Российская алюминиевая промышленность одна из самых конкурентоспособных в мире, даже несмотря на то, что цена на основной ресурс — электроэнергию — в России уже давно вышла на европейский уровень. В таких условиях без технологического перевооружения производственных мощностей невозможно конкурировать на равных ни с американскими заводами, ни тем более с китайскими. Китай обладает гигантскими алюминиевыми предприятиями, построенными за последнее десятилетие, вооружен передовыми технологиями, и конкурировать с ним особенно тяжело.
Но российскому алюминиевому холдингу «Русал» это удается. О том, какие проекты реализуются на заводах компании, «Эксперт» поговорил с техническим директором «Русала» Виктором Манном.
— Какими передовыми технологиями обладает «Русал» и как вы оцениваете его техническую оснащенность относительно мировых конкурентов?
— Когда при оценке речь идет о конкретной отрасли и стране, нужно учитывать, в какие годы она формировалась, когда была заложена база, в том числе технологическая, сырьевая и логистическая. Какие задачи тогда стояли перед отраслью, какие были приоритеты.
Первые алюминиевые предприятия в нашей стране, как и другие металлургические гиганты, были построены и создавались под нужды тяжелой промышленности в сороковые-пятидесятые годы. В тот период была важна близость к сырью и крупным транспортным артериям. Никто особо не задумывался о влиянии производства на экологию. Заводы часто строились в черте городов. Это обеспечивало производство квалифицированными кадрами. Особенности ландшафта, климат, роза ветров были факторами второго порядка. Да и, объективно говоря, за восемьдесят лет они могли значительно измениться. Все это сформировало облик отечественной алюминиевой промышленности на начало девяностых годов.
— «Русал» серьезно оптимизировал производство за последние двадцать лет. Некоторые мощности были законсервированы из-за нерентабельности и устаревших процессов, которые там использовались, особенно в европейской части страны.
— Не совсем так. Многие предприятия были перепрофилированы. Например, Волгоградский алюминиевый завод провел полную модернизацию. Теперь там, например, высокотехнологичное производство электродов мощностью 104 тыс. тонн в год. По сути, все перепрофилирование этого завода — крупнейший НИОКР. Мы полностью реконструировали все производство и теперь выпускаем там «зеленые» аноды.
— И тем не менее, насколько сильно продвинулись технологии производства алюминия на оставшихся площадках «Русала» в сравнении с серединой прошлого века, когда отрасль только зарождалась в нашей стране?
— Сегодня это практически другие заводы. А все без исключения наши новые заводы и фабрики — ХАЗ, БоАЗ, ТаАЗ, ТАФ, ВгАФ — построены по разработанным «Русалом» технологиям.
Новый виток развития начался около двадцати лет назад. За эти годы проведена модернизация старых производств, вложены миллиарды рублей. Сегодня у «Русала» производства, отвечающие самым высоким экологическим стандартам. Вновь построенные и модернизированные заводы — лидеры по внедрению наилучших доступных технологий в отрасли, причем эти технологии одновременно являются собственными ноу-хау.
— Например?
— В 2019 году в Красноярском крае была введена на полную мощность первая очередь Богучанского алюминиевого завода, который сейчас является наиболее современным и экологичным алюминиевым предприятием в мире. Все самые совершенные технологии и подходы были задействованы при его строительстве. Таким же будет и Тайшетский алюминиевый завод, строительство которого завершается в Иркутской области. Строящаяся Тайшетская анодная фабрика будет не только мировым образцом производства электродов, но и образцом применения цифровых технологий. Основной источник электроэнергии для наших алюминиевых производств — гидроэлектростанции, а доля такой безуглеродной электроэнергии составляет уже более 98 процентов. В целом новые технологии и новые производства постепенно замещают старые, и это нормальный процесс.
Революция процесса
— Тренд ясен: в Сибири есть много источников чистой безуглеродной электроэнергии. А какие направления модернизации мощностей приоритетные и как выстроена работа в этом направлении?
— Только в экологические проекты ежегодно инвестируется в среднем около ста миллионов долларов. Созданный для развития компании инженерно-технологический центр, «Русал ИТЦ», стал средоточием компетенций с передовыми инструментами математического моделирования и инженерными разработками.
— Что за решения там разрабатываются?
— Алюминиевое производство — очень энергоемкий процесс, следовательно, повышение энергоэффективности — приоритетное направление. Причем энергоэффективность как ради снижения затрат, так и ради снижения углеродного следа. Поэтому мы и инвестируем в модернизацию конструкций электролизеров. Самый очевидный путь к энергоэффективности — увеличение мощностей этих электролизеров. Это позволяет снижать расход электроэнергии и достигать лучших показателей по экологичности на единицу продукции.
На конец 2019 года были введены в эксплуатацию более 2650 энергосберегающих электролизеров и разработаны двадцать две конструкции, которые обеспечили с 2017 года экономию более пятисот гигаватт-часов электроэнергии.
Для нужд компании мы не только кардинально усовершенствовали технологии действующих заводов, но и разработали линейку самых передовых решений производства алюминия — РА300, РА400, РА550 (речь идет об электролизерах. — «Эксперт»). Эти изобретения составляют базу наилучших доступных технологий (НДТ) компании и имеют значительный потенциал и для зарубежных партнеров. Сегодня самый мощный в мире из стабильно работающих электролизеров — РА550, разработанный и испытанный в «Русале», — имеет лучшие показатели эффективности.
— А за какими технологиями будущее алюминиевой промышленности, насколько безуглеродное будущее достижимо?
— Понимаете, отечественная промышленность в силу исторических особенностей долгое время развивала гражданские направления по остаточному принципу. Сейчас Россия нагоняет этот пробел и в энергетике, и в мостостроении, и в товарах народного потребления. Но мы со своей стороны делаем все, чтобы не только догонять, но и быть ориентиром для других, особенно в экологичных технологиях. Недавно мы приступили к испытаниям нового прототипа промышленного электролизера с инертными анодами с улучшенной конструкцией и рекордно низким углеродным следом. Этот опытный электролизер придет на смену уже испытываемому в компании электролизеру с инертными анодами как следующий шаг в развитии инновационной безуглеродной технологии электролиза алюминия. Электролизер с инертными анодами нового поколения имеет ряд принципиально новых технических решений, позволяющих повысить чистоту производимого алюминия и одновременно снизить углеродный след до рекордно низкого уровня — две тонны на тонну алюминия. Этот проект выведет алюминиевую промышленность на совершенно новый уровень, создаст новые стандарты.
Другой пример: электролизеры «Русала» используют уникальный и единственный в мире есo friendly материал и технологию футеровки электролизеров, которая при капитальном ремонте не требует захоронения использованных материалов на полигоне, а возвращает их в новую футеровку.
— А какие еще собственные разработки вы используете?
— Таких много. Один из ярких примеров эффективной экологической разработки — технология «ЭкоСодерберг». Благодаря конструктивным улучшениям и очистке газов показатели «ЭкоСодерберга» по основному маркерному веществу — фторидам — в три с половиной раза лучше типовой технологии. Кроме того, воссозданная в «Русале» школа систем газоочистки позволила создать инновационную систему очистки. Она близка по эффективности к ста процентам, экономична по материалам и энергоэффективна.
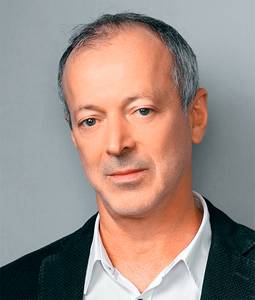
Экология на всех фронтах
— «Русал» — это не только производство алюминия, но и его переделы. Наверняка тут тоже есть место инновациям?
— В последние годы компания активно занимается проектами, связанными с разработкой и внедрением оборудования для литья и обработки металлов давлением. Вот уже более пяти лет «Русал» выпускает литейную оснастку для производства плоских слитков.
Особой своей гордостью мы считаем технологию для получения катанки под торговой маркой EXTRUform. Эта технология была высоко оценена в мире, и мы даже продали лицензию на производство оборудования мировому лидеру — немецкой компании SMS. Изюминка технологии в том, что нам удалось в одном технологическом узле объединить процессы прокатки и прессования. Это позволило создать высокопроизводительную технологию изготовления высококачественной катанки из алюминиевых сплавов. Те продукты, которые раньше изготавливались только низкопроизводительным методом прессования, сейчас можно делать быстрее в семь–десять раз.
Но, по моему мнению, самое главное среди всех улучшений то, что за последние двадцать лет в «Русале» поменялась сама логика принятия инвестиционных решений и любой проект руководство компании оценивает прежде всего с точки зрения влияния на окружающую среду. Если разработка не ведет хотя бы в какой-то части к экологическим улучшениям, то от нее просто отказываются.
В целом в компании есть ряд требований к новым технологиям: они должны быть экологичными и экономически выгодными. Кроме того, это требование к качеству, взвешенное импортозамещение, умное цифровое производство.
— Что происходит в сырьевом блоке?
— Новые технологии, в том числе энергоэффективные, мы внедряем и на глиноземном производстве. Так, на одном из флагманов отечественной глиноземной промышленности — Уральском алюминиевом заводе — выполненные за последние шесть лет проекты по модернизации технологии позволили повысить производительность по глинозему с 770 до 912 тысяч тонн в год. При этом мы снизили расход энергии с 19,5 до 17,8 гигаджоулей на тонну.
У нас амбициозный план: в ближайшие десятилетие еще на девять-десять процентов повысить энергоэффективность на всех глиноземных заводах компании, а также снизить расход каустической соды минимум на сто тысяч тонн в год.
— Звучит хорошо. Тем не менее сейчас в нашей стране, да и во всем мире, очень остро стоит необходимость увеличения переработки и образования отходов, как бытовых, так и промышленных. Вы такую работу ведете?
— За последние десять лет «Русал» переработал и реализовал более половины образованных алюминиевыми заводами отходов. Отдельные виды отходов мы реализуем на сторону, потому что они являются качественным сырьем для потребителей из других отраслей. И перед заводами поставлена задача реализовать все коммерчески востребованные отходы.
Переработка шлама глиноземных предприятий — как красного, так и нефелинового, — составила около десяти процентов, и по этому показателю «Русал» — лидер среди алюминиевых компаний мира. Но мы не останавливаемся и сейчас тестируем инновационную технологию переработки красных шламов — основных отходов глиноземного производства, которые содержат ценные оксиды металлов, в том числе скандия. Уже есть технология извлечения скандия из красных шламов, однако нам нужно снижать себестоимость изготовления оксида скандия. Как только мы увидим экономическую модель, можно будет строить фабрику по его производству.
Второй по значимости вид производственных отходов в компании — отработанная угольная футеровка электролизеров. В прошлом году доля ее переработки превысила 78 процентов. К примеру, на Саяногорской промплощадке уже сейчас более 90 процентов отходов перерабатывается или реализуется потребителям. Это ориентир для всех предприятий «Русала».
Две головы лучше
— Кто ваш партнер в разработке новых технологий для производства?
— В современной промышленности не вести собственные исследования — это путь в никуда. Тот, кто обладает лучшими технологиями, определяет правила игры и в металлургической, и в автомобильной и в авиакосмической, и в любой другой отрасли. Перефразируя известное утверждение, «кто не вкладывает в свои технологии, обречен на зависимость от чужих». У «Русала» есть собственная научная база, а также история сотрудничества с ведущими техническими вузами страны, такими как СФУ, МГУ, МИСиС, УрФУ, ИрНИТУ, и исследовательскими институтами РАН.
— Где основные центры компетенций?
— Один из основных центров — Институт легких металлов и технологий (ИЛМиТ), созданный совместно с МИСиС в 2017 году. Он сфокусирован на создании новых алюминийсодержащих продуктов. Большинство специалистов — молодые ученые и инженеры, которые когда-то учились в вузах, с которыми мы работаем. На исследования мы направляем порядка двадцати миллионов долларов ежегодно. Экспертный совет, действующий в «Русале», оценивает все поступившие идеи, определяет релевантные проекты.
Сейчас в ИЛМиТе в разработке уже более двадцати видов новой продукции и двенадцать R&D-проектов. Оборудование этого института позволяет не только создавать, но и испытывать новинки по всем параметрам и свойствам: прочность, устойчивость к коррозии, деформации. ИЛМиТ, кстати, включился в международную гонку создания материалов для самого легкого экологического транспорта со сниженными выбросами парниковых газов.
Кроме того, алюминий может применяться и в строительстве, и в других традиционных отраслях, а также на перспективных направлениях.
— Много разработок ведется внутри самой компании?
— Да, например, у нас есть Центр аддитивных технологий и комплексного инжиниринга. Центр позволит за счет комплексных алюминиевых материалов, компьютерного инжиниринга и 3D-печати создавать самые легкие детали сложной формы, которые невозможно получать традиционными методами литья и обработки металлов.
Другое направление разработок — скандийсодержащие сплавы алюминия. Такие сплавы нужны автопрому, кораблестроению и аэрокосмосу. В компании создается стартап по получению скандийсодержащих продуктов, от оксида и лигатуры до Al-Sc-сплавов и легирующего алюминия.
Можно также выделить стартап «Русала» по созданию экологичного продукта — высокодисперсного гидроксида алюминия. Этот продукт позволит совершить переворот в технологии изготовления кабельных пластикатов, а в дальнейшем в производстве ПВХ. Этот материал приходит на смену галогенным антипиренам (противопожарные добавки в пластики. — «Эксперт»), выделяющим вредные газы при горении.
Гонка за цифрами
— Сейчас многие компании видят возможности в цифровизации производства. Внедряет ли «Русал» на своих промплощадках цифру?
— Конечно. Все новые технологии компании разрабатываются в комплексах математического моделирования — ANSYS, StarCD, SisCAD, CFD. Реализуются также конкретные проекты по цифровизации производства. На промплощадке в Саяногорске действуют пилотные участки по модернизации сетевой инфраструктуры, развитию системы технического учета и телеметрии энергообъектов, внедрению современной системы управления производственными процессами (MES-системы).
На Красноярском заводе разрабатывается автоматизированная логистическая система управления транспортом. На сибирских предприятиях также внедряется информационная система литейного производства и продолжается обновление систем управления технологическим процессом, разрабатываются и используются 3D-модели создаваемых объектов.
На Красноярском алюминиевом заводе создана роботизированная система детектирования нарушения герметизации электролизеров. Там используется технология цифрового преобразования видеосигнала. Система позволяет автоматически определить возникновение дымков, пламени и других нарушений герметизации.
Для повышения эффективности алюминиевого производства «Русал» разрабатывает систему управления технологическим процессом электролиза на основе прогнозной аналитики (Big Data). Внедрение технологии позволит диагностировать причины снижения производительности электролизеров, подбирать оптимальные условия в зависимости от текущего состояния оборудования, прогнозировать нарушения и, что самое важное, предотвращать их.
— Как скоро ждать внедрения?
— Сейчас пилотный проект идет на нескольких сибирских заводах «Русала». Важно, что разрабатываемая система подразумевает тиражирование без существенных дополнительных затрат на другие площадки компании.
— А государство как-то стимулирует внедрение инноваций промышленностью?
— У нас сложились хорошие взаимоотношения с Минпромторгом, Министерством науки и высшего образования России, которые прилагают серьезные усилия для внедрения новых технологий. В мире много программ, которые поддерживаются на государственном уровне. Например, компания Hydro на разработку энергоэффективных конструкций электролизеров для производства алюминия получила специальный грант от правительства Норвегии. Увеличение количества таких программ в России, конечно, поможет скорее реализовать сложные, но важные в долгосрочной перспективе для экономики нашей страны задачи. Хотелось бы, чтобы все контролирующие органы включали в свой KPI количество новых производств, проектов в регионе, стране, которые они успешно сопровождали. Это существенно ускорило бы реализацию новых проектов, повысило привлекательность инвестирования в новые технологии и производства.