Научно-производственное объединение «Урал» пятнадцать лет выпускает изделия из полимерных и композитных материалов для замены в узлах различных механизмов соответствующих деталей из бронзы и баббита. Однако история компании насчитывает без малого тридцать лет — один из первых кооперативов в Челябинской области создан в июле 1988 года. Впрочем, основной принцип — делать то, чего больше не делает никто, — был выработан уже тогда.
Не числом, а умением
На первом этапе компания занималась изготовлением и ремонтом деаэраторов (устройство по удалению газов из жидкости) для тепловых электростанций.
«Работали мы по всей территории СССР, — рассказывает технический директор НПО “Урал” Виталий Павлов. — В Министерстве энергетики существовала очередь на наши услуги. Ждали, когда мы приедем и сделаем».
Виталий Павлов окончил Челябинский политехнический институт, факультет «Двигатели, приборы, автоматы». Долгое время работал на кафедрах двигателей летательных аппаратов и атомных электростанций. Управленческий и организационный опыт получал в стройотрядах, сначала в качестве рядового бойца, а потом и командира: «Мне все время надо что-то новое создавать. Я не могу мыслить иначе. Если надо что-то сделать, я начинаю думать, как это сделать проще, хитрее, дешевле и так далее».
На следующем этапе компания занялась спутниковым телевидением. Устанавливали в населенных пунктах спутниковые антенны, ретрансляторы, обеспечивали людям возможность смотреть спутниковые каналы. Работали в своей Челябинской области и в соседних регионах — Башкирии и Оренбургской области. Губернатор последней в какой-то момент понял, что часть электората смотрит не местное ТВ, а кабельные каналы, которые в период выборов могут начать показывать совсем не то, чего хотелось бы власти. Так что с этим видом деятельности пришлось расстаться.
Переключились на каслинское литье. Знаменитый Каслинский завод художественного литья обыкновенно окрашивал отлитые из чугуна изделия в радикальный черный цвет. НПО «Урал» построил линию гальванопокрытий. «Перекрашивание» чугуна под бронзу или серебро позволило подчеркнуть и выделить все тонкие детали каслинского литья, придало ему совершенно другой вид. Но вскоре к руководству заводом пришли новые люди, выставившие партнерам более жесткие условия. В НПО «Урал» их посчитали неприемлемыми.
«После того как мы прекратили работать с каслинским заводом, однажды ночью раздался звонок, — вспоминает Виталий Павлов. — Звонили из США. Мы им отправляли партию литья с гальванопокрытием. И сказали, что рассмотрели наше предложение и готовы брать каслинские изделия в неограниченном количестве. Я говорю: “Ребята, месяца бы на два раньше, и все бы получилось. А сейчас всё — вокзал ушел”».
Впоследствии собственник и руководство каслинского завода вновь поменялись, сейчас он входит в состав компании «Мечел». Однако возвращаться к этой теме Виталий Павлов уже не хочет: «Мне их подход не нравится. Они измеряют художественное литье в тоннах. А надо — в штуках. И продавать через аукцион, брать не массовостью, а эксклюзивностью».
Место силы
На каслинском заводе Виталий Павлов встретил знакомого из Челябинского политехнического института, который предложил заняться полимерами. В частности, подшипниками из них, так как он защитил по этой теме диссертацию и имел определенные наработки. Первым крупным заказчиком стал Магнитогорский металлургический комбинат (ММК). Импортные подшипники на прокатном стане, которые часто выходили из строя, попробовали заменить на полимерные. Получилось. Предприятие получило заказ — 500 штук в месяц. Дальше — больше. ММК предложил поставить на блюминг пластмассовые вкладыши, а не бронзовые.
«Мы сделали. Звонят, говорят — сломался. Еще один сделали. Сломался. Ну, думаю, надо кончать эти эксперименты, пока серьезная авария не случилась. А начальник цеха Магнитки против, мол, давайте еще попробуем, должно получиться. Тут наш специалист из ЧПИ говорит, что если прокипятить пластмассу, то она станет менее хрупкой. Сделал он какое-то корыто, поставил тэны. Я подошел: что за кипятильня? Она почти и не кипит. Сейчас, говорю, я вам сварю. И сделал скороварку, грубо говоря. Загрузил, закрутил. А товарищ говорит: я против. Я, мол, за это отвечаю, это мое направление. А я говорю, что в нашей фирме за все отвечаю я. Не нравится — отойди, посмотри со стороны. Сварили. Отправили. Через две недели звонок: “Если у вас это не случайно получилось, то приезжайте договор подписывать”. Товарищ говорит: “Ну ладно. Я вам больше не нужен, и вы мне больше не нужны”. И ушел. С той поры у нас это пластмассовое направление стало активно развиваться. Потому что он нас тормозил. Для него это была не работа, а хобби. Да и когда мы что-то зарабатывали, он очень болезненно воспринимал наши предложения станок какой-нибудь, например, купить. Зачем, мол? Давай поделим, да и все».
Вкладывать заработанное в покупку нового оборудования — еще одна принципиальная позиция НПО «Урал». Порядка 30–40 млн рублей в год отправляется на развитие компании. И при этом за всю свою историю предприятие ни разу не брало кредиты.
«В четвертом квартале 2008 года оборот у нас упал на 80 процентов, — рассказывает генеральный директор компании Мария Эйдельштейн. — И выжили мы только потому, что никому ничего не были должны. Мы только в 2016 году получили в общей сложности шесть миллионов рублей дотаций от местных и федеральных властей. Это компенсация за купленное новое оборудование. Мы теперь обязаны в течение определенного времени сохранять среднесписочное число работников». Их, кстати говоря, 150 человек. И, по словам Марии Эйдельштейн, текучка кадров — минимальная. А 32 человека и вовсе работают в компании более десяти лет.
Заводов в Челябинской области много, круг заказчиков стал расширяться. Постепенно он вышел и за пределы региона. Сейчас в числе заказчиков — металлургические и трубные заводы, лифтостроительные заводы, производители автокранов и грузовиков, предприятия нефтегазовой и горнорудной промышленности. Компания выпускает более 17 тыс. наименований продукции: плиты скольжения, втулки, гайки, подшипники, ролики, направляющие и прочее.
Один из главных заказчиков — КамАЗ. Сотрудничество началось с внедрения композитной втулки балансира заднего моста. Внедряли два года. Зато завод сэкономил на этой замене 1,2 млрд рублей за несколько лет. А НПО «Урал» зарекомендовало себя на заводе как компания с высоким интеллектуальным уровнем, решающая сложные задачи. Одной из них стала задача по замене бронзовой втулки в сателлите дифференциала заднего моста на полимерное покрытие. Не с первого раза, но получилось. Пятнадцатимикронное напыление заменило бронзу. Получилось и дешевле, и долговечнее. Таких сателлитов НПО «Урал» поставляет более 1 млн штук в год.
«То, что можно сделать на термопластавтомате, могут скопировать конкуренты, документация порой к ним утекает, но наше качество они повторить не могут. Нам звонят со всей России и просят напрямую поставить именно наши втулки. А вот что касается сателлитов, то здесь никто, кроме нас, не знает, что именно напыляется на металл, и еще долго никто не сможет повторить этот успех, — говорит Мария Эйдельштейн. — Нам интересно делать то, чего другие делать не могут. Можно, конечно, тазики отливать, но их же еще надо суметь продать, а мы предлагаем то, чего нет, сами формируем рынок и создаем спрос».
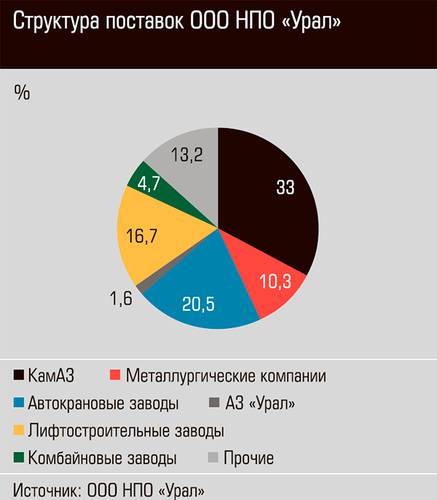
«Делать тазики нам гордость не позволяет, — поддерживает Марию Виталий Павлов. — Полимерами занимаются многие. Но получается не у всех. Пластмасса — это такая тонкая штука. Как игра на скрипке. И в каждой нашей детали есть свои маленькие хитрости. Можно повторить, да. Но сначала придется вложить десятки миллионов в оборудование. Одна RIM-установка*, которую мы заказывали в Германии, стоит 16 миллионов. Таких в мире и десяти штук не наберется. А мы ее еще и дорабатывали, чтобы она могла отливать детали весом до 150 килограммов, а не максимум 20, как было вначале».
НПО «Урал» запатентовало полиамиды собственной разработки под торговой маркой «Аркаим».
Аркаим — древний город в Челябинской области, открытый в конце 80-х годов прошлого века. Люди жили здесь примерно четыре тысячи лет назад. Считается, что они обладали довольно развитыми для того времени технологиями. Некоторые наши особо впечатлительные современники полагают, что это поселение находится в некоем месте силы, где в одной точке сходится энергия космоса и земли.
Сила НПО «Урал» — в ее инженерной составляющей. Здесь не просто изготавливают деталь по чертежу заказчика. Конструкторы компании изучают весь узел, при необходимости меняют конструкцию детали, улучшая ее функциональные возможности.
В середине марта на предприятие приезжала делегация КамАЗа — обсудить, что еще могла бы делать уральская фирма для автозавода: «Они меня спрашивают: можете вот это сделать? Можем, говорю. Но подготовка производства для каждой детали стоит несколько миллионов рублей. А мы, говорят, знаем, но у нас на заводе принято решение: теперь можно финансировать подготовку производства у поставщиков. Если они будут финансировать, то мы резко вырастем, там можно много еще чего сделать», — считает Виталий Павлов.
Сейчас НПО «Урал» разрабатывает для КамАЗа воздушный баллон (ресивер) из пластика. На каждом грузовике таких баллонов, работающих в тормозной системе, — шесть штук. Металлических. Они тяжелые и подвержены коррозии. Пластиковый ресивер будет практически вечным. В компании внедрили очередное ноу-хау, идут испытания: «Такой технологии ни у кого нет. Я недавно в журнале вычитал, что над ней работает несколько фирм в Германии. Но до внедрения им еще далеко. А мы уже пытаемся получить готовый продукт», — говорит Виталий Павлов.
В работе также водяной насос для КамАЗа, сделанный из пластика, а не из металла. Пока предполагается поставлять его как запчасть, а если все пойдет хорошо, то и на главный конвейер.
Преимущества очевидны
В планах компании — дальнейшее расширение. В ближайшее время будет закуплен новый роботизированный термопластавтомат, уже построено новое здание, подготовлено место еще для одного. Есть планы существенно — вдвое — увеличить штат.
Идет работа и по расширению круга заказчиков.
Например, НПО «Урал» с 2010 года сотрудничает с заводом «Клевер», который входит в группу компаний «Ростсельмаш». «Клевер» занимается производством прицепного и навесного оборудования для сельхозтехники. Замена металлических деталей на пластмассовые позволяет, в частности, уменьшить вес конструкций. Однако если с «Клевером» сотрудничество налажено, то с головной компаний, «Ростсельмашем», пока никак не получалось. Хотя поле для совместной деятельности широкое — на каждом комбайне большое количество передаточных шкивов и ремней. Замена металла на пластик позволит уменьшить вес всего агрегата, да и, как утверждают в НПО «Урал», обойдутся пластиковые детали дешевле. При этом в компании могут ради интересного заказа провести все НИОКР и выдать готовую деталь на испытания за свой счет. Если считают, что заказ интересный и перспективный.
«Однажды на одном мероприятии я попросила Станислава Твердохлеба подвести меня к нашему челябинскому министру экономического развития Сергею Смольникову, — рассказывает Мария Эйдельштейн. — Станислав — директор местного Центра развития промышленных инноваций, активно занимается промышленной кооперацией, многих знает и в бизнесе, и во власти. В общем, я у Сергея Александровича попросила его личную почту и написала ему письмо. Объяснила все, так, мол, и так, прошу посодействовать в налаживании связей с компанией “Ростсельмаш” и Щербинским лифтостроительным заводом. Сработало. В ответ на письма министра от обеих компаний пришли ответы, предлагают обсудить возможное сотрудничество. Будем разговаривать».
Впрочем, в части увеличения количества партнеров-заказчиков хорошо работает и сарафанное радио.
«Мы поработали с одним автокрановым заводом, заменили часть металлических деталей на пластмассовые. Они привезли свой кран на выставку в Москву, там их коллеги-конкуренты увидели и тоже пришли к нам, — рассказывает Виталий Павлов. — Если раньше я носился по всей Российской Федерации, искал заказы, то теперь часто нас ищут».
*Технология RIM (от англ. Reaction Injection Molding) заливка полимера в оснастку под низким давлением.