«Импортозамещение — это неамбициозно. Импортозамещать — это значит догонять. Нужно быть впереди. Экспортировать. Не сырье: нефть, газ и зерно, — а машины и оборудование. — Глеб Белич постукивает ребром ладони по столу в такт своим словам. — Я считаю, что мы можем это делать. В малом производственном бизнесе есть наработки, есть опыт, есть успешные проекты. Мы у себя, например, сделали лучший в мире ручной инструмент для установки люверсов по соотношению цена–качество. Мы его в Германию продаем. И это только один пример».
На низком старте
Глеб окончил физический факультет Челябинского государственного университета. Но физиком-теоретиком работать не стал. Сначала было домашнее издательство, потом небольшая типография, из которой в конце 1990-х выросла рекламно-производственная фирма (таблички, сувенирка, вывески), а затем компания по производству алюминиевых профилей для рекламной отрасли. Это направление уже давно живет своей жизнью, а Глеб Белич десять лет назад основал компанию «Промкаскад». Часть выпускаемой ею продукции тоже ориентирована на рекламную сферу — оборудование для работы с пленочными материалами, устройства для установки люверсов, сами люверсы, различная фурнитура и прочие изделия, изготавливаемые методом холодной штамповки металла.
Первое производственное помещение компании располагалось в небольшой мастерской автосервиса. По мере развития бизнеса начали арендовать помещения у одного из челябинских заводов, постепенно наращивая площади. Вместе с ними рос ассортимент и количество выпускаемой продукции (миллионы штампованных изделий), а также рынки сбыта, в том числе за пределами страны. В прошлом году «Промкаскад» был признан лучшим экспортером Челябинской области в номинации «Микропредприятие». Сегодня здесь работает более 80 человек. Выпускается широкий спектр продукции, от собственно штампованных металлических изделий и различных промышленных деталей, изготавливаемых на современных металлообрабатывающих станках, до промышленных линий холодной штамповки металла, штампов, а также другого оборудования. По-прежнему особое место в ассортименте компании занимают инструменты для рекламщиков и производителей тентов для грузовых автомобилей и других тентовых конструкций (один из самых массовых продуктов компании как раз люверсы). Годовой оборот компании — более 100 млн рублей.
«Все десять лет всё, что зарабатывали, мы вкладывали и компанию, в новые разработки, в новую продукцию. Все десять лет я создавал эту ситуацию низкого старта. Мне многие партнеры говорили, мол, не майся фигней, выпускай люверсы, отточи это производство до совершенства и успокойся. Но я родился в великой стране, я что, должен посвятить жизнь люверсам? — горячится Глеб. — Вот видите, на подоконнике лежит “звездочка”? К нам пришли, сказали, что нужна такая деталь для атомных станций. Мы ее сделали! Работает теперь в атомном реакторе на Кольской станции. Или нам дали на заказ линию по производству труб из одного хитрого сплава для подводных лодок. Причем труба нестандартная. Сделали. Нам ставят задачу — мы ее решаем».
Вперед, в прошлое!
Одна из последних решенных задач — установка электровысадки. Когда-то такое оборудование изготавливалось в СССР только на одном заводе. Сейчас завода нет. Технология забыта. Кому надо — покупают импортное оборудование.
Для неискушенного человека станок делает простую на вид операцию: металлический пруток электричеством нагревается с одного конца и прессом на этом конце делается утолщение. Получается пруток с набалдашником. Последний можно превратить в головку болта или клапана для двигателя внутреннего сгорания, шаровое соединение, лопатку и так далее. Традиционным способом тот же болт изготавливается из более толстого прутка, с которого срезается лишний металл, а клапан, например, может свариваться из двух деталей — стержня и головки. В первом случае — лишний расход металла, во втором — лишняя операция, удорожающая процесс. Понятно, что болтами и клапанами применение такого рода станка не ограничивается. Так, нагрев может происходить и в середине прутка, и тогда утолщение появится именно там. Или нагреваться и утолщаться может конец трубы, на котором затем может быть нарезана резьба. Ну и так далее: любая деталь с тонкой ножкой и большой головкой может быть сделана по технологии электровысаживания.
С просьбой сделать такой станок к «Промкаскаду» обратился завод, выпускающий клапаны для двигателей внутреннего сгорания. У него резко вырос объем заказов в связи с тем, что из-за известных событий резко сократились поставки из Турции, которая традиционно поставляла в Россию клапаны для двигателей.
В «Промкаскаде» сделали компактную установку, которая быстро переналаживается и позволяет использовать металлический пруток диаметром от 8 до 30 мм. Таким образом, на ней можно делать и маленькие и большие клапаны. В мире такого нет, мировая тенденция — выпускать узкоспециализированное оборудование, утверждает Глеб Белич.
Работа над установкой заняла больше года и отняла много сил. «Чуть не издохли, — кратко комментирует Глеб итог работы и добавляет: — Заработали только убытки. Но я невероятно рад, что мы взялись за эту работу, потому что эта технология достойна того, чтобы о ней знали». В компании надеются окупить вложения за счет продажи установки и линий на ее основе другим потребителям, поскольку считают, что это оборудование может пригодиться огромному количеству металлообрабатывающих производств.
«Самая большая сложность при изготовлении этой установки была в том, чтобы свести вместе знания гидравликов, электриков, электронщиков, механиков, металловедов, — продолжает Глеб Белич. — Например, та часть пресса, которая давит на пруток, должна быть токопроводимой и одновременно выдерживать высокую температуру плавления металла и колоссальное давление. Из какого материала ее сделать? Графит лопнет. Керамика не проводит электричество. Жаропрочная сталь выгорит… Посидели в библиотеке, пообщались с людьми. В итоге взяли кусок металла от кумулятивного снаряда, попробовали. Получилось. Нашли предприятие, которое выпускает такие стали, и покупаем у него заготовки».
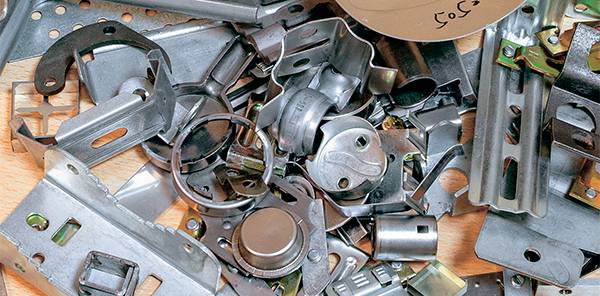
Исход из Китая
Холодная штамповка — один из самых распространенных методов обработки металла. Детали, произведенные этим способом, есть практически в любой промышленной продукции — от мебели до сложной электронной техники. Важная доля в выручке «Промкаскада» — производство на заказ металлических штампованных изделий.
Но сейчас ситуация меняется: производство оборудования — это то направление, от которого Глеб Белич ожидает в ближайшее время взрывного роста. И тому есть несколько причин. Первая, внутренняя: компания наработала нужный опыт и компетенции, чтобы производить это оборудование и штампы. Речь идет прежде всего об автоматических линиях холодной штамповки металла. Вторая причина в том, что, хотя основная масса металлоштампованных изделий в России по-прежнему китайского производства (потребители активно импортировали их последние пару десятков лет), в последнее время китайская продукция стала дорожать, да и условия работы с восточным соседом усложняются. И потому штамповочные линии от «Промкаскада» могут быть востребованными: те, кто раньше закупал готовые изделия в Китае, теперь задумываются о том, чтобы поставить собственную линию и делать их самостоятельно. Или, как минимум, начать заказывать услугу по производству штампованных изделий в России.
«Мы наконец-то решились на активную рекламу услуг штамповки, и сейчас в неделю к нам поступает ощутимый пакет заявок на расчет: люди хотят, чтобы мы посчитали, где им будет дешевле производить штампованные изделия — у нас или в Китае. Уходят люди из Китая. А что касается производства непосредственно линий, то об этом мы заявили несколько недель назад, и уже есть три заказа».
С точки зрения бизнеса «Промкаскаду» не столь важно, отдадут ему заказ на штамповку изделий или на производство всей линии, в обоих случаях он получает клиента: оборудование нуждается в обслуживании, обновлении, замене штампов. Последнее, кстати, важная составляющая. В России мало кто занимается производством сложной оснастки для прогрессивной штамповки, везут опять-таки из Китая: «Мы штампы учились делать все эти десять лет, — рассказывает Глеб. — История грустная для страны в целом. Компетенции в изготовлении оснастки практически потеряны. Так как вся штамповка ушла в Китай, туда же ушло и производство штампов. Я думал привезти специалистов из Китая, чтобы они здесь работали, делились опытом с нашими парнями. Но на китайском заводе мне прямо сказали: ты не потянешь, токарь-инструментальщик две тысячи долларов в месяц стоит, конструктор — две с половиной, и, главное, их нет. Прошли времена, когда китайские рабочие стоили дешево».
В итоге договорились о том, что штампы «Промкаскад» будет заказывать и покупать в Китае. При этом компания сама выполняет интеллектуальную часть работы — проектирует схему штамповки, пишет техническое задание. «Китайцы — это наши рабочие руки, — объясняет Глеб. — Мы на себя берем наладку, ремонты, обслуживание. В этой схеме важно, что мы можем выпускать одновременно сразу несколько штампов и при этом мы сами учимся».
Впрочем, надежда вернуть производство штампов в Россию все-таки есть.
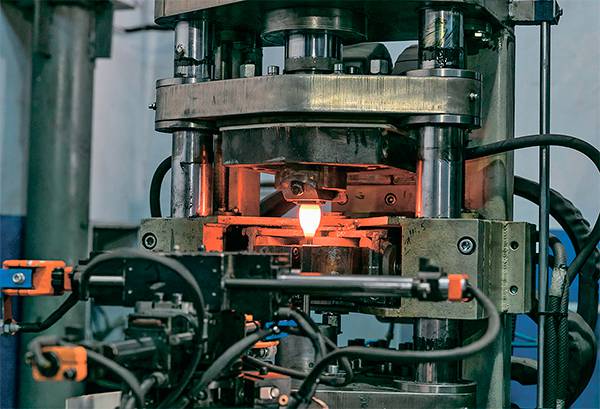
Загрузить оборонку
Глеб Белич говорит, что не знает ни одного предприятия в России, которое одновременно занимается скоростной штамповкой, проектирует и выпускает прессовое оборудование, создает линии автоматической штамповки. «Это очень трудный опыт, который сейчас становится нашим конкурентным преимуществом. Представьте, у вас есть заказ, скажем, на обувной супинатор. И мы вам его произведем на наших линиях. Потом вы решите его выпускать самостоятельно. И мы под вас создадим линию. Более того, мы обучим вас: технике, поставкам, экономике и прочему. Круто же!»
Поле для бизнеса по производству таких изделий огромное. Все дело в том, получится ли здесь обойти китайских производителей и составить конкуренцию уже им. Глеб уверен, что получится, и готов продавать оборудование желающим попробовать: «Наша проблема в том, что выросло целое поколение людей, которые даже представить себе не могут, что можно что-то делать не в Китае, а здесь, и что здесь это будет делать проще и дешевле. Это поколение непроизводственников».
Стоимость линии — от двух до пяти миллионов рублей в зависимости от сложности оборудования и комплектации. Глеб уверяет, что его оборудование получается примерно на 20% дешевле китайского: «Во-первых, линии — это всегда тяжелые вещи, прессы, чугун. Доставка из Китая будет дорогая. Во-вторых, очень важная вещь — наладка. Мы как делаем? Собрали линию на своей территории, говорим: присылайте своих специалистов, мы их обучим. Китайцы этого не предлагают». Еще одна причина — использование б/у советской техники при производстве этих линий: «Это зависит от многих факторов, иногда альтернативы нет, чугунную станину для пресса большого размера в России просто негде отлить. Да и мы все равно там поменяем и электронику, и механику… К Новому году доделаем линию для нефтяников, в ее составе есть реставрированная техника, а вот линия для изготовления номерных знаков будет спроектирована и сделана с нуля».
В свое время в холодной штамповке металла Советский Союз упустил момент технологического перехода к прогрессивной автоматной штамповке: тогда каждая операция выполнялась на своем прессе — сначала, например, вырубалась заготовка, потом она изгибалась определенным образом, потом в ней вырубалось отверстие и так далее. Каждую операцию делал отдельный человек. На некоторых предприятиях такие линии по-прежнему работают. Их замена на современные, где с одной стороны линии висит рулон металла, а с другой вылетает уже готовая деталь, позволит в разы увеличить производительность труда.
Впрочем, Глеб Белич рассматривает не только вариант производства линий на заказ, но и передачу своих наработок сторонним производителям, которые могли бы заняться производством этих средств производства.
«Два года назад, когда президент сказал, что оборонные предприятия должны освоить выпуск гражданской продукции, многие директора посмеивались, — рассказывает Станислав Твердохлеб, директор Центра развития промышленных инноваций Челябинской области. — Но сейчас они все больше задумываются о том, что они будут делать на своих мощностях, когда военный заказ сократится. И тут как раз такие малые производственные предприятия, как “Промкаскад”, могут предложить им свои разработки для воплощения их в металле. Нужно только наладить эту коммуникацию».
Это дорога с двусторонним движением: в ОПК сохранилась и научная база, и специалисты, в сотрудничестве с которыми заинтересован тот же «Промкаскад». Но, как говорит Станислав Твердохлеб, у оборонки «нет интерфейса для взаимодействия со сторонними контрагентами».
Возможно, сокращение оборонного заказа будет способствовать отладке этого самого интерфейса. «Я думаю, что сегодня военно-промышленный комплекс имеет возможность держать у себя высококвалифицированный персонал, — рассуждает Глеб Белич. — И этому персоналу было бы по плечу делать те же штампы и тем самым заменить Китай на этом рынке. Я был в Китае на заводах, где их делают и для нас, и для Европы, и для Японии и Америки. У наших оборонщиков есть нужные кадры, станки и оборудование, чтобы делать штампы на экспорт. Не говоря уже о потребностях своей страны».