Мы имеем 50 тысяч тонн мощностей при внутренней потребности 80–90 тысяч тонн. Эта ситуация обнажила проблему импортозависимости отечественной металлургии от зарубежных поставщиков графитированных электродов», — отмечают в группе «Энергопром».
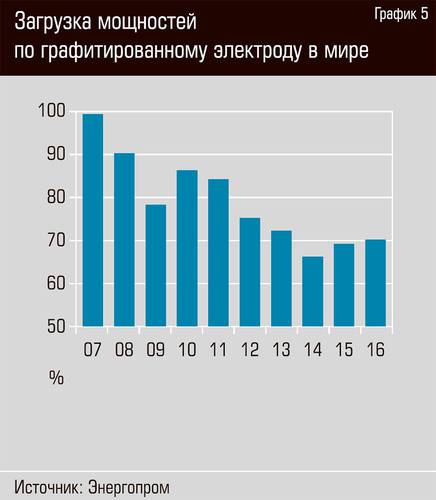
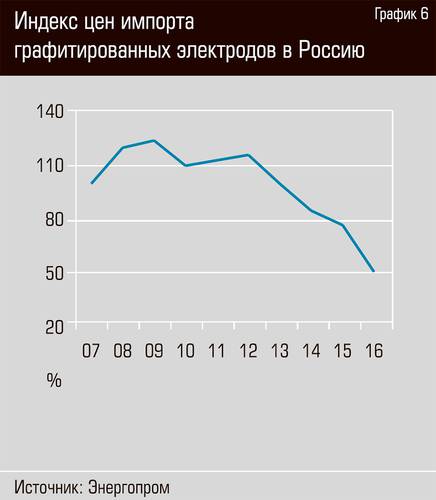
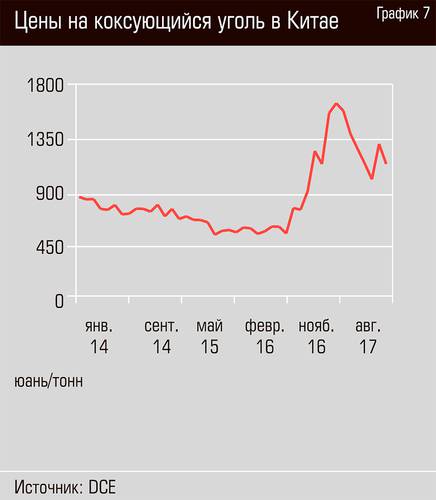
Надо договариваться?
«Важно совместно говорить: необходимы стимулы для нефтяных компаний, чтобы они развивали производство сырья, — подчеркивает Виктор Нечуятов. — Производство игольчатого кокса в России потребует инвестиций и технологий. Нефтяники говорят: мы вложимся, но кто будет эти объемы покупать, ведь требуемые вам объемы не столь значительны. Если же мы хотим сбалансировать рынок внутри России, нужно создать стимулы как для наших нефтяников, так и для производителей углеграфитовой продукции, чтобы они все же создавали дополнительные мощности. Сильно помогли бы определенные гарантии со стороны металлургов, что они эту продукцию приобретут, а это долгосрочные контракты на покупку графитированных электродов с горизонтом на 2019–2020 годы».
Позицию металлургов выражает ассоциация «Русская сталь». «С некоторыми поставщиками долгосрочные контракты действуют уже сегодня, — отмечает Алексей Сентюрин. — Для остальных поставщиков, например индийских, барьером являются действующие российские пошлины — в этих условиях заключение долгосрочного контракта, с учетом изменения его цены из-за пошлины, становится проблематичным. В отношении единственного российского поставщика металлургические компании однозначно поддерживают долгосрочные договоры. Мы понимаем, что необходимые компетенции для расширения мощностей в стране имеются. Однако до решения проблемы импортозамещения сырья и электродов однозначно необходимо снять барьеры для импорта данной продукции, поскольку от нее зависит стабильное функционирование одной из базовых отраслей российской экономики — металлургической».
В свою очередь производители электродов указывают, что расширение мощностей потребует времени (не менее двух лет) и значительных инвестиций. За это время рыночная конъюнктура может измениться, металлурги снова проторят дорожку к импортным поставщикам, а производители электродов в России останутся с продуктом, который снова не нужен, и не ясно, как окупать сделанные инвестиции.
Ранее на мировом рынке графитированных электродов уже имели место примеры агрессивного демпинга. Например, в случае с индийскими компаниями, у которых демпинговая маржа достигала 32,5% и против которых действуют антидемпинговые пошлины в России и Евросоюзе. В «Энергопроме» опасаются, что повторение подобных историй без протекционистских мер может убить отрасль, сделав зависимость отечественной металлургии от импорта вечной.
«Мы видим решение не в том, чтобы усложнить жизнь отечественным производителям электродов, то есть нам, и, убрав импортную пошлину в размере пяти процентов, позволить металлургам немного сэкономить, — говорит Виктор Нечуятов. — Сейчас доля электродов в тонне стали составляет семь-восемь процентов. Соответственно, пять процентов от восьми — это и есть тот эффект, который получат металлурги от снятия пошлин, при этом существование российского производства графитированных электродов в лице группы “Энергопром” будет поставлено под угрозу. Мы бы видели решение проблемы, скорее, в создании собственного производства сырья, то есть игольчатого кокса, в России, в создании дополнительных объемов производства электродов. Если в этом заинтересовано государство и наши потребители-металлурги, то дело за практическими действиями, которые обеспечат рынок России собственным сырьем, позволят увеличить производство графитированных электродов и уйти от зависимости, реализовав импортозамещение в нашей отрасли».
Отметим, что первые шаги к импортозамещению в этом направлении в России уже делаются. Так, на принадлежащем «Газпром нефти» Омском НПЗ в 2015 году была получена первая опытная партия игольчатого кокса. Сейчас завод реализует достаточно дорогостоящий (стоимостью 5,2 млрд рублей) проект реконструкции установки замедленного коксования, которая позволит после 2018 года получать 38,7 тыс. тонн сырого игольчатого кокса в год.
Этого еще недостаточно для удовлетворения всех потребностей российской металлургии. Однако, как показал проведенный в «Газпром нефти» анализ, при коксовании 380 тыс. тонн тяжелого газойля в год (максимальное количество сырья, которое могут в совокупности выдать две установки Омского НПЗ — каталитического крекинга и комбинированный комплекс глубокой переработки мазута) можно получить около 75 тыс. тонн сырого игольчатого кокса. При этом проектная мощность установки замедленного коксования в Омске составляет 150 тыс. тонн коксовой продукции. То есть только на омском заводе «Газпром нефти», в принципе, есть возможность выпускать игольчатый кокс в достаточном для российского рынка количестве и с перспективой увеличения.